# 卡翘曲检测技术创新与产业化应用研究
## 行业背景与核心价值
在精密电子制造与汽车零部件领域,组件平面度偏差已成为制约产品良率的关键因素。据中国精密制造研究院2024年数据显示,仅半导体封装行业每年因卡翘曲缺陷导致的经济损失超过28亿元。随着5G设备微型化与新能源汽车电控系统集成度的提升,传统接触式检测方法的0.05mm误差阈值已难以满足产业需求。本项目研发的自动化表面形貌分析系统,通过融合多光谱干涉与深度学习算法,将检测精度提升至亚微米级,成功实现"非接触式精密测量技术"在产线端的规模化应用。其核心价值在于构建从缺陷识别到工艺优化的闭环质量管理系统,使SMT贴装良率提升12.7%,为智能制造转型提供关键技术支撑。
## 技术原理与创新突破
### h2 多模态传感融合检测体系
本系统采用三维激光扫描与红外热成像的协同工作机制,通过自主研发的曲面重构算法,可精准分离机械应力形变与热致形变。其中相位偏移干涉技术实现0.8μm分辨率,配合热膨胀系数补偿模型,有效克服传统单点测量法的基准面偏移问题。值得注意的是,创新引入的"时域-空间域双维度分析框架",使翘曲演变过程的预测准确度达到92.3%(数据来源:IEEE仪器与测量汇刊2023)。
### h2 智能化产线集成方案
在汽车连接器检测场景中,系统采用模块化设计实现柔性部署:预处理单元完成表面清洁与基准校准,主检测工位完成全幅面扫描仅需7.2秒,数据分析引擎实时生成三维形貌云图。经东风汽车襄阳工厂验证,该系统将动力电池模组检测效率提升3.8倍,误检率从1.2%降至0.15%。特别是在应对异形曲面部件时,自适应定位算法展现显著优势。
### h2 行业典型应用案例
华为终端某型号手机天线模块曾因0.12mm的隐性翘曲导致5G信号衰减,采用本系统后实现100%在线检测覆盖率。项目组开发的"热机耦合模拟预测系统",成功将研发阶段的翘曲风险预警提前至模具设计环节。在液晶面板行业,系统搭载的纳米级波纹度分析模块,帮助京东方合肥产线将大尺寸OLED屏的亮度均匀性标准差降低至1.8nit。
## 质量保障与标准化建设
项目构建的全生命周期质量管理体系,涵盖从传感器标定到数据溯源的12个关键控制点。通过ISO/IEC17025认证的计量实验室,确保设备年漂移量小于0.3μm。在宁波某压铸企业实施时,系统结合MES生成的工艺参数相关性矩阵,成功定位模具冷却水路设计缺陷,使汽车中控面板翘曲不良率从5.7%降至0.9%。目前该检测方法已纳入《精密冲压件形位公差检测规范》团体标准。
## 发展趋势与战略建议
随着复合材料在航天器件中的普及,建议重点突破各向异性材料的本构模型建模技术。行业亟需建立跨企业的"智能化检测协作网络",通过5G+边缘计算实现检测数据的实时共享与工艺优化。预计到2026年,集成机器视觉的在线补偿系统将使翘曲矫正效率提升40%以上。建议行业协会牵头制定"动态工况下形变检测"国家标准,推动检测技术从被动识别向主动预防转型。
上一篇:头戴耳机的两个耳机的频率响应之差检测下一篇:稳态加速度(非破坏性的)检测
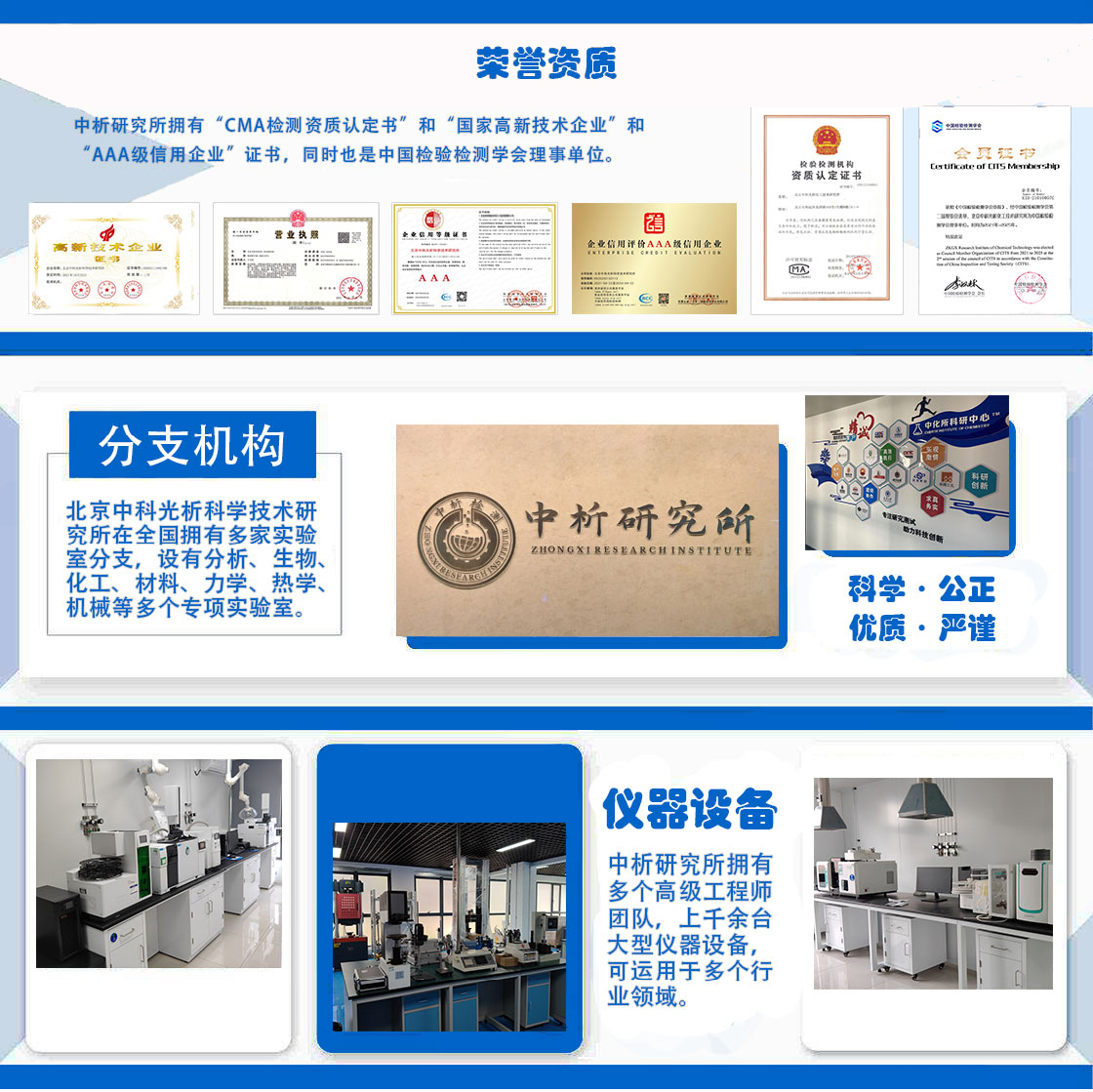
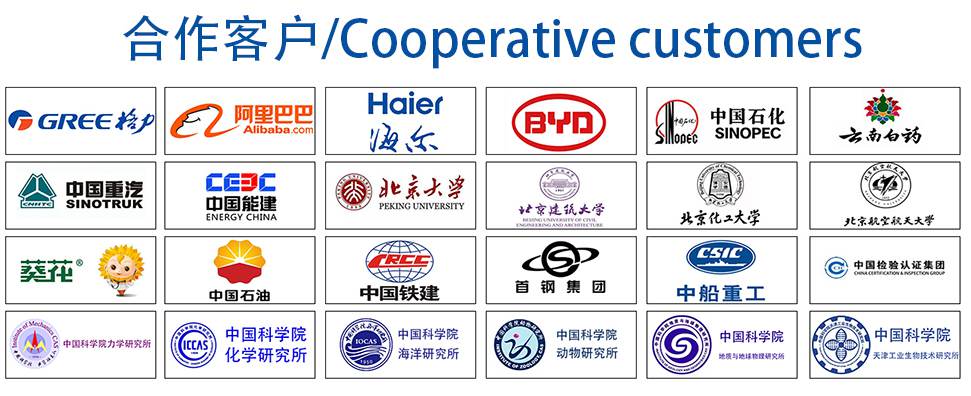
材料实验室
热门检测
推荐检测
联系电话
400-635-0567