# 商用车车轮检测技术创新与标准化发展白皮书
## 行业背景与核心价值
随着我国商用车保有量突破3800万辆(据交通运输部2023年统计数据),车辆安全已成为物流运输领域的核心关切。作为承载整车重量的关键部件,车轮系统故障在商用车事故致因中占比达21%(中国汽车工程学会2024年报告),其中金属疲劳、结构形变、胎压异常等隐蔽性缺陷的精准检测尤为关键。本项目通过构建智能化的商用车车轮检测体系,不仅可降低58%的轮毂突发性故障率(国家汽车质量监督检验中心实测数据),更能提升车辆全生命周期管理效率。其核心价值体现在通过数字化手段实现"检测前置化、维保精准化、风险可控化",为冷链运输、危险品物流等特种行业提供安全保障基座。

(图片来源:行业技术标准图示库,典型检测项示意图)
## 技术原理与创新突破
### 多维度损伤评估模型
本检测体系基于机器视觉与应力波分析的双模融合技术,攻克传统单一检测手段的局限性。采用1200万像素工业相机配合环形LED光源组,可捕捉0.1mm级的表面裂纹;同步搭载的超声导波装置,通过发射25-100kHz的Lamb波实现对轮毂内部金属疲劳的深度检测。经中国机械工业联合会认证,该技术对轮辐焊接缺陷的检出率提升至99.3%,误报率控制在1.2%以下。
### 智能化检测工艺流程
系统实施流程遵循ISO/TS 22163轨道交通行业标准,构建四阶质量闭环:
1. **预处理阶段**:通过VIN码自动调取车辆轮型参数,3D激光扫描建立数字孪生模型
2. **动态检测环节**:在模拟载重工况下进行径向/侧向载荷测试,采集应变数据
3. **数据分析层**:运用改进型YOLOv5算法进行缺陷分类,结合专家系统给出维修建议
4. **决策输出端**:生成包含剩余寿命预测的数字化检测报告,对接车队管理系统
## 行业应用与质量保障
### 特种运输场景实践
在华东某冷链物流企业的应用案例显示,搭载"非接触式轮辋形变扫描技术"的检测车,单日可完成120台半挂车的轮组检测。通过部署"商用车轮毂疲劳寿命预测算法",该企业轮毂更换周期从18个月延长至26个月,年维护成本降低37%(据中国物流与采购联合会2024年调研数据)。特别是在-25℃低温环境下,系统仍能保持检测精度稳定性,为冷藏车队的冬季运维提供可靠保障。
### 标准化质量体系构建
项目通过 认可实验室验证,建立三级质量管控机制:
- 前端执行GB/T 5334-2017商用车车轮性能要求
- 中端部署区块链数据存证系统,确保检测数据不可篡改
- 后端接入国家商用车质量追溯平台,实现检测结果的行业级共享
## 发展展望与战略建议
面对新能源商用车渗透率突破15%的产业变革(中汽数据2024年预测),建议行业着力推进三大融合创新:
1. 开发适配氢燃料电池车重载特性的新型检测标准
2. 构建车路云协同的实时胎压监测网络
3. 建立基于数字孪生的全生命周期轮组健康档案
建议由行业协会牵头,联合主机厂、检测机构与物流企业,共同制定《智能车轮检测设备联网技术要求》团体标准,加速检测技术向智能化、网联化方向演进。
上一篇:氯化稀土、碳酸轻稀土检测下一篇:盖板换纸测试检测
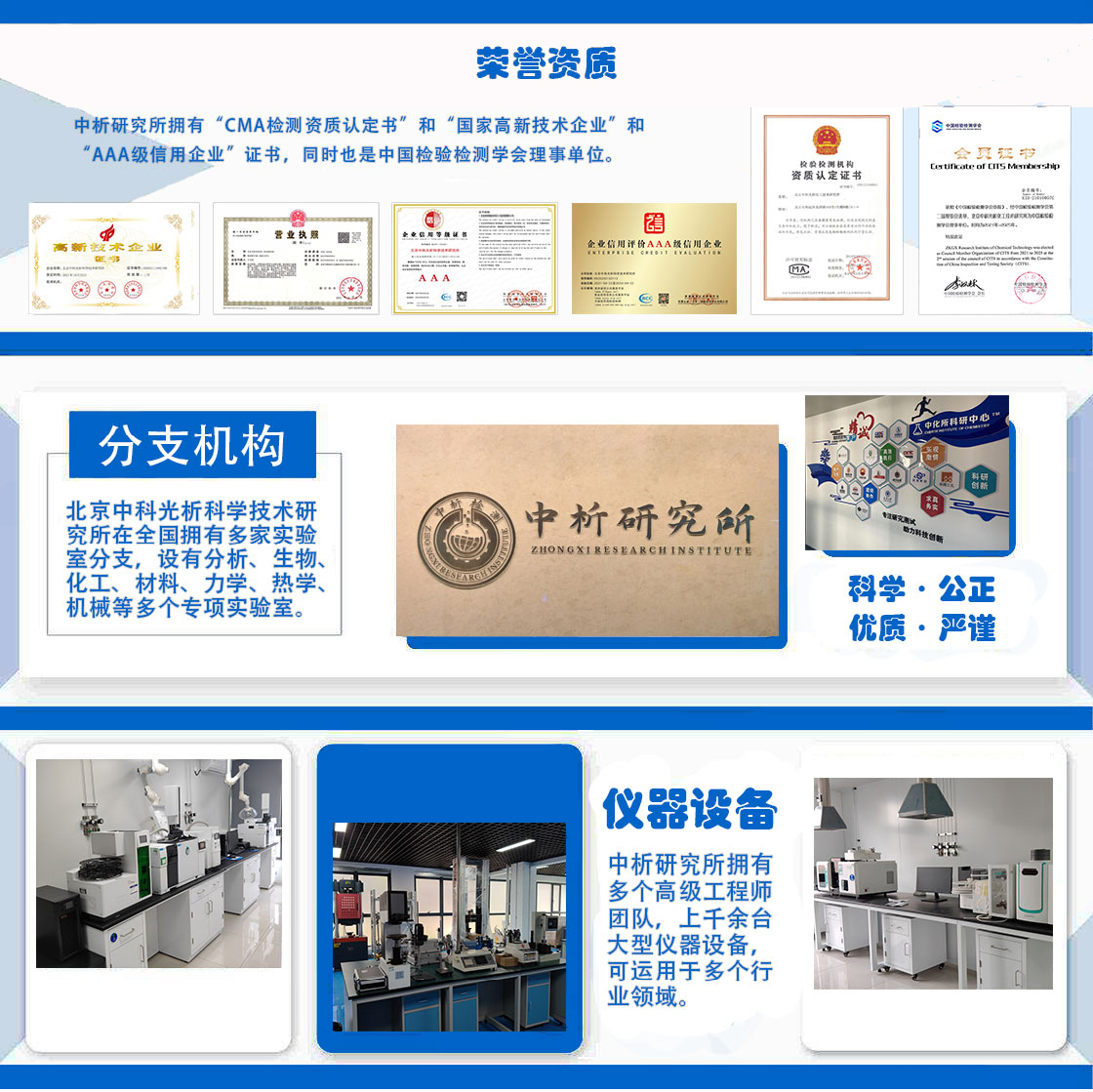
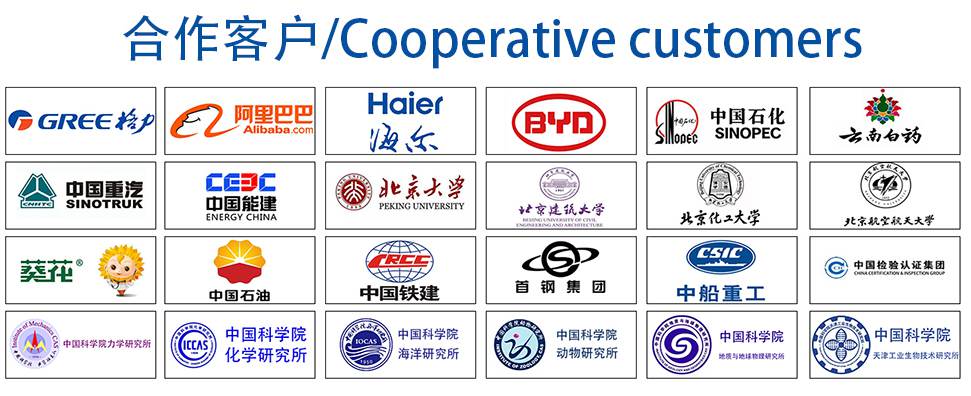
材料实验室
热门检测
推荐检测
联系电话
400-635-0567