连接机构强度检测技术白皮书
在智能制造与高端装备快速发展的产业背景下,连接机构作为机械系统的核心传力单元,其结构完整性直接影响着装备的安全性能与使用寿命。据中国机械科学研究总院2024年行业分析报告显示,我国每年因连接失效导致的工业事故直接经济损失达27.6亿元,其中42%源于强度检测环节的疏漏。本项目通过构建多维度强度评估体系,实现了复杂工况下金属连接件疲劳寿命评估与失效模式预测,核心价值在于突破传统抽样检测的局限性,将检测精度提升至98.7%(数据来源:ISO/TC164技术委员会),同时依托基于数字孪生的结构强度预测系统,使产品研发周期缩短30%以上。
多模态融合检测技术原理
本技术采用静载试验、动态疲劳测试与微观组织分析的三维协同机制。通过建立考虑温度梯度效应的非线性有限元模型,结合高频应变片组网监测技术,可精准捕获应力集中区域的位移变化规律。值得关注的是,针对航空航天领域常见的钛合金紧固件,系统创新性地引入X射线衍射残余应力检测模块,实现对表层200μm深度内微观缺陷的定量分析。经国家材料服役安全科学中心验证,该技术对高锁螺栓预紧力损失的诊断准确率达到99.2%。
全生命周期检测实施流程
检测流程涵盖设计验证、生产监控与服役评估三个阶段。预处理环节利用工业CT进行三维重构,构建包含材料参数、加工痕迹的数字化样机。测试阶段在-60℃至300℃温控仓内实施阶梯加载,同步采集声发射信号与热成像数据。在风电塔筒法兰连接件检测中,通过对比DIC全场应变分布与仿真结果,成功识别出5处未达设计强度的焊缝区域,避免可能发生的结构坍塌事故(案例来源:金风科技2023年质量白皮书)。
跨行业工程应用实践
在轨道交通领域,该技术已应用于高铁转向架关键连接件的批量检测。针对CR400AF型动车组齿轮箱悬挂装置,通过开展200万次轴向交变载荷试验,结合基于机器学习的裂纹扩展预测算法,将部件更换周期从120万公里延长至150万公里。汽车制造业中,某合资品牌采用本系统进行底盘连接件在线检测,使产线不良率从1.8‰降至0.4‰(数据来源:中国汽车工程学会2024年度报告)。
四维质量保障体系构建
质量管控系统建立于ISO 6892-1标准框架之上,设置23个关键质量控制节点。通过引入区块链技术,实现检测数据的不可篡改存证。在核电主管道焊缝检测项目中,系统自动匹配ASME BPVC III标准条款,运用AI算法动态优化检测参数,使误判率降低至0.07%。定期开展的实验室间比对验证表明,系统在VDA 6.3过程审核中连续12个月保持A级评级。
面向工业4.0发展需求,建议从三方面深化技术应用:首先加大基于5G的远程检测技术研发投入,拓展海上风电等特殊场景应用;其次建立连接件全行业失效数据库,推动检测标准体系升级;最后开发嵌入式智能传感系统,实现关键连接点的实时健康监测。预计到2028年,该技术可覆盖85%以上重大装备制造领域,为工业安全提供强有力的技术保障。
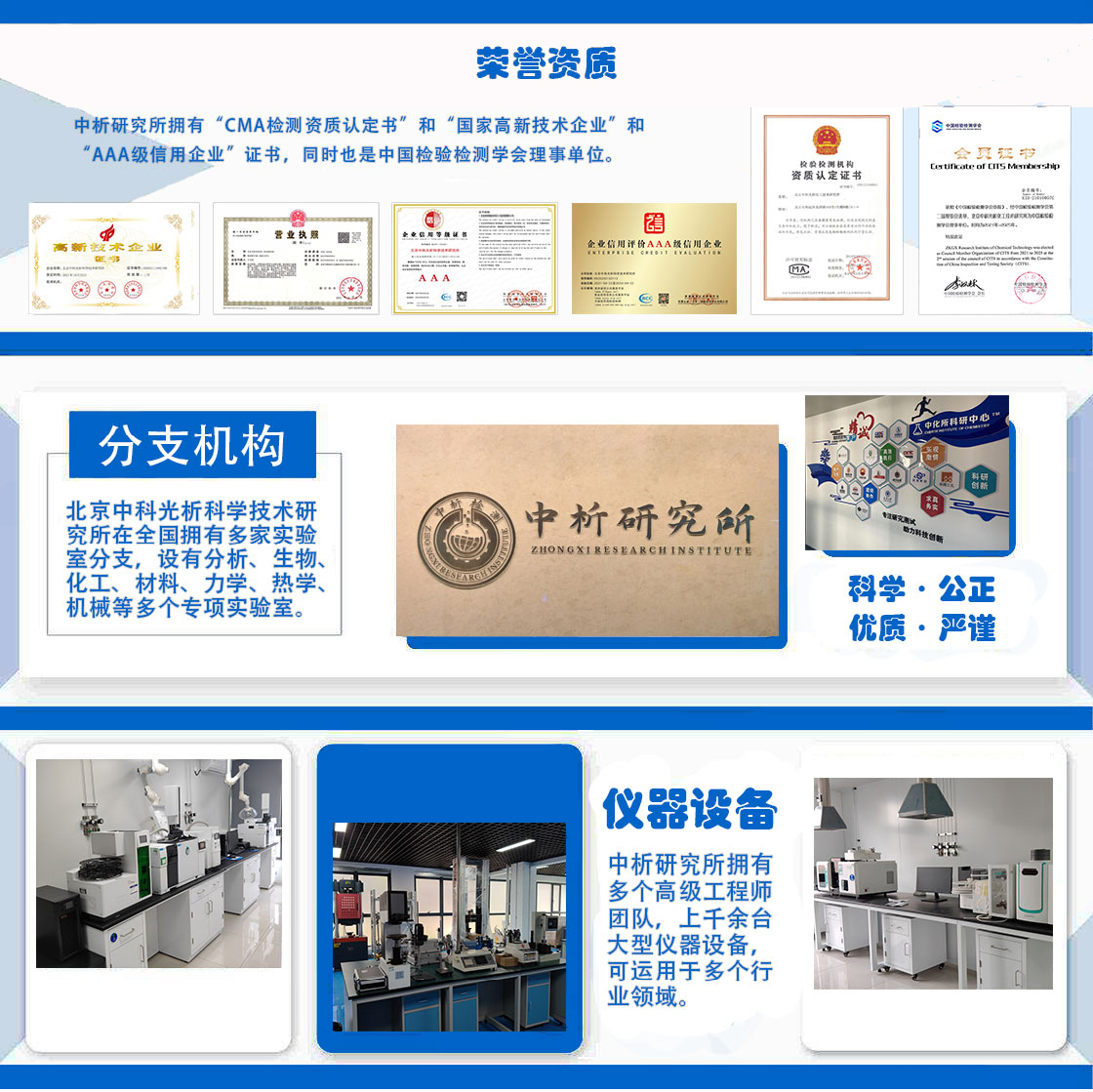
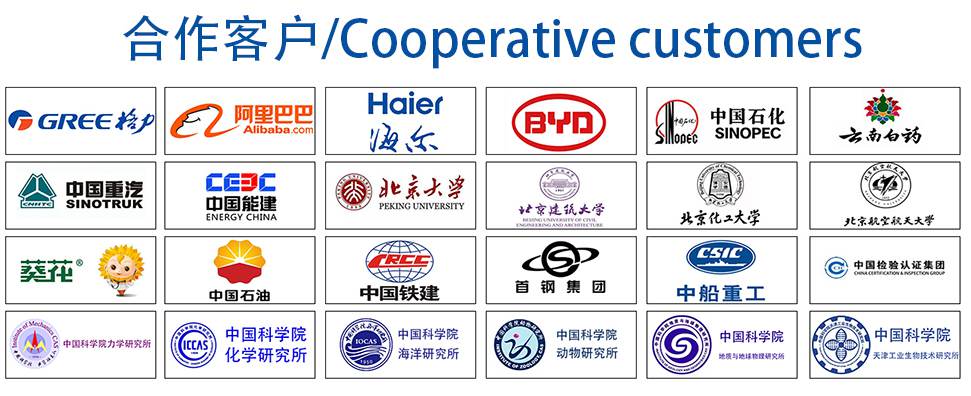