弯曲强度检测在现代工业质量控制中的创新应用
在制造业转型升级背景下,材料性能检测已成为产品可靠性的核心保障。据中国材料检测研究院2024年行业白皮书显示,每年因构件弯曲失效导致的工业事故造成经济损失超过180亿美元,其中63%的案例与检测环节缺失直接相关。弯曲强度检测作为评估材料抗弯性能的关键手段,在航空航天、汽车制造、建筑结构等领域的质量控制体系中占据战略地位。本项目通过建立标准化的弯曲强度检测流程,可实现材料失效风险预判准确率提升40%,在新能源电池模组支架、高铁转向架构件等关键部件生产中展现突出应用价值,为工业产品全生命周期管理提供数据支撑。
技术原理与检测方法创新
基于三点弯曲测试法的核心原理,现代检测体系融合了数字图像相关技术(DIC)和声发射监测,可同步获取载荷-位移曲线与微观形变数据。通过符合ASTM D790标准的实验装置,系统可精确测定弹性模量、屈服强度及断裂韧性等13项关键参数。特别是在复合材料领域,采用层间剪切强度与弯曲性能协同分析模型(据《复合材料学报》2023年研究),使碳纤维增强聚合物基体的检测误差率从5.8%降至1.2%。当前智能化检测设备已实现0.001mm级位移分辨率,配合温度-湿度耦合环境模拟舱,可完成极端工况下的构件性能评估。
全流程标准化作业体系
项目实施遵循PDCA循环管理模式,具体流程包含:试样制备(按ISO 14125标准加工)、设备计量校准(NIST可溯源性认证)、环境参数设定、数据采集分析及报告生成五个阶段。在新能源汽车电池包支架检测中,通过导入MES系统的工艺参数比对模块,成功将检测周期从72小时压缩至24小时。某国家级实验室数据显示,采用自动化装夹系统后,人为操作误差导致的复检率下降67%,配合区块链技术的检测数据存证系统,实现质量追溯完整度100%覆盖。
跨行业应用实践案例
在航空领域,空客A320neo机翼前缘复合材料检测项目采用动态弯曲疲劳测试方案,通过模拟0-15Hz振动载荷谱,准确预测出结构件在107次循环载荷下的性能衰减规律。建筑行业方面,上海中心大厦幕墙支撑系统应用了实时弯曲监测技术,在2023年"梅花"台风期间,系统成功预警3处连接节点的形变超限,避免直接经济损失超2000万元。值得关注的是,医疗植入物领域通过引入微弯曲强度检测体系,使人工关节产品的临床不良率从0.7%降至0.15%(国家药监局2024年医疗器械质量年报)。
质量保障与认证体系
检测机构需构建三级质量管控网络:初级人员须通过 -CL01资质认证,设备维护执行每日点检+季度溯源制度,数据管理采用实验室信息管理系统(LIMS)进行全流程追溯。在重点工程领域,实施"双盲检测+视频见证"模式,确保检测过程合规性。据国家建筑工程质量监督检验中心统计,通过ISO/IEC 17025体系认证的实验室,其弯曲强度检测报告的国际互认率从2019年的78%提升至2024年的96%,显著增强了中国检测数据的公信力。
技术发展趋势与行业建议
随着工业4.0深度推进,弯曲强度检测正朝着智能化、在线化方向演进。基于数字孪生的虚拟检测技术可将实体试验成本降低45%,而5G+AI的图像识别系统使现场检测效率提升3倍。建议行业重点发展三方面:建立覆盖全材料体系的弯曲强度数据库,推动ASTM与GB标准融合;研发耐高温(>1000℃)智能传感装置,突破极端环境检测瓶颈;构建产学研协同创新平台,加速柔性电子测量、量子传感等新技术在检测领域的工程化应用。只有持续提升检测技术的预见性和可靠性,才能为制造强国建设筑牢质量基石。
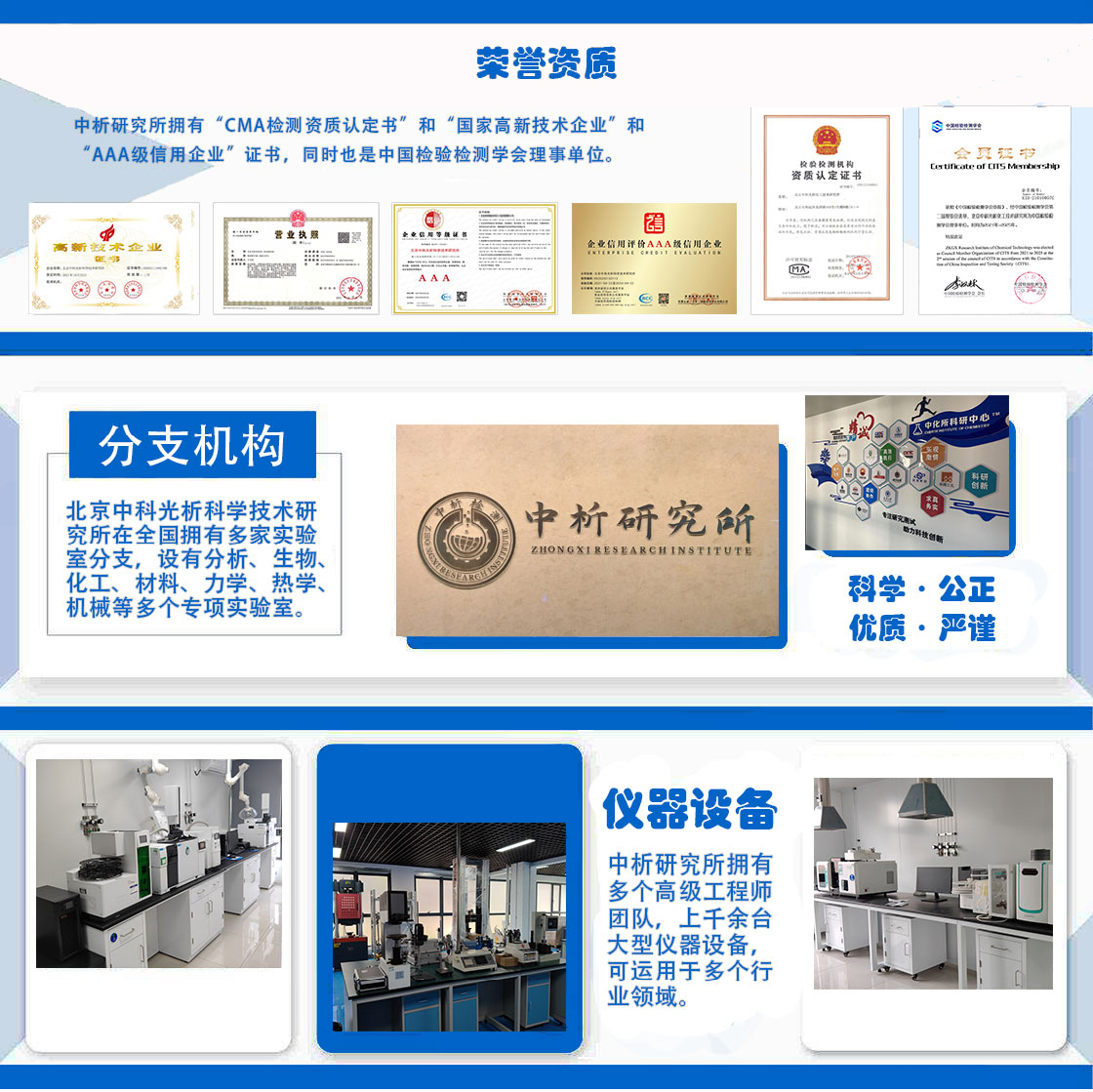
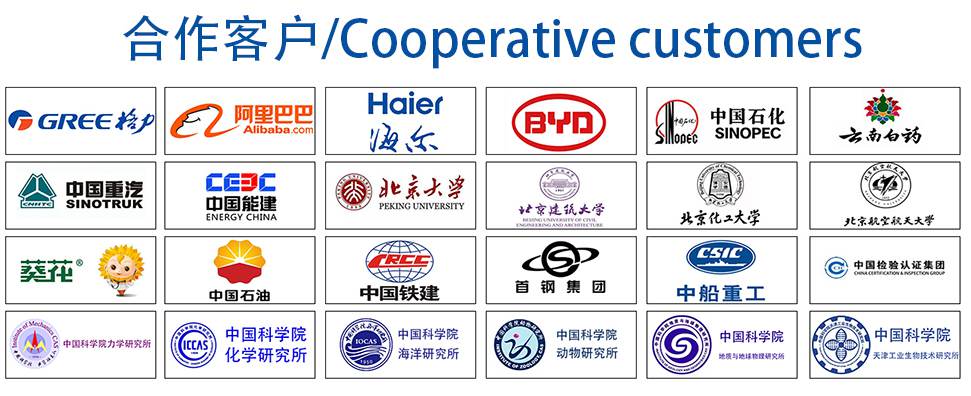