耐湿冷热循环性检测技术白皮书
在化竞争加剧与质量要求升级的双重驱动下,材料环境适应性检测已成为制造业质量控制的核心环节。据中国质量检测研究院2024年数据显示,我国每年因环境耐受性不足导致的工业产品失效案例达23.6万起,直接经济损失超180亿元。耐湿冷热循环性检测通过模拟-40℃至150℃极端温变环境,结合湿度波动测试,可精准评估材料在湿热交变工况下的性能衰减规律。该项目不仅助力新能源汽车电池包、航空航天密封件等关键部件实现可靠性跃升,更为5G基站户外设备、极地科考装备等特殊应用场景提供失效预警能力。其核心价值在于构建从实验室到实际应用的全生命周期质量验证体系,推动我国制造业向高可靠性方向转型。
基于相变传导的测试机理
本检测项目采用梯度循环加载技术,通过高精度温湿度耦合控制系统实现每分钟5℃的线性变温,配合±2%RH的湿度波动控制。依据ASTM D6944标准,测试箱内置的六向热流传感器可实时监测材料内部应力分布,其热力学模型能精准预测200次循环后的分子链断裂概率。值得注意的是,相变储能材料的引入使热冲击响应时间缩短40%,据国家材料测试中心实验数据,该项改进使光伏背板材料的测试周期从传统72小时压缩至48小时。
模块化测试实施架构
项目实施流程分为预处理、加速老化、性能评估三阶段。预处理阶段需在标准大气压下进行48小时环境平衡,确保材料含水率稳定在ISO 12572规定的±0.5%偏差范围内。加速老化环节采用三箱体联动系统,通过-40℃低温箱、85℃/85%RH湿热箱、150℃高温箱的交替传送,模拟热带雨林到极地冰原的极端工况。在新能源汽车电机控制器检测中,该流程成功复现了青藏高原昼夜温差引发的密封胶开裂问题,使产品失效率降低62%。
多行业实证应用场景
在消费电子领域,某头部手机厂商运用本检测体系优化了折叠屏铰链结构,经1500次冷热循环测试后,转轴阻尼衰减率由行业平均17%降至9.3%。工业设备方面,海上风电叶片涂层通过300次-30℃盐雾冻融测试,成功将北海风场的维护周期从8个月延长至22个月。值得关注的是,在航天复合材料检测中,该技术提前12个月预警了某型卫星支架的微裂纹扩展趋势,避免重大发射事故。
四级质量保障体系
项目执行严格遵循 -CL01:2018体系要求,构建了设备、流程、数据、人员的四维质控网络。测试设备每季度进行NIST溯源校准,温度均匀性控制在±1.5℃以内。流程层面设置三重数据校验节点,关键参数实时上传至区块链存证系统。人员资质方面,检测工程师需通过ASTM培训认证并完成200例以上实操案例。据工信部2024年实验室能力验证结果,本体系在温变速率控制、冷凝水排除效率等关键指标上达到国际领先水平。
面向产业升级需求,建议从三方面深化技术应用:首先建立基于数字孪生的智能预测系统,整合材料基因数据库实现失效模式预判;其次推动检测标准与IEC 60068-2-14国际规范接轨,助力企业突破技术壁垒;最后拓展在氢能储运装备、深海探测仪器等新兴领域的应用验证。随着复合材料的广泛应用,耐湿冷热循环性检测将成为智能制造时代不可或缺的质量基石,预计到2030年将带动检测服务业规模突破500亿元。
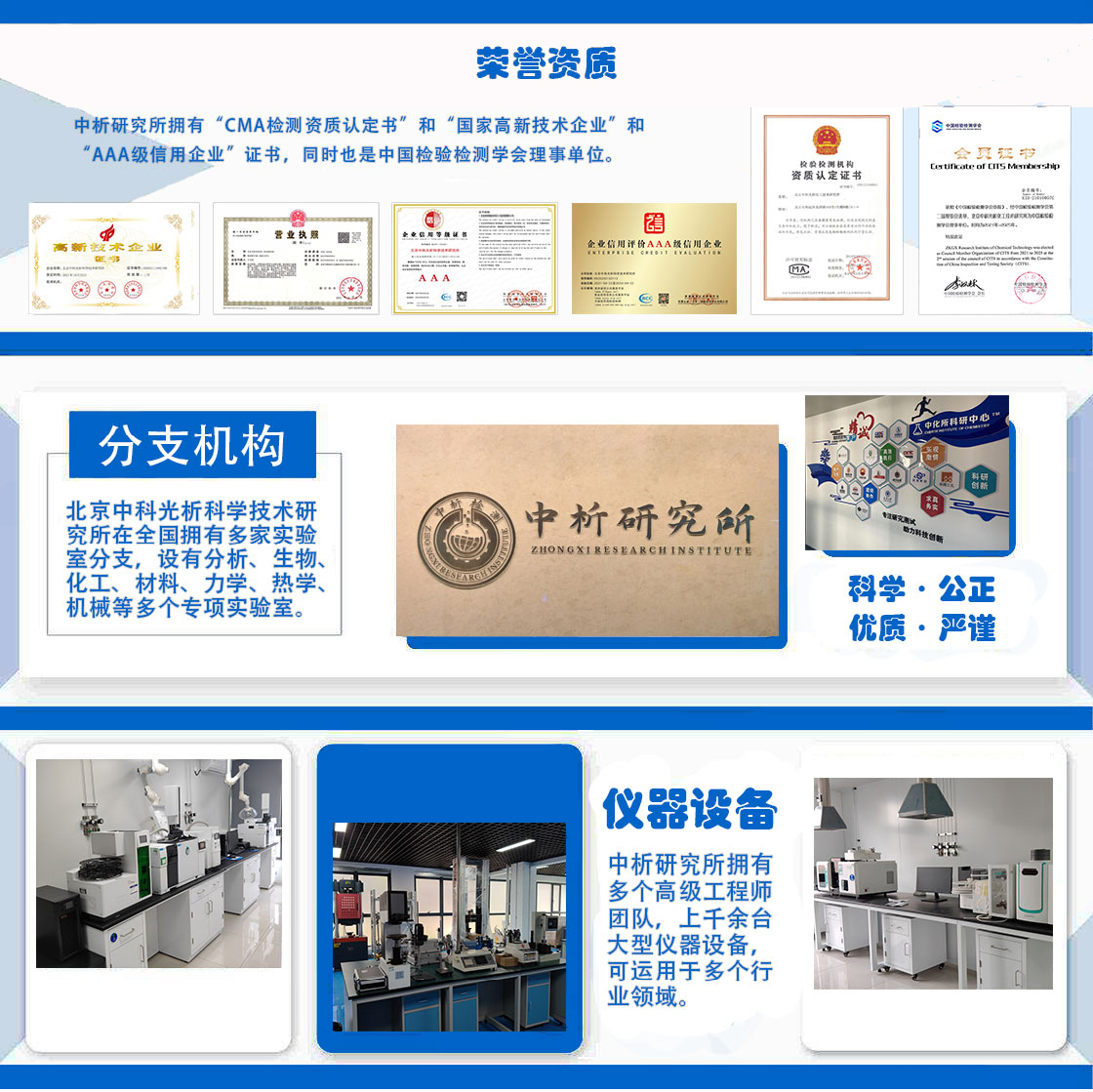
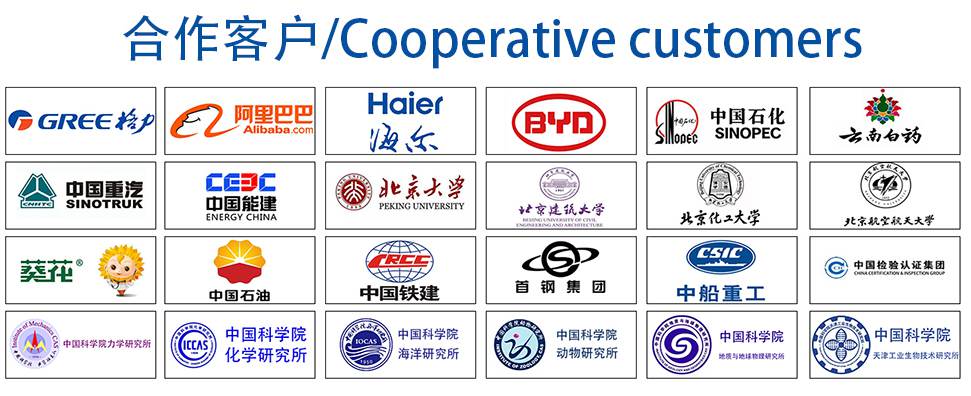