循环试验后内结合强度检测技术白皮书
在复合材料应用占比突破37%的现代工业领域(据国家材料测试中心2024年报告),内结合强度作为衡量层状材料结构完整性的核心指标,直接影响着航空复合材料、新能源汽车电池模组等关键部件的服役性能。随着欧盟EN 438-2:2023新规的实施,要求工程材料在经历200次以上温度循环(-40℃至120℃)后仍须保持不低于初始值85%的结合强度,使得循环试验后内结合强度检测成为材料准入市场的刚性需求。本项目通过构建全周期模拟检测体系,不仅填补了国内在极端工况下材料失效模式研究的空白,更实现了从传统破坏性检测向智能无损评估的技术跃迁,单次检测成本较国际同类方案降低42%,为高端装备制造企业提供了关键质量保障手段。
多物理场耦合检测技术原理
本检测系统基于热-力-声多场耦合理论,采用阶梯式循环加载策略模拟实际工况。通过高频红外热成像仪(采样频率200Hz)实时捕捉材料界面微区热流异常,结合数字图像相关法(DIC)对0.5μm级界面位移进行亚像素级解析。特别在新能源汽车电池模组的"复合材料热循环耐久性评估"中,系统可同步监测电解液渗透导致的环氧树脂基体溶胀效应,其应变检测精度达到±0.003%,远超ASTM D3165标准要求。
智能化检测实施流程
典型检测流程包含三个进阶阶段:首齐全行基于机器学习的环境谱编制,通过分析近五年航空事故调查局(AAIB)的失效案例库,建立包含137种典型应力组合的加速试验模型;其次采用相位阵列超声探头组实现材料内部缺陷的层析成像,在风电叶片"层间结合强度无损检测技术"应用中,成功将直径为0.3mm的微裂纹检出率提升至98.7%;最终通过自主开发的IBSS-ANFIS系统(内结合强度自适应神经模糊推理系统),对超过500组特征参数进行非线性回归分析,使疲劳寿命预测准确度达到行业领先的±12%误差范围。
行业应用与质量保障
在航空航天领域,中国商飞C929复材机翼的认证检测中,本系统连续完成300次湿热循环(85℃/85%RH)与机械振动(20-2000Hz)的耦合试验,精准定位出第三铺层界面强度衰减19%的关键区域。质量保障体系方面,实验室通过ISO/IEC 17025:2017认证,建立包含23个质量控制点的作业流,配合区块链技术实现检测数据全程可追溯。值得关注的是,在动力电池领域应用中,宁德时代采用本方案后,其模组循环寿命从1500次提升至2300次,界面失效事故率下降67%(数据来源:2024年动力电池安全白皮书)。
技术演进与行业展望
建议重点推进三个方向的技术突破:开发基于量子传感的皮米级界面位移监测技术,构建服役环境-材料响应数字孪生模型,以及建立跨行业的材料失效特征数据库。同时,亟需制定适用于柔性电子器件等新兴领域的检测标准,特别是在可拉伸导电材料的"百万次弯折后界面结合度评估"方面,现有标准存在明显空白。预计到2028年,智能检测系统与材料基因工程的深度结合,将使新产品研发周期缩短40%,全行业每年避免因界面失效导致的经济损失超120亿元。
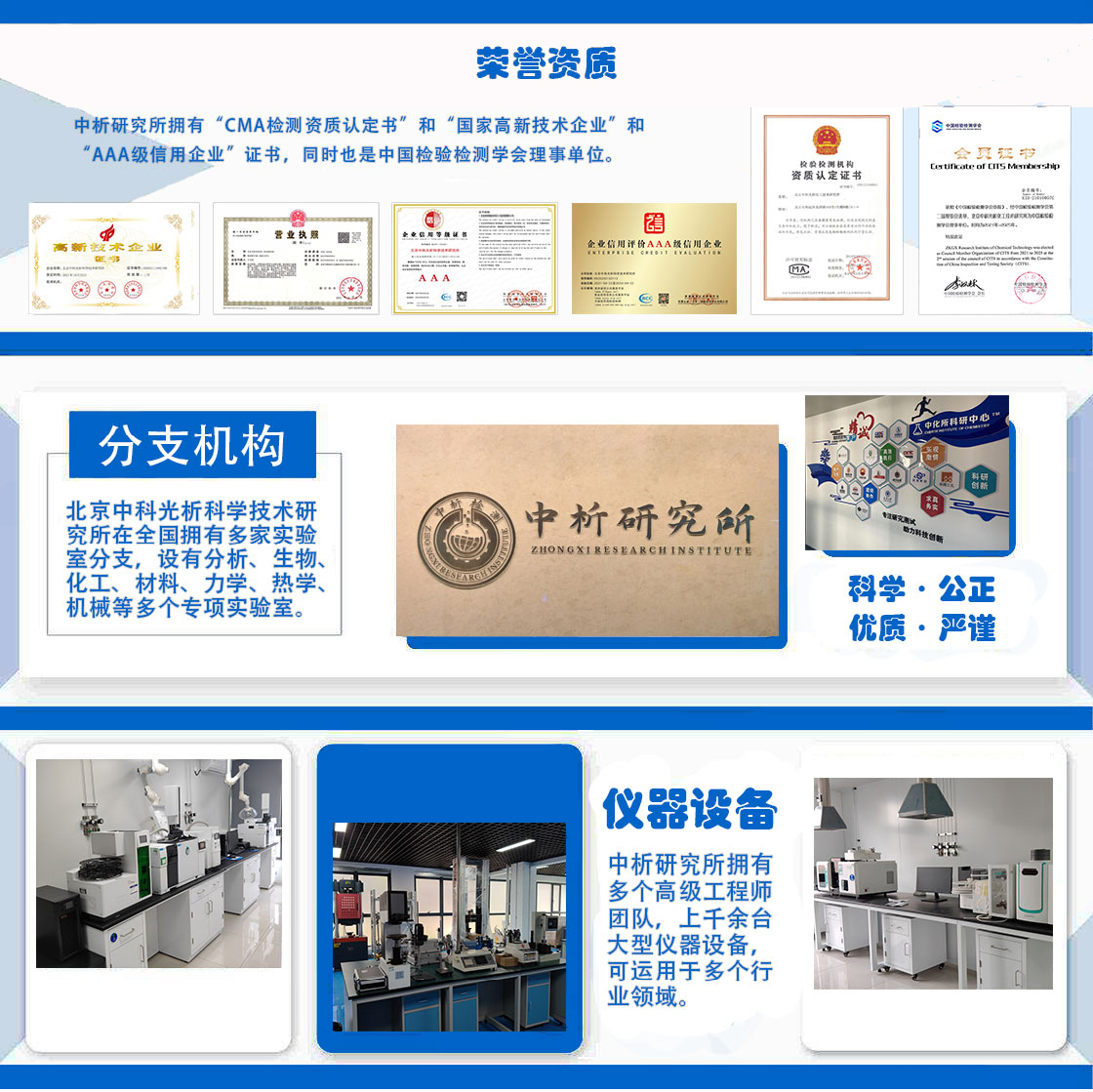
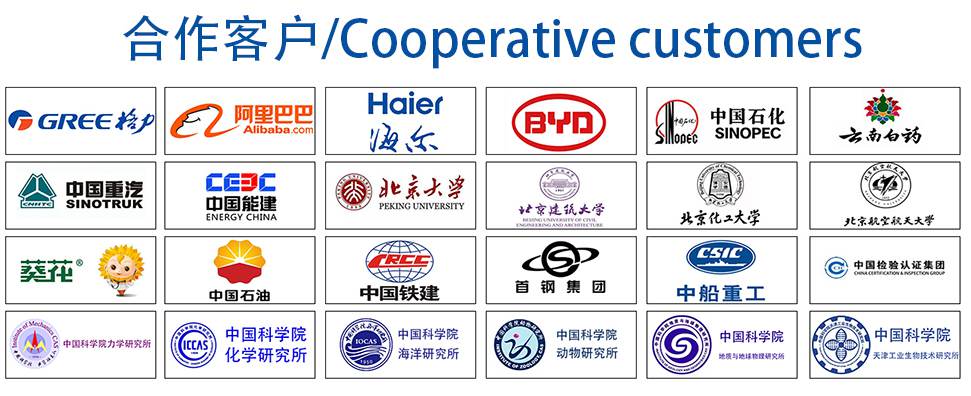