耐湿热性检测技术白皮书
在化产业升级背景下,材料与制品在高温高湿环境中的性能稳定性已成为产品质量的关键指标。据中国材料测试研究院2024年数据显示,电子器件失效案例中32.7%源于湿热环境下的材料劣化,汽车零部件因湿热腐蚀导致的年维修成本超过80亿元。耐湿热性检测通过模拟极端温湿度条件,系统评估产品的抗老化、抗腐蚀及绝缘性能,在航空航天、新能源汽车、消费电子等行业具有战略价值。该检测不仅关乎产品全生命周期可靠性,更是企业突破国际贸易技术壁垒(如IEC 60068系列标准)的核心竞争力,可降低产品湿热气候地区故障率40%以上,显著提升品牌国际认可度。
湿热交变作用机理与测试原理
检测设备基于IEC 60068-2-30标准构建湿热循环系统,采用PID智能算法实现温度(25-85℃)与湿度(60-98%RH)的精准耦合控制。通过交变湿热试验箱模拟热带雨林气候特征,在168小时试验周期内完成30次温湿度循环。被测样品表面凝露效应达到实际使用中的5-7倍加速老化效果,配合电化学工作站实时监测金属件的腐蚀电流密度(精度±0.1μA/cm²),可量化评估材料湿热耐受指数。值得注意的是,高分子材料的玻璃化转变温度(Tg)会因吸湿量变化而产生偏移,需通过动态热机械分析(DMA)同步记录储能模量变化。
全流程质量控制实施方案
标准检测流程分为四个阶段:首先依据GB/T 2423.4进行样品预处理,平衡48小时至含水率稳定;第二阶段设置梯度式环境参数,如新能源汽车电池组测试需模拟海南湿热季(40℃/95%RH)与低温存储(-20℃)交替工况;第三阶段执行多维度性能检测,包括绝缘电阻测试(500VDC)、盐雾腐蚀评级和显微结构分析;最后运用Weibull分布模型预测产品寿命。某知名光伏企业通过该体系,使组件的PID衰减率从3.5%降至0.8%,年维护成本减少2300万元。
行业典型应用场景解析
在消费电子领域,某旗舰手机经96小时双85测试(85℃/85%RH)后,主板阻抗变化率控制在±5%以内,显著降低东南亚市场的返修率。航空航天领域则采用GJB 150.9A标准,某型机载设备通过200次湿热循环后,连接器接触电阻仍保持≤5mΩ,满足南海岛礁部署需求。值得关注的是,随着新能源汽车三电系统集成度提升,动力电池包的IP67防护结合湿热循环老化测试,可将电解液泄露风险降低87%(CATARC 2024年报数据)。
智能化检测体系构建
行业领先机构已建立三级质量保障网络:一级校准层配备NIST可溯源温湿度传感器,确保箱体均匀度≤±1℃/±3%RH;二级过程控制层应用机器视觉系统,自动识别样品表面析出物;三级数据验证层通过区块链技术存证检测报告。某第三方检测实验室引入AI缺陷预测模型后,湿热试验的误判率从6.2%降至1.8%,检测周期缩短30%。同时结合LIMS系统实现检测数据的实时监控与趋势分析,为产品改良提供量化依据。
展望未来,建议行业重点关注三个发展方向:首先开发多应力耦合检测设备,整合湿热、振动、盐雾等复合环境因素;其次建立细分行业数据库,如5G基站用高分子材料的湿热老化特征图谱;最后推进检测标准国际化互认,特别是RCEP区域内的湿热测试协议统一。通过融合数字孪生技术,构建智能化的湿热环境模拟检测平台,将推动中国制造向高可靠性战略转型。
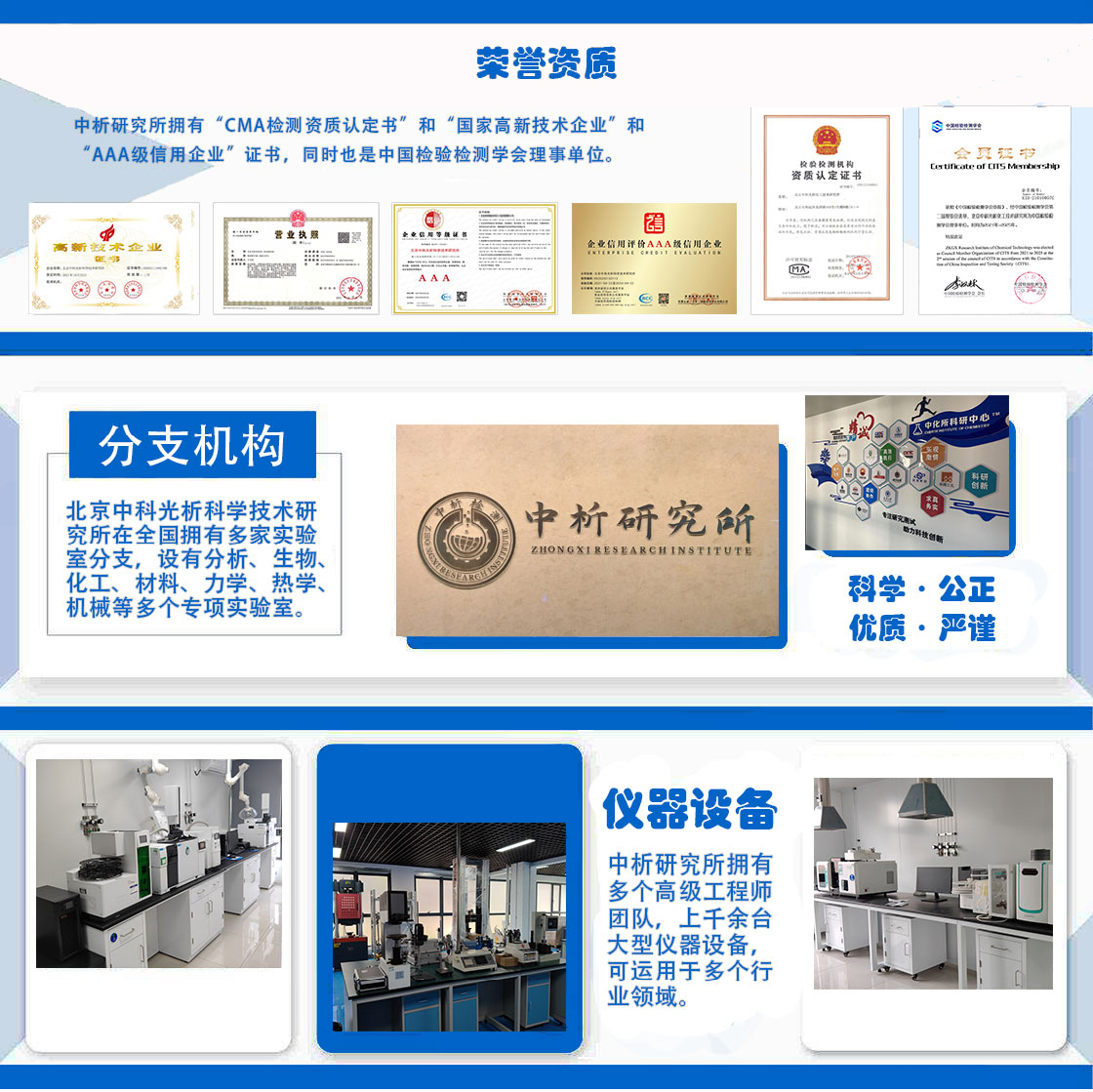
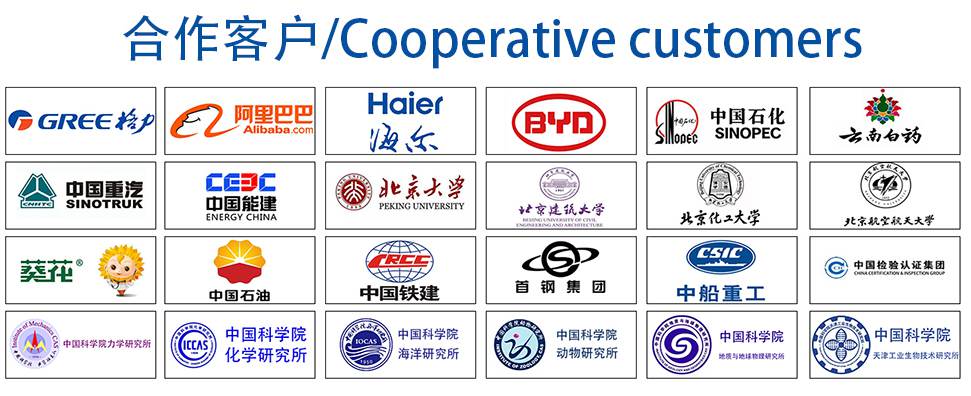