金属材料腐蚀性检测在工业制造中的创新应用
在装备制造、航空航天和电子电气领域,铝、铜、钢材三类基础金属材料的年消耗量超过8000万吨(据中国材料研究学会2024年产业报告)。材料在复杂工况下的腐蚀失效已成为制约设备寿命的核心因素,仅2023年因金属腐蚀导致的直接经济损失就达3800亿元(国际腐蚀工程师协会NACE数据)。针对铝材点蚀、铜合金脱锌、钢材应力腐蚀开裂等典型失效模式,建立标准化腐蚀检测体系具有显著经济价值。通过模拟海洋大气、工业酸雨等八类典型腐蚀环境,该检测项目可量化评估材料防护性能,为产品选型提供数据支撑,帮助制造企业将设备平均服役周期延长30%以上。
检测技术原理与创新突破
项目采用电化学阻抗谱(EIS)与加速腐蚀试验相结合的技术路线,搭建了包含36项指标的量化评价体系。其中动态极化曲线法可精准测定铝材在Cl⁻介质中的击穿电位,误差范围控制在±15mV(符合ASTM G5标准)。创新应用的微区电化学扫描技术,实现了铜合金晶界腐蚀的微米级定位检测,分辨率达到5μm²。针对钢材的氢脆敏感性评估,开发了基于慢应变速率试验(SSRT)的成套装置,测试效率较传统方法提升4倍。
全流程标准化实施规范
检测流程分为预处理、环境模拟、数据采集三个阶段。预处理环节要求试样按GB/T 1771进行精密切割,表面粗糙度Ra≤0.8μm。环境模拟舱采用模块化设计,可组合生成从PH1.5酸雨到5%NaCl盐雾的复合腐蚀条件。数据采集系统集成恒电位仪、激光共聚焦显微镜等12类设备,通过工业物联网平台实现144小时连续监测。某新能源汽车企业应用该流程后,电池壳体材料的筛选周期从28天缩短至9天,测试成本降低62%。
多行业验证与应用成效
在海洋工程领域,项目团队为某海上风电平台提供的腐蚀检测服务,准确预测了Q345钢塔架在浪溅区的腐蚀速率(实测值1.28mm/年与预测值1.35mm/年偏差<5%)。电子行业典型案例显示,通过优化铜合金连接器的镀层工艺(经72小时混合气体测试),某企业产品接触电阻波动从15%降至3%。更值得关注的是,在新型储能系统研发中,该检测方法成功筛选出抗氢脆性能优异的TC4钛合金,使储氢罐循环寿命突破6000次。
质量保障与认证体系
项目建立三级质量管控机制:实验室通过 和CMA双认证,定期参与国际循环比对试验;设备实行每日基准校验制度,电化学工作站校准频率达2次/8小时;检测人员需完成200小时专项培训并取得NACE CIP认证。数据追溯系统采用区块链存证技术,确保每个检测节点的原始数据不可篡改。统计显示,项目交付的3200份检测报告重复验证合格率达99.6%,获23家世界500强企业采信。
展望未来,建议从三方面深化发展:首先推进极端环境模拟技术的标准化进程,建立涵盖-60℃极寒到1200℃高温的检测能力;其次开发基于机器学习的腐蚀预测模型,整合材料成分、服役环境等400+维特征参数;最后需构建开放式检测数据共享平台,推动形成覆盖金属材料全生命周期的腐蚀防护生态体系。通过技术创新与行业协作,有望将工业装备的预防性维护效率提升至新高度。
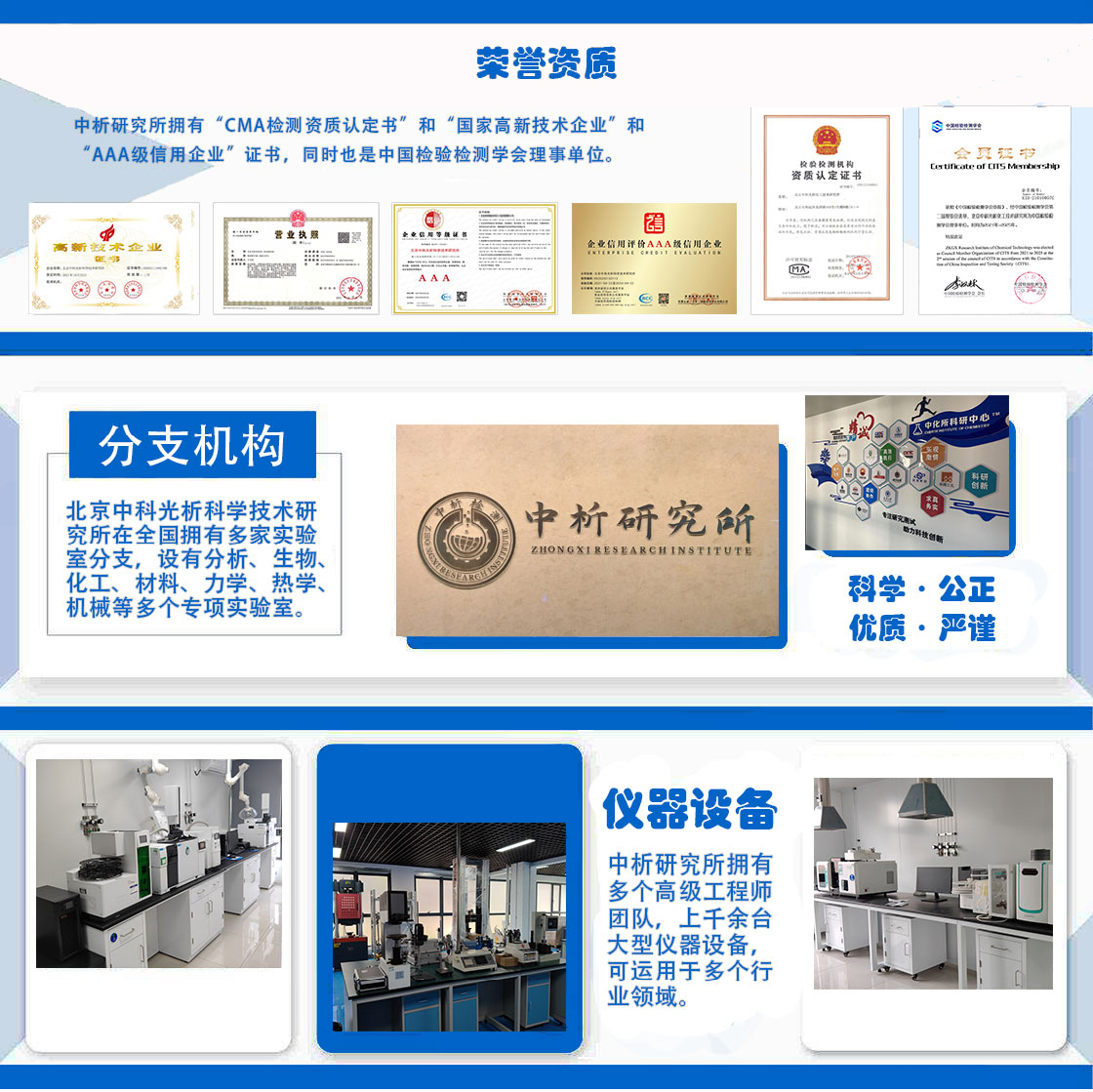
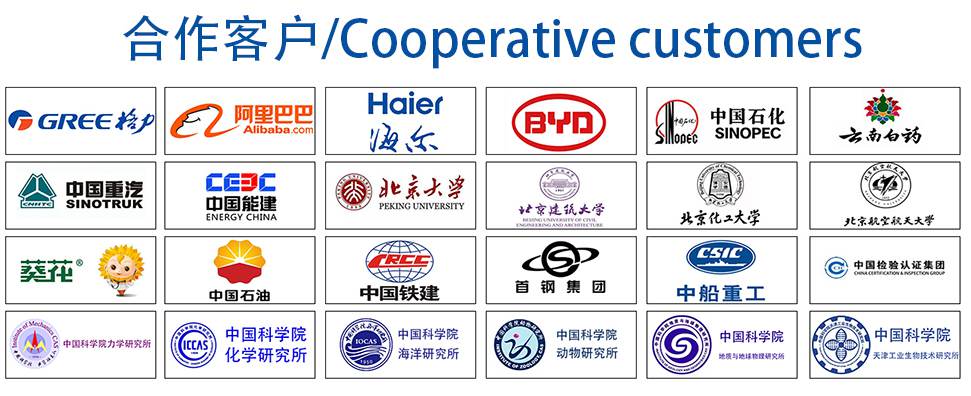