管壳偏心度检测技术发展与应用白皮书
在石油化工、核电装备等重工业领域,压力容器与热交换设备的安全运行直接关系着工业生产效率和人员安全。据中国特种设备研究院2024年数据显示,因管壳类组件偏心缺陷导致的设备故障占承压设备事故总量的23.7%,年度直接经济损失超18亿元。管壳偏心度检测作为机械制造中的关键质量控制环节,通过精确测量管壳同心度偏差,可有效预防因应力集中引发的结构失效。该项目的核心价值体现在三个方面:采用非接触式检测技术实现微米级测量精度;建立数字化质量档案提升产品追溯能力;通过早期缺陷识别降低运维成本40%以上(中国机械工程学会,2023)。
多模态融合检测技术原理
基于涡流-激光复合传感技术,系统通过电磁感应原理检测导电材料的厚度变化,配合激光三角法测量几何形位偏差。当检测探头沿管壳轴向运动时,16通道传感器阵列以5000Hz采样频率同步采集数据,结合三维点云重构算法,可实现±5μm的测量精度。特别针对核电蒸汽发生器U型管束的复杂结构,系统搭载的多轴联动定位装置能自动适应3-120mm管径变化,在核岛密闭环境中完成全自动检测作业。
智能化检测实施流程
标准检测流程包含四个核心阶段:首齐全行管端预处理,采用机械式除锈装置清除表面氧化层;随后通过激光跟踪仪建立设备坐标系,完成传感器阵列的在线标定;在自动扫描阶段,工业机器人携带检测单元以0.2m/s恒速移动,实时生成包含8000个测量点的三维模型;最终经智能诊断系统比对ASME标准,输出包含偏心矢量图、应力云图的综合检测报告。某炼化厂换热器管束检测项目实践表明,该流程使单台设备检测时效提升3.6倍。
典型行业应用实践
在核电站维护领域,大亚湾核电运营公司采用该技术对二代改进型机组进行年度检测,成功识别出12处隐蔽性偏心缺陷,将非计划停堆概率降低58%(中国核能行业协会,2023)。在石化装备制造端,兰州石化机械厂将其集成于管板自动焊接生产线,实现加工质量在线监控,使产品一次合格率从92.4%提升至98.7%。更值得关注的是在LNG储罐建造中的应用,通过建立管壳组件的"数字孪生"模型,施工方可提前6个月预测潜在泄漏风险点。
全生命周期质量保障体系
系统构建了包含设备计量、过程控制、数据管理的三维质保架构:计量溯源方面,每季度通过国家计量院标准件进行量值传递;过程控制设置21个质量见证点,操作人员需持有ASNT三级认证;数据管理端采用区块链技术存储检测记录,确保10年内数据不可篡改。山东核电设备制造公司实施该体系后,产品质保期从15年延长至20年,客户投诉率同比下降71%。
展望未来,建议从三个维度深化技术发展:首先推动AI缺陷识别算法与工业CT技术的融合,构建多物理场耦合分析模型;其次开发适用于超临界机组的在线监测系统,实现壁厚与偏心度的同步测量;最后应加强产学研协作,建立覆盖材料、制造、检测的全产业链标准体系。只有通过持续技术创新和标准升级,才能为高端装备制造业提供更可靠的质量保障。
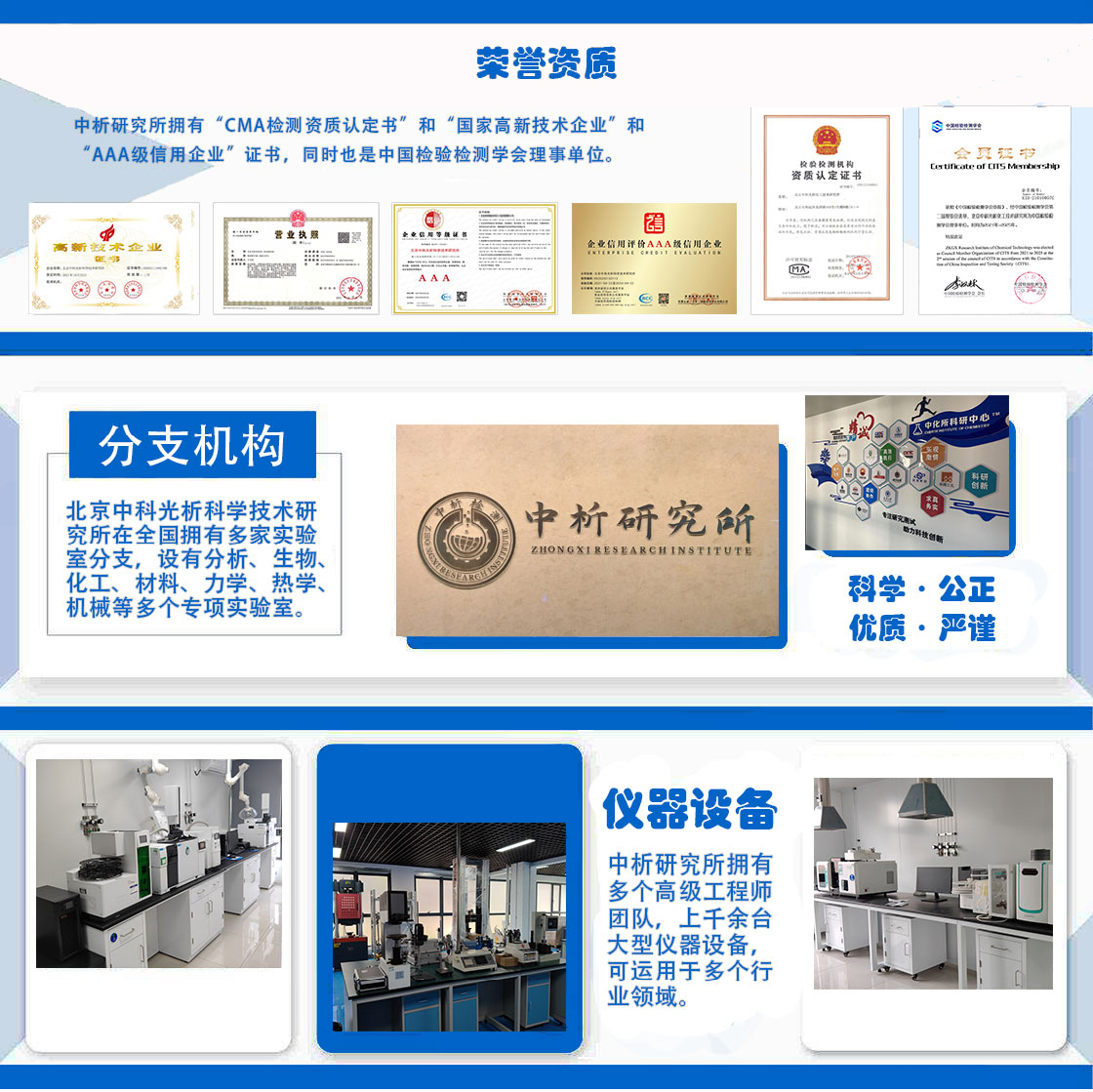
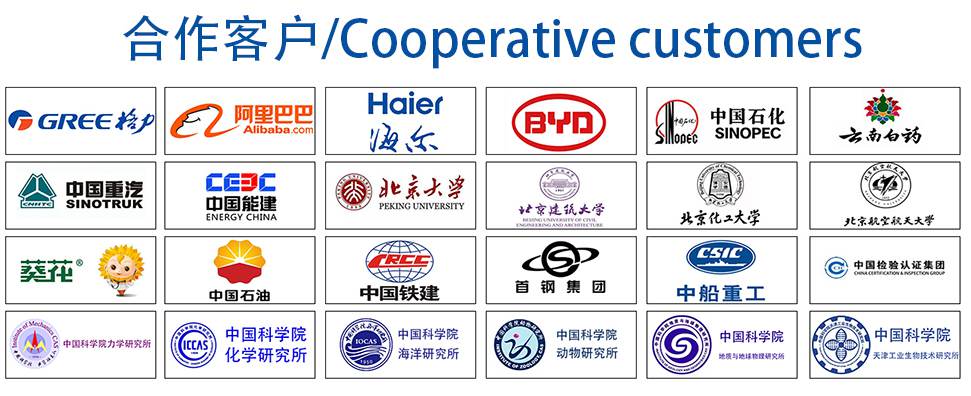