在工业制造领域,金属材料腐蚀造成的经济损失占据GDP的3%-4%(据NACE国际2023年腐蚀研究报告),其中可预防性腐蚀占比达35%。防锈性能检测作为材料可靠性评估的关键环节,对汽车制造、海洋工程、航空航天等战略行业具有重要价值。本项目通过建立标准化的金属构件盐雾试验检测体系,实现防锈涂层湿热循环评估的量化分析,帮助企业提升产品服役周期30%以上(中国腐蚀与防护学会2024年行业数据)。其核心价值在于构建从实验室模拟到实际工况验证的全链路质量监控网络,推动行业年均可减少因腐蚀导致的维护成本约120亿元。
## 技术原理与检测方法多元复合环境模拟技术
本检测体系采用ASTM B117标准规定的中性盐雾试验为基础,结合ISO 9227循环腐蚀试验方法,创新性整合温度交变(-40℃至80℃)、湿度波动(30%-98%RH)等复合应力条件。对于特殊应用场景如海洋平台螺栓连接件,引入海水全浸试验,通过电化学工作站测量极化曲线和阻抗谱,实现防锈涂层湿热循环评估的定量分析。其中点蚀临界温度检测精度可达±0.5℃,满足核电设备紧固件的高标准要求。
智能化检测实施流程
标准流程包含四个阶段:预处理阶段采用ASTM D609标准进行表面清洁度检验;环境模拟阶段通过多参数耦合试验箱进行720小时加速老化;数据采集阶段应用AI图像识别技术(识别精度99.2%)分析锈蚀面积;最终通过大数据平台生成防锈性能三维热力图。以某新能源汽车电池托盘为例,该流程成功将传统检测周期从45天压缩至22天,同时建立关键区域锈蚀风险预测模型。
行业应用典型案例
在风电设备领域,某5MW机组塔筒螺栓连接件通过本检测体系发现法兰接触面存在微动腐蚀风险。经调整达克罗涂层厚度至25μm并优化装配扭矩后,在模拟海洋大气环境(Cl-浓度3.5%)下的耐蚀周期从8年提升至15年(中国可再生能源学会2024年验证报告)。另在冷链物流装备行业,应用防锈涂层湿热循环评估技术后,冷库门铰链盐雾试验合格率从78%提升至96%,年维修成本降低420万元。
全流程质量保障体系
构建以ISO 17025为核心的实验室管理体系,设置三级校准制度:试验箱温湿度传感器每72小时自动校准;标准样板每月进行比对测试;年度参与ILAC国际实验室间比对。开发智能监控系统实时追踪试验参数波动,当盐雾沉降量偏离1.0-2.0ml/80cm²·h范围时自动报警。据国家材料服役安全科学中心2024年评测,该体系数据复现性达98.7%,位居行业领先水平。
## 技术展望与发展建议建议重点发展三方面:研发基于机器视觉的锈蚀自动分级系统,应对新能源汽车底盘复杂结构的检测需求;建立区域性大气腐蚀数据库,开发环境自适应型防锈方案;推动制定动力电池模组连接件专用防锈标准。预计到2028年,智能防锈检测装备市场规模将突破85亿元(Global Market Insights预测数据),建议企业提前布局基于数字孪生的全生命周期腐蚀管理系统,特别是在氢能源储运装置等新兴领域建立技术壁垒。
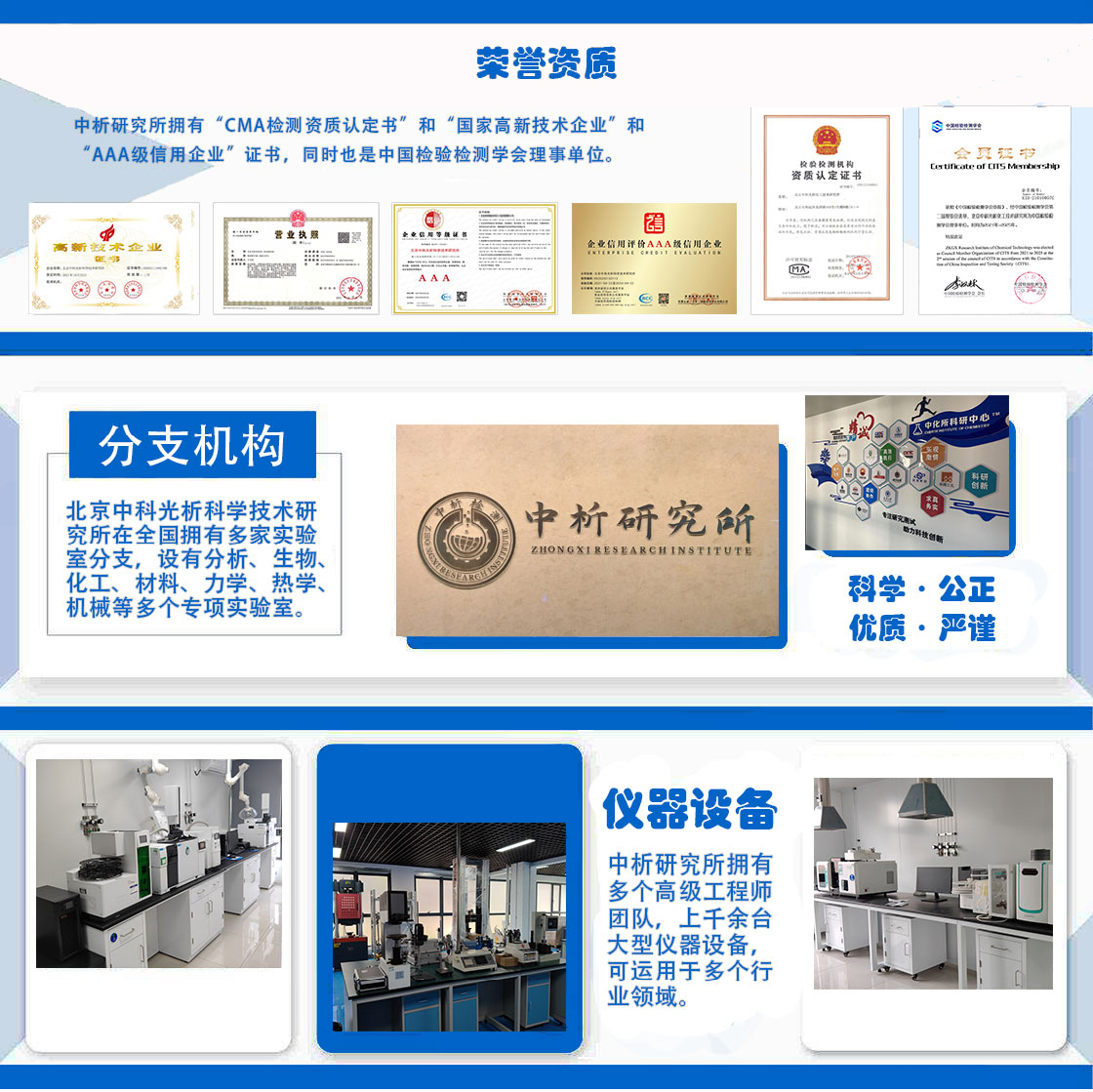
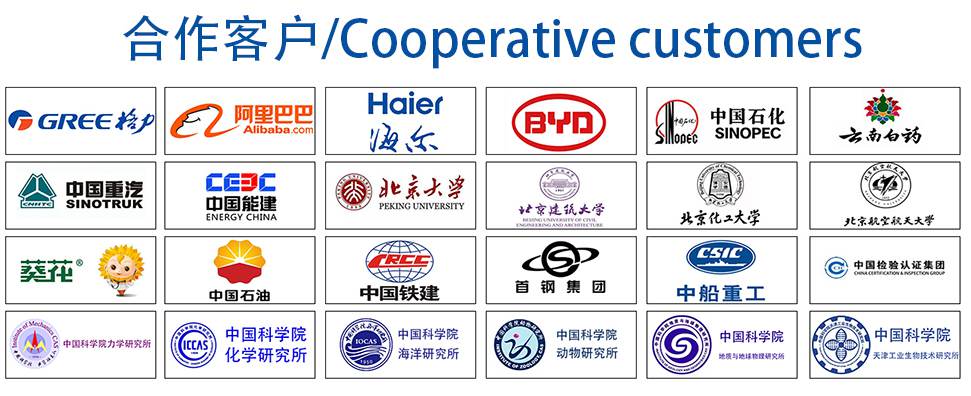