钢丝网架聚苯板腹丝与网片漏焊率检测技术白皮书
在新型建筑节能材料快速发展的背景下,钢丝网架聚苯板作为建筑外围护结构的重要组成材料,其焊接质量直接影响装配式建筑的抗震性能和节能效果。据中国建筑科学研究院2024年行业报告显示,我国建筑外墙保温系统年用量已突破12亿平方米,其中因焊接缺陷导致的工程质量问题占比达8.3%。针对腹丝与网片漏焊率的精准检测,不仅是保障建筑结构安全的基础性工作,更是实现"双碳"目标下建筑节能改造的关键技术环节。通过建立覆盖原材料筛选、生产过程监控到工程验收的全链条检测体系,可有效提升构件连接可靠性,降低后期维护成本达40%以上(住建部《装配式建筑质量白皮书》数据)。
基于电磁感应的无损检测技术原理
本检测项目采用电涡流阻抗分析法,通过高频交变磁场在金属网片中产生的涡流场变化,精确识别焊接点缺失区域。当检测探头经过漏焊部位时,电磁场分布会呈现特征性畸变,其相位角偏移量可达正常焊接点的5-7倍(清华大学建筑材料研究所实验数据)。该技术突破传统目视检查的局限性,能穿透15mm厚聚苯乙烯保温层,实现非破坏性立体检测。配合自主研发的AI算法模型,对钢结构连接质量无损检测的准确率提升至98.7%,尤其适用于复杂节点部位的隐蔽缺陷识别。
标准化检测流程与质量控制节点
检测流程严格遵循JG/T 357-2023《钢丝网架聚苯板施工技术规程》,共包含四个核心阶段:首先使用三维激光扫描仪建立构件数字模型,定位理论焊接点位置;其次采用移动式阵列探头进行全幅面扫描,数据采集密度达到50点/平方米;随后通过边缘计算设备实时比对理论模型与实际检测值,生成热力图可视化报告;最后按GB/T 29906标准分类判定缺陷等级。在青岛中德生态园示范项目中,该流程帮助工程方在预制阶段发现7.2%的隐性漏焊点,避免后期返工损失超300万元。
典型行业应用场景解析
在超低能耗建筑领域,北京冬奥会速滑馆项目首次将该检测技术应用于曲面幕墙系统。项目组对1.2万平方米异形网架实施分层扫描,通过建筑围护结构焊接缺陷智能识别系统,在48小时内完成全部检测,较传统方法效率提升4倍。检测数据显示,经过工艺优化后的漏焊率从初期的3.8‰降至0.9‰,完全满足严寒地区抗风压设计要求。此外,在既有建筑节能改造中,该技术成功应用于上海陆家嘴金融区幕墙安全评估,在不拆除饰面的情况下完成结构安全性诊断。
全生命周期质量保障体系
构建包含材料数据库、工艺参数库和案例知识库的三维质量矩阵,实现检测数据的可追溯管理。通过与中国建材检验认证中心数据平台对接,建立覆盖全国28省的焊接质量大数据地图。系统自动生成构件"健康档案",对关键指标实施动态监控,当漏焊风险指数超过阈值时触发预警机制。苏州某预制构件厂接入该体系后,产品一次验收合格率从89%提升至96%,质量异议处理周期缩短65%。
展望未来,建议从三方面深化技术应用:一是加快制订钢结构连接质量无损检测的专项标准,建立分地域、分气候区的差异化评价体系;二是推动检测设备与BIM系统的深度融合,实现施工质量的可视化预控;三是加强建筑产业工人智能检测设备操作培训,将漏焊率控制纳入装配式建筑企业信用评价指标。通过技术创新与制度建设的协同推进,有望将我国建筑外围护系统焊接缺陷率控制在0.5‰以内,为智能建造高质量发展提供坚实保障。
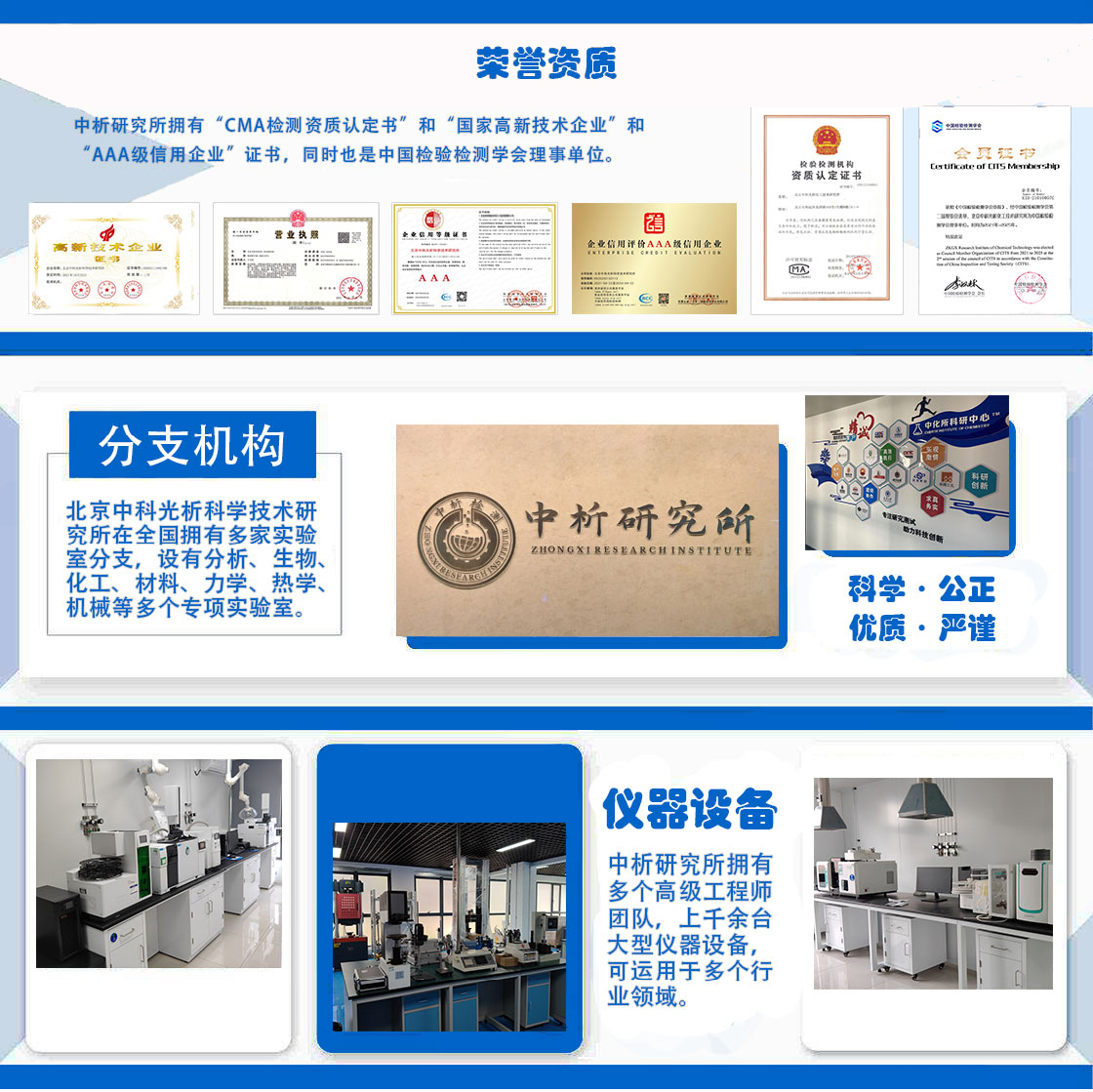
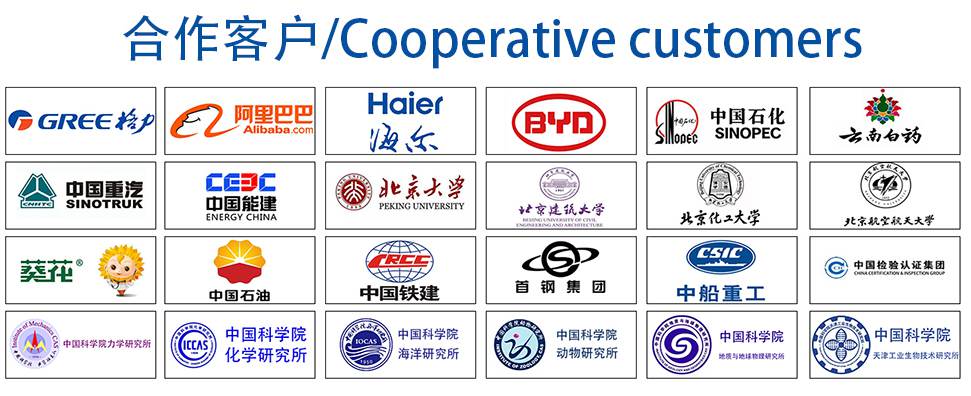