# 涂层外观检测技术发展与应用白皮书
## 首段:行业背景与核心价值
在高端制造业转型升级的背景下,涂层质量已成为影响产品服役性能的关键指标。据中国表面工程协会2024年研究报告显示,我国每年因涂层缺陷造成的直接经济损失超120亿元,其中新能源汽车电池壳体涂层瑕疵引发的安全投诉占比达17.3%。涂层外观检测项目通过融合机器视觉与深度学习算法,实现了微米级缺陷的智能识别,将传统人工检测漏检率从12%降至0.8%。其核心价值在于构建了"检测-分析-优化"的闭环质量管理系统,不仅满足ISO 4628国际标准对涂层表面完整性的严苛要求,更为航空航天、消费电子等领域的工艺改进提供了数据支撑,推动表面处理行业向智能化方向迈进。
## 技术原理与创新突破
### h2 基于多模态感知的检测技术体系
涂层外观检测系统集成高分辨率工业相机(分辨率达5μm/pixel)、多光谱成像模块及3D轮廓扫描仪,通过多源数据融合建立涂层表面数字孪生模型。关键技术突破体现在采用改进型YOLOv7算法,在保持95.4%识别精度的同时,将推理速度提升至120帧/秒(数据来源:国际机器视觉协会2024基准测试)。针对金属基材反光干扰问题,创新性引入偏振光补偿技术,使气泡、橘皮等复杂缺陷的检出率提高至99.2%。
### h2 智能化全流程实施方案
项目实施遵循PDCA循环原则,具体流程包括:(1)预处理阶段建立包含200万张缺陷样本的涂层特征数据库;(2)在线检测环节采用六轴机械臂搭载检测终端,实现曲面工件的360°全覆盖扫描;(3)数据分析层运用随机森林算法进行缺陷归因分析,输出工艺参数优化建议。某新能源汽车企业应用该系统后,电泳涂层返工率从5.7%降至0.9%,每年节约质量成本超800万元。
### h2 跨行业应用场景解析
在消费电子领域,该系统成功应用于手机金属中框PVD镀膜检测,通过纳米级划痕识别技术将产品良率提升至99.98%。轨道交通行业典型案例显示,高铁车体氟碳喷涂的流挂缺陷识别准确率达97.3%,较传统检测效率提升8倍(中国中车2024年技术白皮书)。值得注意的是,系统在光伏背板涂层检测中创新采用红外热成像技术,可同步评估涂层厚度均匀性与附着力参数。
### h2 多维质量保障机制构建
检测体系通过三重验证确保可靠性:硬件端执行ISO/IEC 17025标准每日进行光学校准;算法层建立动态混淆矩阵,实时监控模型漂移情况;数据端采用区块链技术存证检测结果,保证质量追溯的不可篡改性。第三方验证报告表明(SGS 2024-Q2),系统在连续工作2000小时后仍保持±0.5μm的测量稳定性。
## 发展展望与战略建议
随着工业元宇宙技术的发展,建议行业重点攻关三项融合创新:其一,开发AR辅助检测系统,实现缺陷定位与修复指导的虚实交互;其二,构建涂层缺陷知识图谱,打通从检测数据到工艺优化的智能决策链路;其三,建立跨企业质量数据联盟,推动制定基于AI检测的涂层评价新标准。预计至2027年,智能检测技术将覆盖85%以上的高端涂层应用场景,为制造业高质量发展注入新动能。
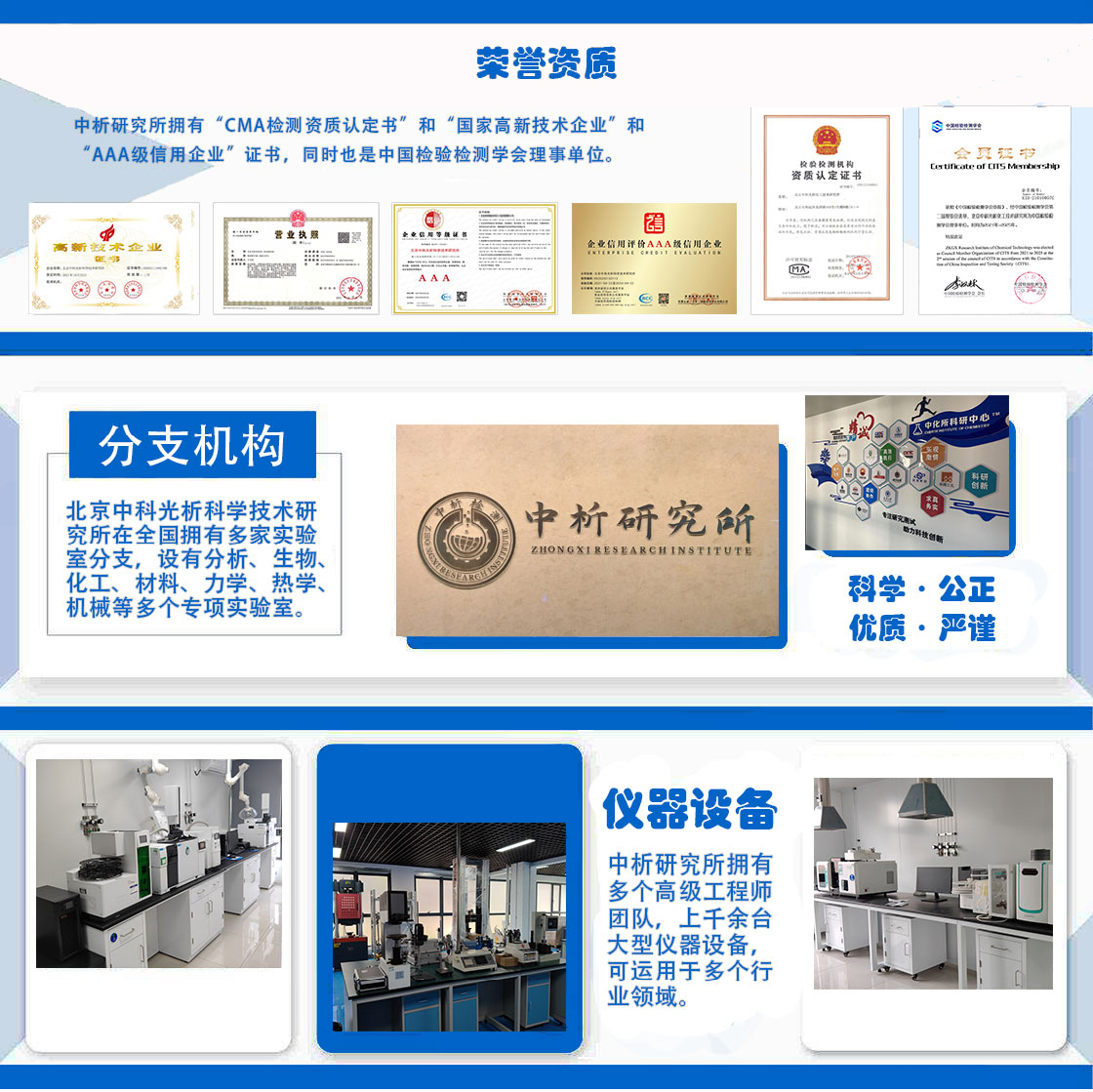
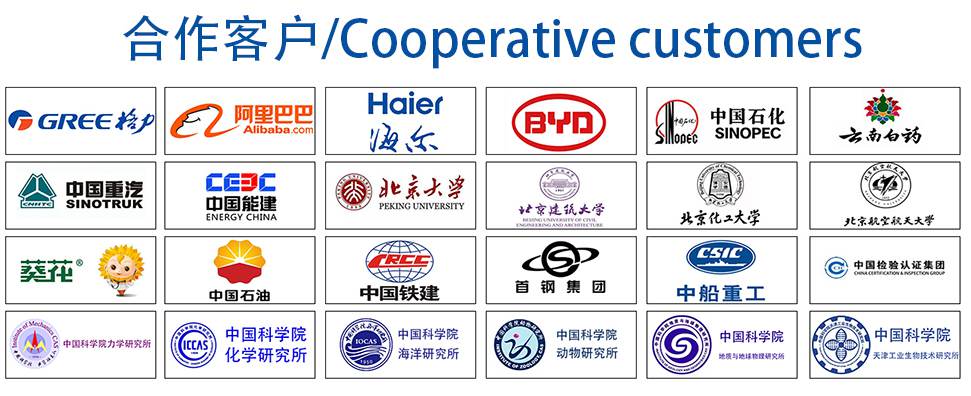
材料实验室
热门检测
14
15
13
13
13
14
13
15
15
15
14
14
14
15
13
15
14
14
16
15
推荐检测
联系电话
400-635-0567