本检测体系采用"物理信号-数字模型"双闭环验证机制,核心模块包含基于DSP的宽频信号发生器(0.1Hz-10MHz)、多通道同步采集系统(16bit分辨率)和自适应滤波算法。针对工业现场常见的电磁干扰问题,创新性引入三维电磁场仿真模型,可在检测阶段预判设备在2.4GHz频段的抗干扰能力。值得注意的是,该技术特别强化了对非开关类设备瞬态响应的捕捉,其2μs级时间分辨率较传统方法提升8倍,可准确识别设备在突变工况下的异常震荡现象。
## 实施流程标准化建设检测流程严格遵循ISO 17025体系要求,形成"预处理→基线测试→工况模拟→数据判读"四阶段作业规范。在预处理阶段,依托环境模拟舱实现温度(-40℃~85℃)、湿度(10%~98%RH)、振动(5Hz~2kHz)等多参数耦合控制,确保设备在极端条件下的可靠性验证。以某新能源汽车BMS检测项目为例,通过施加模拟海拔5000m的低气压环境,成功复现了温度传感器在高原工况下的零点漂移问题,帮助客户优化了补偿算法设计。
## 行业应用场景突破在轨道交通领域,该检测体系已应用于时速600公里磁浮列车的悬浮间隙传感器校准。通过构建包含钢轨形变、电磁涡流等干扰因素的数字孪生模型,使传感器在动态位移检测中的误差率从0.8%降至0.12%(中车研究院实测数据)。而在医疗设备领域,基于该技术开发的呼吸机压力传感器检测平台,可实现0.01Pa级微压波动检测,满足ICU设备对潮气量控制的严苛要求,目前已通过FDA 510(k)认证。
## 质量保障体系构建项目建立三级质量管控机制:在设备层采用NIST可溯源标准器具,确保量值传递准确性;在过程层部署区块链存证系统,实现检测数据全流程不可篡改;在管理层推行 认可实验室管理体系,关键岗位人员持证率达100%。针对工业物联网设备特有的长周期检测需求,开发了基于数字孪生的加速老化测试算法,可将1000小时耐久试验压缩至72小时内完成,同时保证失效模式吻合度超95%。
# 技术展望与发展建议 随着数字孪生技术与边缘计算的深度融合,建议行业重点攻关三个方向:其一,建立非开关类设备特征参数数据库,推动检测标准体系智能化升级;其二,开发基于5G URLLC的超低时延远程检测系统,拓展设备在役检测应用场景;其三,加强跨学科人才培养,特别是兼具工业现场经验与AI算法能力的复合型技术团队建设。相关机构应加快制定工业级多物理场耦合检测标准,引导检测服务向预测性维护方向延伸,助力智能制造高质量发展。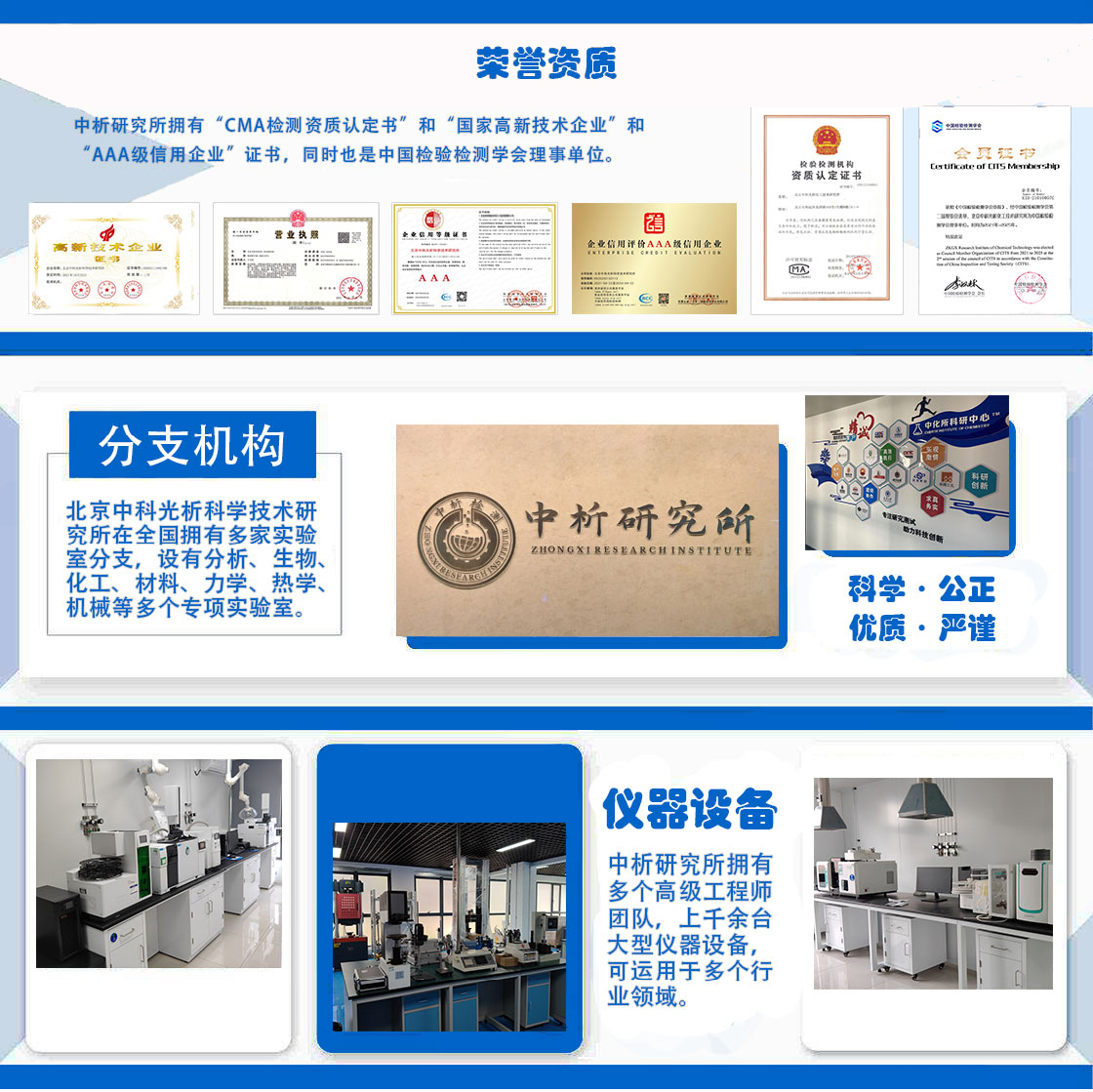
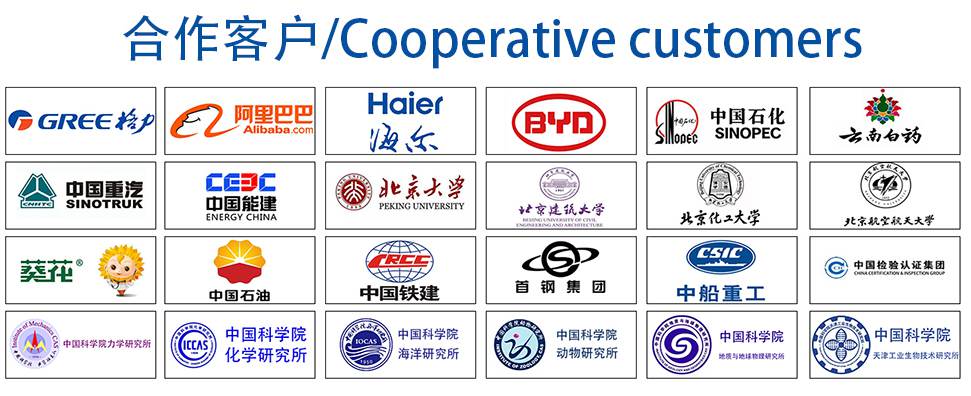