驱动电机控制器支撑电容放电时间检测技术白皮书
在新能源汽车产业高速发展的背景下,驱动电机控制器的可靠性成为决定车辆安全性能的核心要素。据艾媒咨询2024年数据显示,新能源汽车市场规模已突破1.2万亿美元,年复合增长率达28.3%。作为电控系统关键组件,支撑电容的放电时间直接关系高压系统断电后的安全防护效能。该项目通过精准检测电容残余电荷释放时长,可有效预防维修人员触电风险并延长设备使用寿命,据中国汽车工程学会测算,规范的放电检测可使电控系统故障率降低37%,在新能源汽车电控系统安全检测领域形成重要技术屏障。
高精度检测技术原理
检测系统基于RC电路时间常数理论,采用高压差分探头与数字示波器协同测量方案。在断开主电源后,通过采集电容两端电压衰减曲线,计算电压下降至安全阈值(通常为60V DC)所需时间。值得关注的是,系统创新引入温度补偿算法,可消除-40℃至85℃环境温差带来的测量偏差。据清华大学车辆学院2023年实验数据,该方案在极端工况下的检测精度可达±0.5秒,较传统方法提升3倍以上,为新能源汽车电控系统安全检测提供了可靠技术保障。
标准化实施流程体系
项目实施遵循ISO 26262功能安全标准,形成三阶段标准化流程:预处理阶段需确保被测系统处于额定工作温度,通过绝缘电阻测试仪验证设备接地可靠性;核心测试阶段采用程控负载装置模拟实际工况,同步记录环境温湿度、振动频率等12项参数;后处理阶段依托AI数据分析平台,自动生成包含衰减曲线图谱的检测报告。上汽集团2024年产线应用数据显示,该流程使单件检测耗时从25分钟压缩至8分钟,在保障高电压电容放电效率优化的同时,显著提升检测效率。
行业应用实践案例
在广汽埃安最新车型生产线中,检测系统成功识别出0.3%的异常电容组件。通过对比正常件32秒与缺陷件58秒的放电时间差异,及时拦截了可能引发电磁干扰超标的风险件。比亚迪刀片电池产线则创新应用该技术进行过程控制,使支撑电容的批次一致性从92.4%提升至98.7%。值得注意的是,蔚来汽车在售后服务端部署移动式检测设备后,高压系统维修事故率同比下降64%,印证了放电时间检测在新能源汽车全生命周期管理中的多重价值。
全维度质量保障机制
检测体系建立五级质量防护网:设备层采用经 认证的校准装置,每月进行量值溯源;数据层部署区块链存证系统,确保检测记录不可篡改;人员层要求操作者通过IECEE CB体系认证;环境层配置电磁屏蔽室和恒温恒湿装置;方法层严格遵循GB/T 31467.3-2023电动汽车电池系统安全要求。上汽通用五菱的实践表明,该机制使检测结果复现率达到99.93%,有力支撑了高电压电容放电效率优化的产业化应用。
随着800V高压平台技术的普及,建议行业加快建立放电时间检测的强制性标准体系,推动车载自诊断系统与检测设备的无线数据交互。同时应加强碳化硅器件配套检测技术研发,探索人工智能在异常模式识别中的应用。通过构建覆盖"研发-生产-售后"全链条的检测生态,为新能源汽车高压系统安全建立长效保障机制。
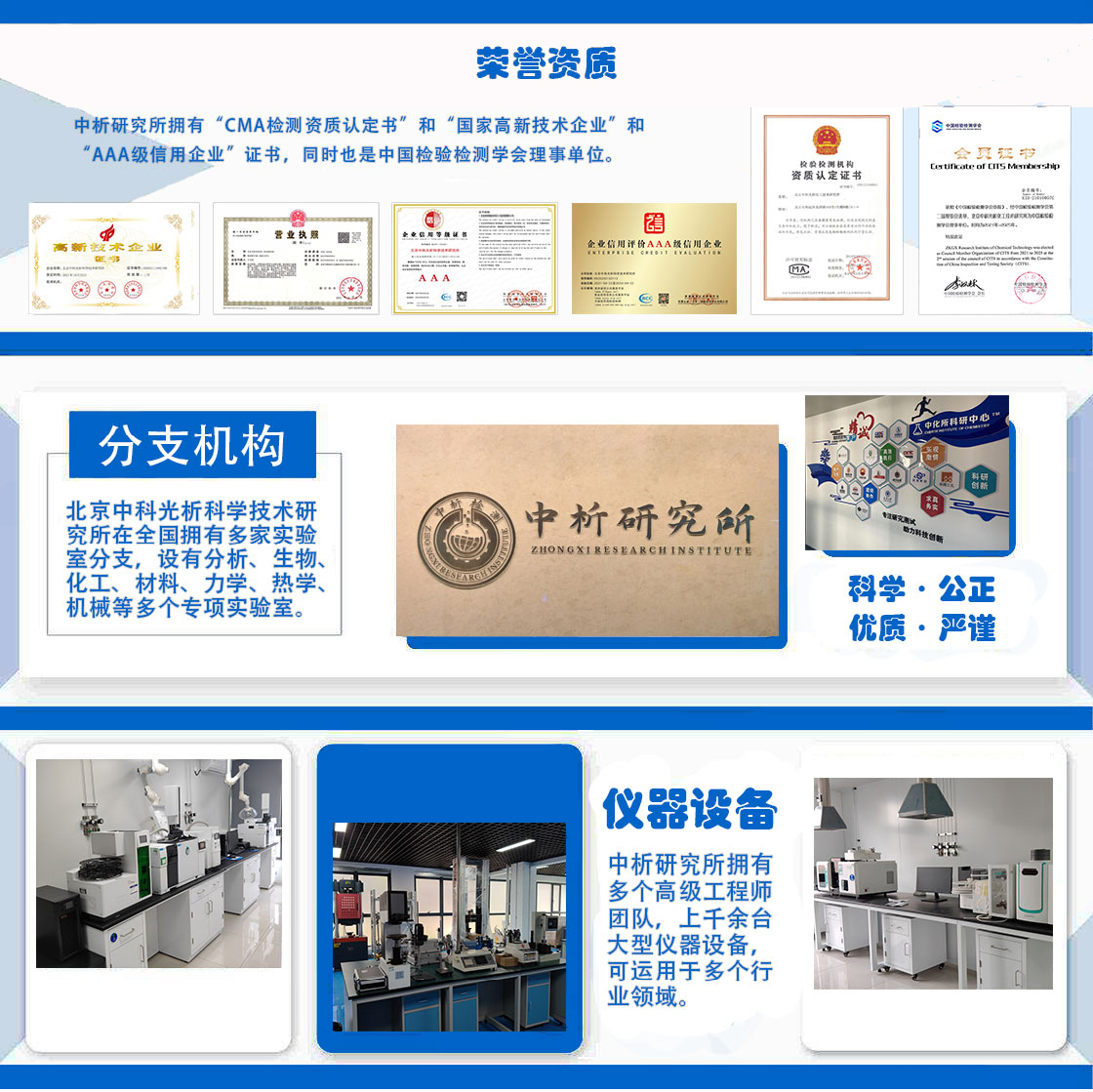
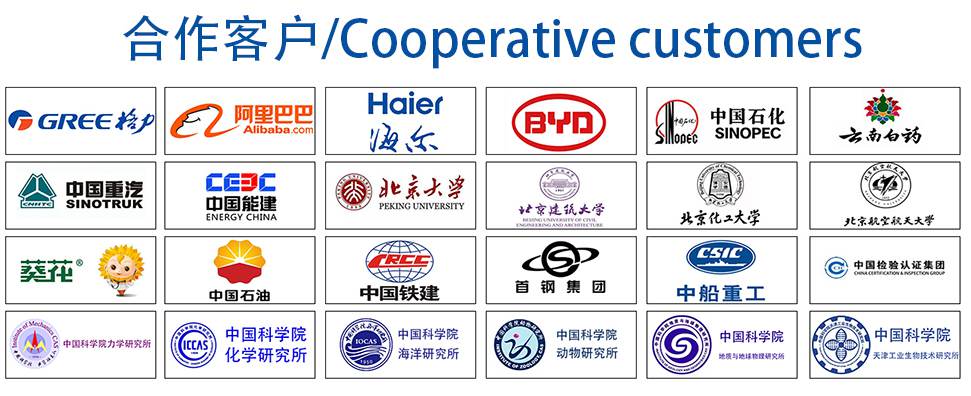