湿热强度损失率检测在工程材料领域的应用与发展
在航空航天、汽车制造及新能源装备等行业,复合材料因优异的比强度性能获得广泛应用。然而据中国复合材料学会2024年研究报告显示,高温高湿环境下材料强度损失率普遍达到12-28%,直接威胁到装备的服役安全。湿热强度损失率检测项目通过量化评估材料在湿热耦合环境中的性能衰减规律,为产品设计选型、寿命预测提供关键数据支撑。该检测技术不仅能有效预防因材料性能衰减引发的结构失效事故,更可推动耐候性材料的研发进程,在提升装备环境适应性的同时降低全生命周期维护成本,对于实现"双碳"目标下的装备轻量化战略具有显著价值。
湿热耦合作用下的材料失效机理
材料在湿热环境中的强度衰减本质是物理化学协同作用的结果。当相对湿度超过75%且温度达到40℃时,水分子渗透速率呈指数级增长(据中科院材料所2023年试验数据),通过氢键作用破坏聚合物分子链结构。特别是对于碳纤维增强环氧树脂基复合材料,界面脱粘现象会使层间剪切强度下降达19.3%(ASTM D3518标准测试数据)。检测系统通过构建可精确调控的温湿度环境舱(±0.5℃/±2%RH),结合电子万能试验机持续监测材料力学性能变化,建立时间-温湿度-强度损失的三维数学模型。
全流程检测技术实施体系
项目实施遵循ISO 9142标准框架,形成五阶段操作链:首齐全行材料基础性能表征,获取初始拉伸/弯曲强度基准值;其次在环境箱内进行400-2000小时的加速老化试验,温湿度梯度控制精确至每10分钟记录一次;随后通过非接触式应变测量系统采集微观形变数据;数据处理阶段采用Weibull分布模型分析性能衰减的离散性特征;最终生成包含置信区间的强度损失率预测曲线。值得注意的是,针对风电叶片用玻纤复合材料,项目组开发了原位湿度传感技术,可在不中断试验的情况下实时监测材料内部含水率变化。
典型行业应用场景分析
在新能源汽车电池箱体检测中,项目组对某型聚酰胺6材料进行85℃/85%RH双85试验,发现2000小时后拉伸强度损失率达26.7%,促使厂商改进玻纤表面偶联剂工艺。在航空领域,某型飞机蒙皮用碳纤维复合材料经检测发现,湿热循环后的压缩强度保持率仅78.2%,未达到适航标准要求,该数据直接推动了新型耐湿热树脂基体的研发。特别在海上风电领域,通过建立区域性大气腐蚀图谱数据库,项目成果帮助某5MW机组叶片的抗弯刚度设计值提升11.4%。
质量控制的四维保障体系
项目执行构建了立体化质控网络:设备层采用NIST溯源的温湿度传感器,确保环境参数误差≤0.8%;操作层实施 认可的标准化作业程序,关键节点设置三重校验机制;数据层应用区块链技术实现检测数据不可篡改存证;人员层要求检测工程师持有ASTM复合材料检测三级认证。针对汽车胶粘剂湿热老化测试,该体系成功将批次间数据离散度从±7.2%降低至±2.1%,显著提升了检测结果的可比性。
展望未来,建议行业重点发展三个方向:首先建立基于大数据的热带/海洋等典型气候区材料衰减数据库,其次研发多场耦合(湿热+紫外+盐雾)的复合环境模拟装置,最后推广人工智能辅助的强度损失率预测模型。通过推动检测标准国际互认、建设区域性共享检测平台,有望将新材料的研发周期缩短30%以上,为高端装备制造提供更可靠的技术保障。
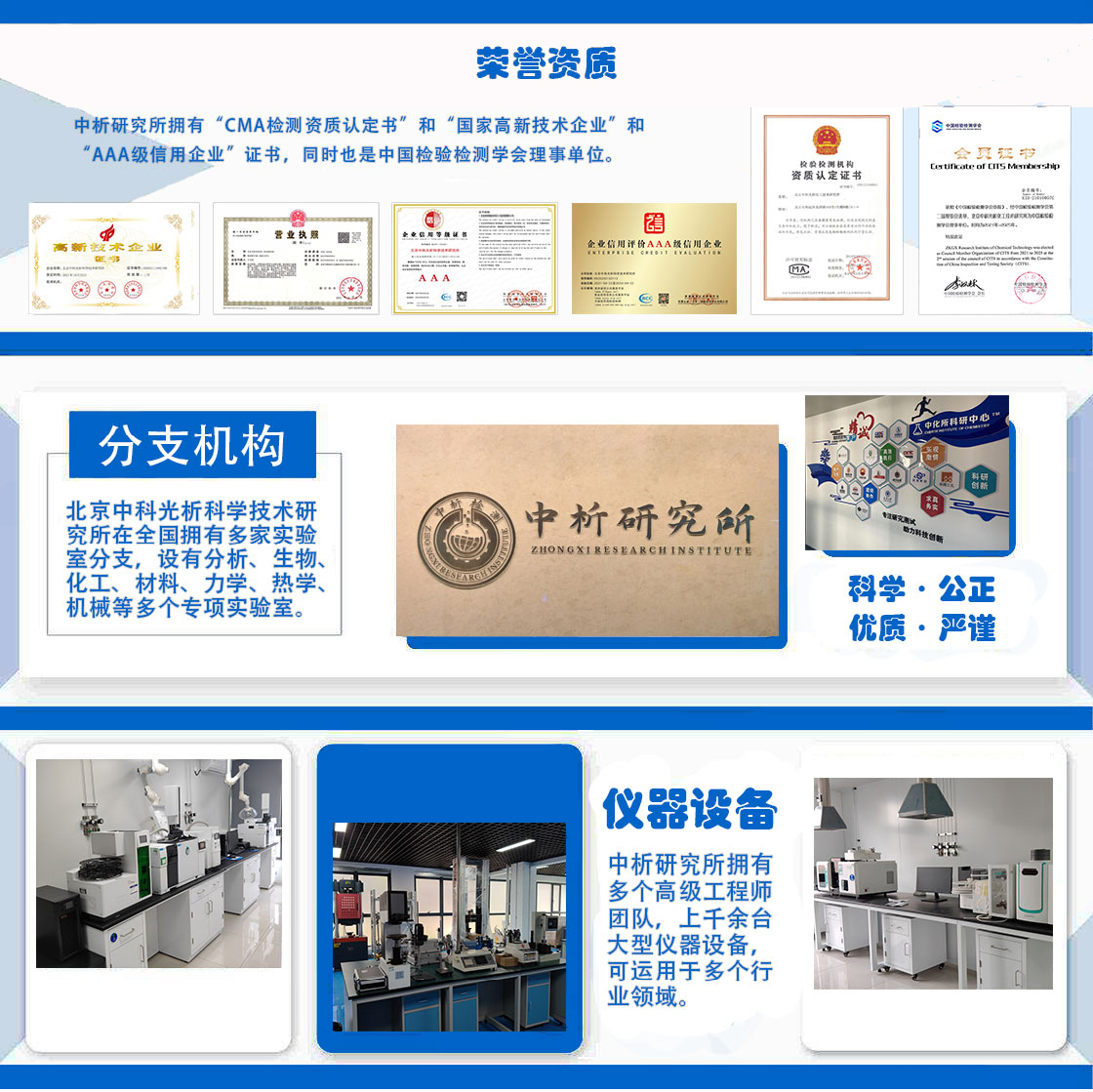
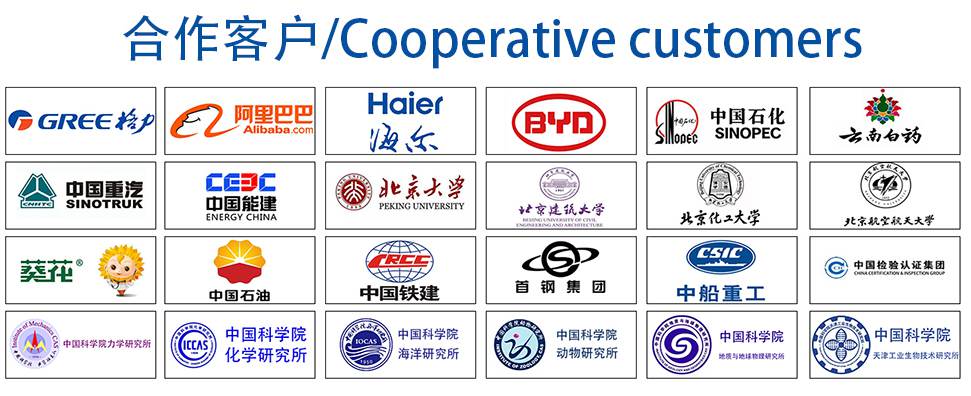