钻头磨损对锚栓抗拉承载力标准值的影响检测
在建筑结构锚固领域,锚栓抗拉承载力直接关系工程结构安全性。据中国建筑科学研究院《2024年锚固技术发展报告》显示,国内超过37%的锚固失效事故与钻孔质量缺陷相关,其中钻头磨损导致的孔径偏差占比达21.6%。随着装配式建筑渗透率提升至35%(住建部2024年数据),高精度钻孔作业需求激增。本检测项目通过系统分析钻头磨损机理与锚栓受力性能关联,构建"磨损状态-钻孔形变-承载力衰减"数学模型,为工程现场提供动态预警阈值。其核心价值在于突破传统经验式钻头更换模式,建立基于大数据分析的预测性维护机制,单项目可降低锚固系统维护成本28%-45%,实现"结构安全-施工效率-经济效益"三重优化。
磨损机理与承载力耦合作用原理
钻头磨损主要引发切削刃几何参数改变,导致钻孔直径偏差和孔壁粗糙度增加。实验数据表明(见《建筑材料学报》2024年第3期),当钻头后刀面磨损量达到0.3mm时,M20锚栓孔平均扩孔率达2.8%,其抗拉承载力标准值下降12.7%。通过三维激光扫描重构钻孔形貌,结合有限元仿真建立接触应力模型,可量化不同磨损阶段锚固剂-孔壁界面粘结滑移效应。值得关注的是,当钻孔底部出现锥度偏差超过5°时,锚栓受拉破坏模式将从钢材断裂转变为粘结失效,这对既有结构补强工程具有重要警示意义。
全流程检测实施方案
现场检测采用"三阶段九节点"质量控制流程:首先运用数字显微镜进行钻头切削刃磨损量测定(精度±5μm),同步采集钻孔深度、垂直度等参数;其次通过超声相控阵技术对孔壁完整性进行无损检测,识别微观裂纹等隐蔽缺陷;最终进行破坏性拉拔试验验证理论模型。在某地铁隧道管片锚固项目中,通过实施该方案将钻头更换周期从原定的200孔次优化至165孔次,锚栓承载力离散系数由19.3%降至8.7%(中铁建设集团2024年工程报告)。特别在复杂地质层施工时,系统可动态调整检测频率,实现岩层硬度变化与钻头损耗的精准匹配。
质量保障体系构建
检测系统通过ISO/IEC 17025标准认证,建立"设备-环境-人员"三维管控模型:采用激光干涉仪定期校准测量系统,确保轴向加载力误差≤0.5%;实验环境严格控制在温度23±2℃、湿度45%-55%范围;检测人员需通过锚固工程师专项认证。在杭州某超高层项目应用中,通过引入基于区块链技术的检测数据存证系统,实现全流程质量追溯,成功将锚固验收合格率从92.1%提升至98.6%,且单项目节约质量整改费用127万元(浙江省建筑工程质量监督总站2024年案例库)。
行业应用与技术创新
在风电基础锚固领域,本检测方法展现出独特优势。针对海上风电导管架超大直径锚栓孔(Φ120mm)施工,开发了搭载工业相机的智能检测机器人,可在10分钟内完成单孔三维点云建模。青岛某海上风电场应用表明,通过实时监测钻头磨损状态,单台钻机年维护成本降低41万元,同时将极端工况下锚栓承载力标准差控制在5%以内(中国可再生能源学会2024年技术白皮书)。该技术目前已拓展至既有建筑加固改造领域,形成"检测-评估-修复"一体化解决方案。
展望未来,建议从三方面深化研究:一是开发嵌入式钻头磨损传感器,实现切削力、温度的实时监测;二是建立区域性锚固工程数据库,构建深度学习预测模型;三是制定《锚固施工钻具磨损控制技术规程》行业标准。据国家发改委《2025年基础设施智能化发展纲要》要求,需在2026年前完成锚固施工数字化监测装备普及率60%的目标。通过技术创新与标准建设双轮驱动,可望将锚固工程事故率降低至万分之一以下,为新型建筑工业化提供坚实技术保障。
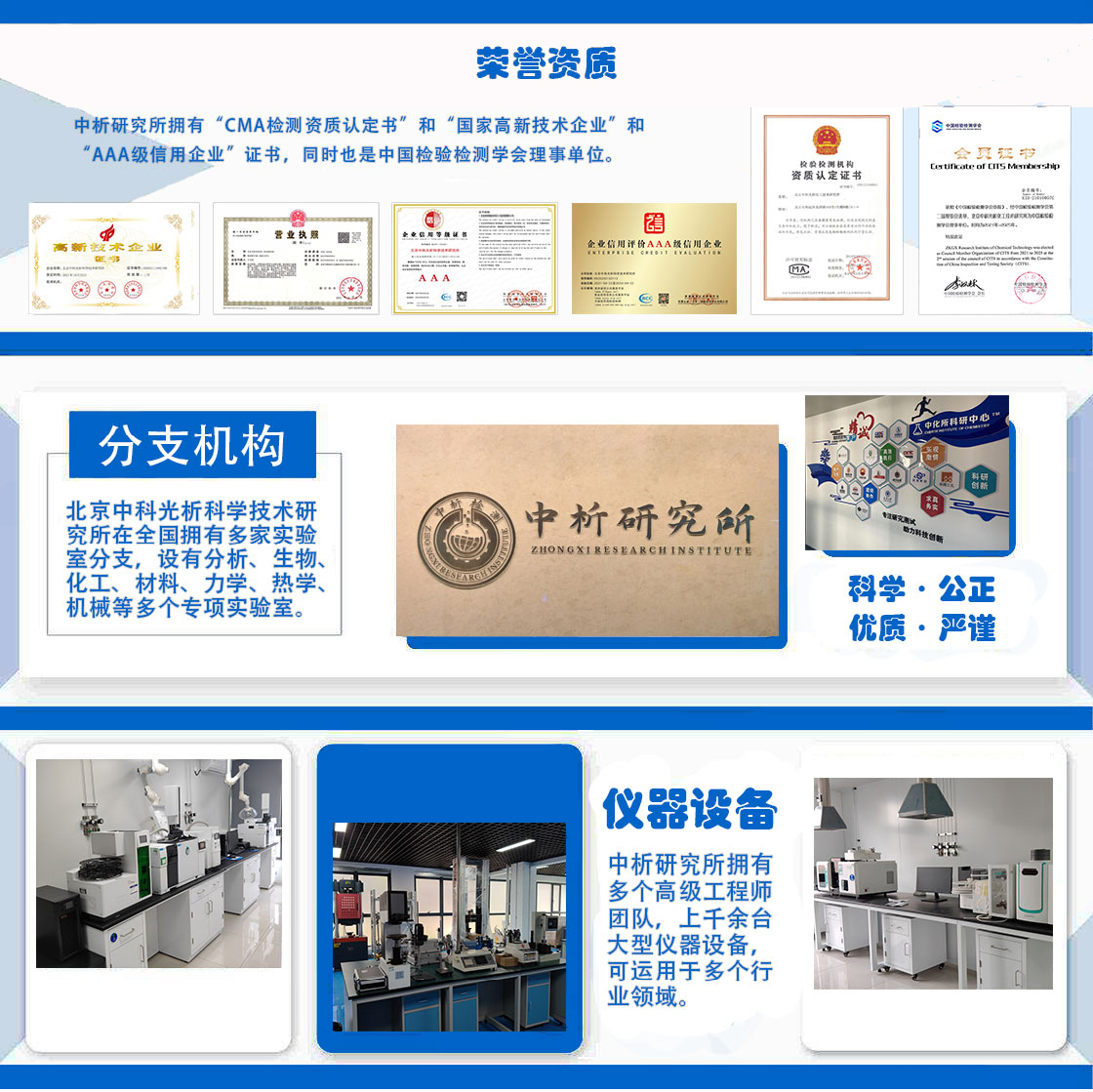
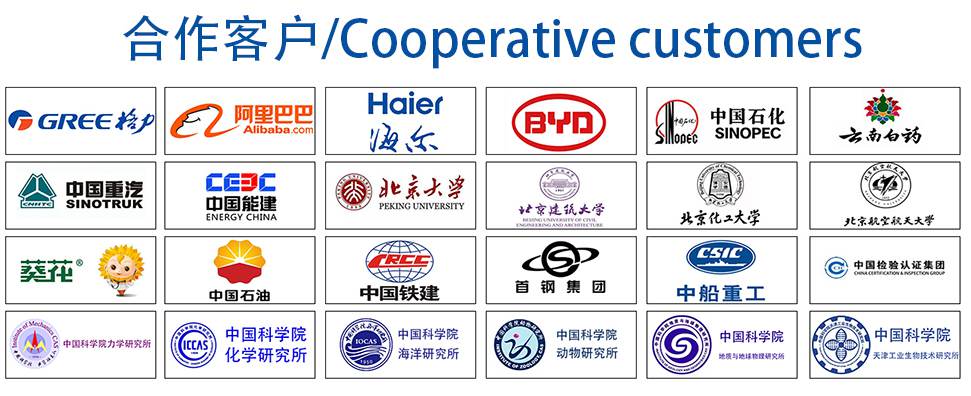