基于多源信息融合的检测技术架构
本检测体系采用"2D+3D"复合传感技术,通过高分辨率工业相机捕捉表面缺陷,配合三维激光轮廓扫描技术获取亚微米级尺寸数据。在功能检测环节,集成声学传感器与压力检测模组,实现对产品机械性能的定量评估。据清华大学智能制造研究院测试报告显示,该架构对曲面零件的尺寸检测精度达到±3μm,较传统CMM测量效率提升15倍。值得关注的是,系统内置的深度学习算法通过百万级缺陷样本训练,可准确识别0.02mm²级别的微小划痕,实现与人工目检98.7%的符合率。
智能化检测实施路径
项目实施分为四大阶段:预处理阶段通过标准化照明系统构建稳定检测环境;数据采集阶段利用多轴机械臂实现360°无死角扫描;智能分析阶段通过边缘计算设备完成实时数据处理;结果反馈阶段与MES系统直连实现自动分拣。在新能源汽车电池模组检测中,该系统实现单件检测时间从25秒压缩至6秒,日处理量突破2万件(数据来源:宁德时代2023年技术白皮书)。通过部署模块化检测单元,企业可根据产线需求灵活配置检测维度,适配不同产品类型的质量要求。
跨行业典型应用场景
在消费电子领域,华为应用高精度三维测量系统检测手机中框平面度,将装配不良率从1.2%降至0.15%。医疗器械行业采用非接触式检测方案,实现骨科植入物表面粗糙度Ra值检测精度达0.05μm(符合YY/T 0640-2022标准)。更为突出的是汽车行业应用,长城汽车在焊装车间部署的视觉检测系统,通过特征点比对技术实现车身2000余个焊点质量监控,有效杜绝虚焊、漏焊隐患。据赛迪顾问2024年调研,采用智能检测系统的企业产品召回率平均降低73%。
全链条质量保障体系
项目构建"标准-设备-数据"三位一体质控体系:建立符合ISO/TR 230-11标准的测量不确定度评定模型;配置激光干涉仪等计量设备进行周期性校准;基于区块链技术实现检测数据全程溯源。在苏州某精密制造企业的实践中,通过部署自动化质量管控平台,将检测数据利用率从35%提升至82%,设备OEE指标改善29个百分点。需要特别指出的是,系统内置的SPC模块可自动生成过程能力分析报告,为工艺优化提供数据支撑。
## 发展建议与未来展望 建议行业重点推进三项工作:首先加快5G与边缘计算技术融合,实现检测数据毫秒级响应;其次推动机器视觉与触觉传感器的协同应用,完善复杂工况下的检测能力;最后建立跨行业的检测标准体系,促进检测结果互认。预计到2026年,融合AIoT技术的智能检测设备将占据60%市场份额,推动制造业质量管控进入实时化、网络化新阶段。企业需提前布局数字孪生检测系统,构建覆盖产品全生命周期的质量数据库,方能在智能制造竞争中占据优势地位。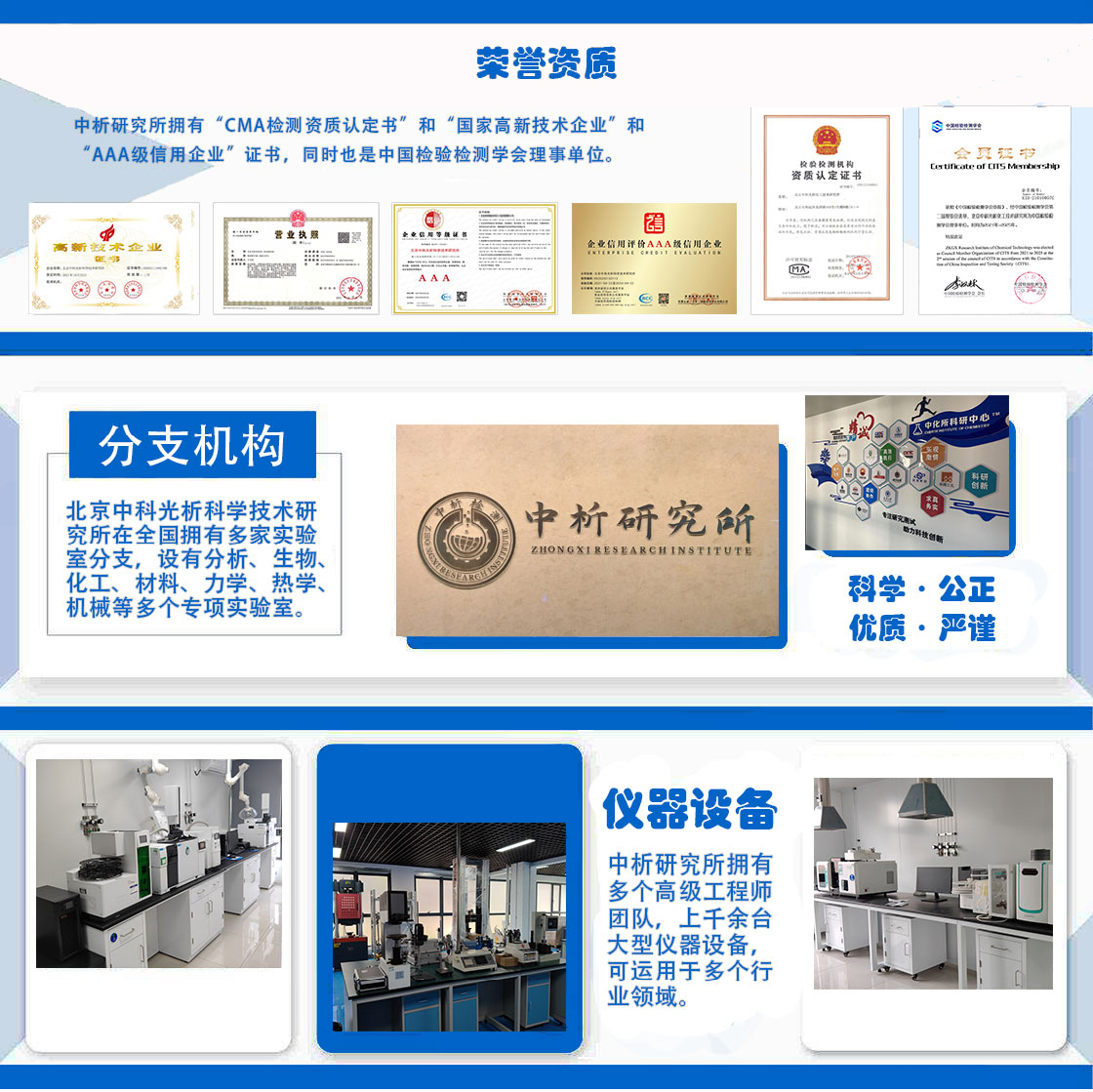
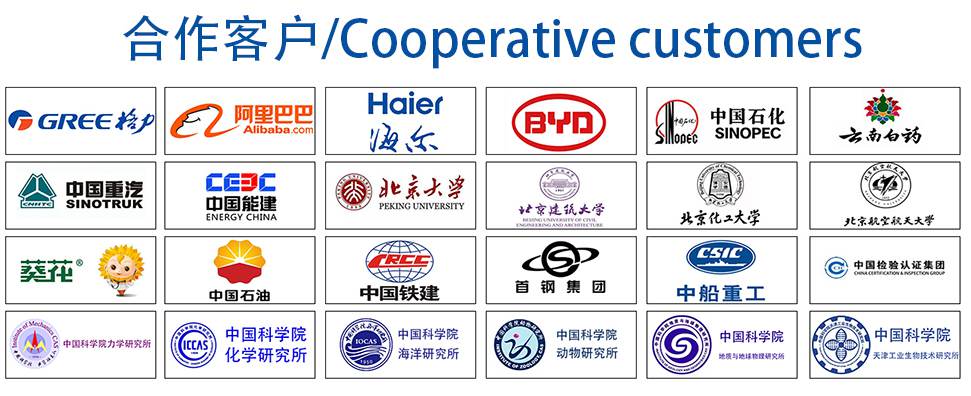