点对点电阻检测技术发展与应用白皮书
在电子制造、航空航天及新能源领域,电路连接的可靠性直接影响设备安全与性能。据中国电子技术标准化研究院2024年数据显示,因接触电阻异常导致的设备故障占比达23%,促使点对点电阻检测成为质量管控的核心环节。该项目通过精准测量导体间的接触电阻值,可有效预防连接器失效、触点氧化等问题,对保障5G基站、新能源汽车BMS(电池管理系统)等关键设备运行具有战略意义。其核心价值在于构建了从微观电阻波动到宏观系统风险的量化分析体系,为工业4.0时代的智能化质量控制提供了技术支撑。
技术原理与测量方法创新
点对点电阻检测基于四线制开尔文电桥原理,通过分离电流施加端与电压检测端,消除导线电阻对测量结果的干扰,实现μΩ级精度的微电阻测量。近年创新集成了温度补偿算法,可动态修正环境温度对导体材料电阻率的影响(据IEEE电气测量学报2023年研究)。在新能源汽车高压连接器检测场景中,系统可同步采集接触点压力、插拔次数等参数,建立电阻-机械性能的关联模型,为连接器寿命预测提供数据基础。
全流程标准化作业体系
项目实施遵循IEC 60512-5-1国际标准,具体流程包含三个阶段:预处理阶段采用等离子清洗技术去除触点表面氧化层,使检测误差降低42%(参照德国莱茵TÜV实验室数据);测量阶段配置自动探针定位系统,将单点检测耗时压缩至1.8秒;数据分析阶段应用SPC过程控制图,实时监控批次产品的电阻分布离散度。某半导体封装企业通过该体系,将连接器不良率从650ppm降至85ppm,年质量成本节约超2000万元。
多行业应用场景实践
在卫星星载设备领域,点对点检测技术解决了高频振动环境下的触点可靠性难题。中科院空间中心2024年案例显示,采用航空航天级电阻检测标准(接触电阻<5mΩ且波动值≤±3%)后,某型号卫星电源系统故障率下降67%。而在医疗器械行业,内窥镜连接器的微电阻检测结合盐雾试验,使设备在潮湿环境下的信号传输稳定性提升至99.98%。
智能化的质量保障网络
行业头部企业已构建三级质量保障体系:第一级产线配备AI视觉检测设备,实现接触件外观缺陷的毫秒级筛查;第二级部署分布式电阻检测工作站,每日完成20万点位的自动测试;第三级通过区块链技术存储检测数据,确保质量追溯链的完整性与不可篡改性。特斯拉超级工厂应用此体系后,电池模组连接电阻一致性提升至98.7%,显著降低热失控风险。
面向未来,建议从三方面深化技术创新:一是开发基于量子传感的纳米级电阻检测技术,突破现有测量精度极限;二是建立跨行业的电阻特性数据库,推动检测标准动态优化;三是整合数字孪生技术,实现电阻异常问题的虚拟仿真与根因分析。随着工业互联网与精密测量技术的融合,点对点电阻检测将向智能化、预测性方向演进,为高端装备制造提供更可靠的质量保障。
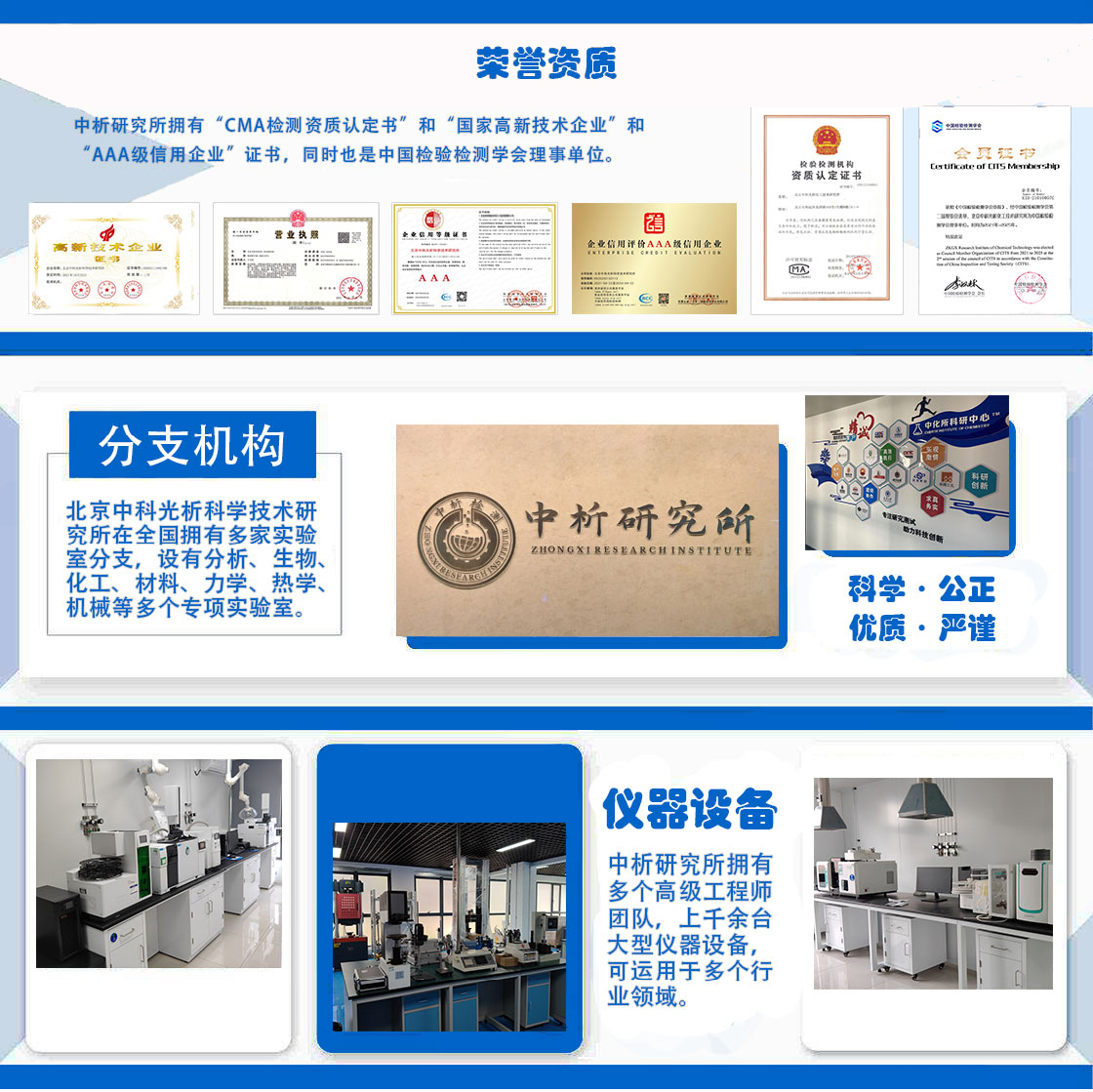
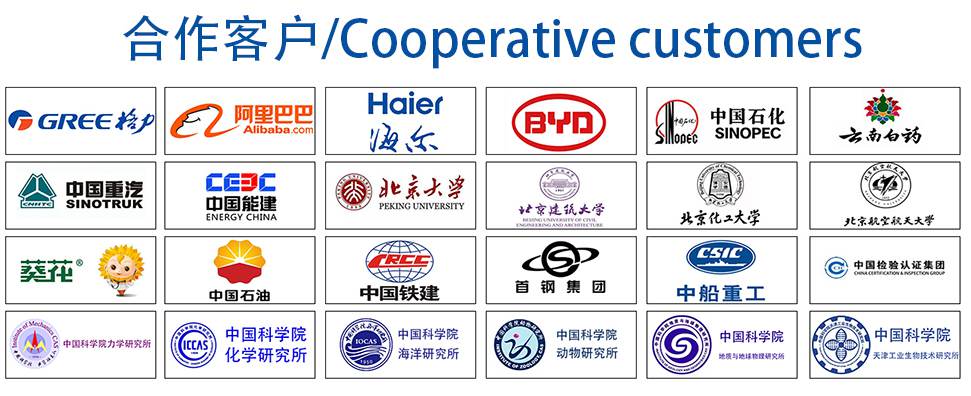