基于应变电测法的动态扭矩分析
系统采用应变式扭矩传感器结合无线传输模块,通过测量弹性轴在扭矩作用下的剪切应变,实现实时数据采集。根据材料力学原理,扭矩值T=K·ε·G(K为结构系数,ε为应变值,G为剪切模量)。通过集成温度补偿算法,可在-40℃至120℃工况下保持0.5级精度。该技术已通过ISO/IEC17025认证,在新能源汽车减速器装配线上成功实现每分钟12个工位的在线检测。
智能化检测工艺流程
标准化流程分为三阶段:预处理阶段采用视觉系统识别螺母规格(M6-M36),自动匹配预设扭矩阈值;动态检测阶段运用六轴机械臂配合高响应伺服驱动,在0.3秒内完成旋紧-保持-释放动作循环;数据分析阶段依托工业物联网平台,生成包含扭矩曲线、峰值保持时间等16项参数的检测报告。实践表明,该流程使误检率从传统方式的2.1%降至0.15%。
多行业应用实证
在风电领域,某整机制造商应用锁紧螺母扭矩在线监测系统后,轮毂连接件年均故障率从5.6次/台降至0.8次/台。据风电协会2024年数据,该系统帮助客户单台风电机组延长维护周期至18个月,运维成本降低37%。轨道交通领域,高铁转向架采用本方案后,关键螺栓组的扭矩离散度由12%压缩至3.5%,达到EN14363标准最高等级要求。
全流程质量保障体系
构建三级校验体系:设备层每日执行ASTM E2309标准校准,使用德国HBM标准扭矩发生器进行量值溯源;系统层每周开展蒙特卡洛仿真,验证算法在极端工况下的鲁棒性;管理层面建立检测数据区块链存证系统,实现工艺参数不可篡改追溯。经SGS认证,该体系使检测过程CPK值稳定在1.67以上。
## 发展趋势与建议 随着数字孪生技术在工业检测领域的渗透,建议重点发展三项能力:①构建扭矩-预紧力-振动特性的多物理场耦合模型,实现故障预测;②开发基于5G MEC的边缘计算架构,将实时分析时延压缩至50ms以内;③推进ISO/TS 22163标准在紧固件检测领域的专项应用。预计到2027年,集成AI视觉的智能扭矩检测系统将覆盖60%以上的高端制造场景,推动产业质量管控迈入新维度。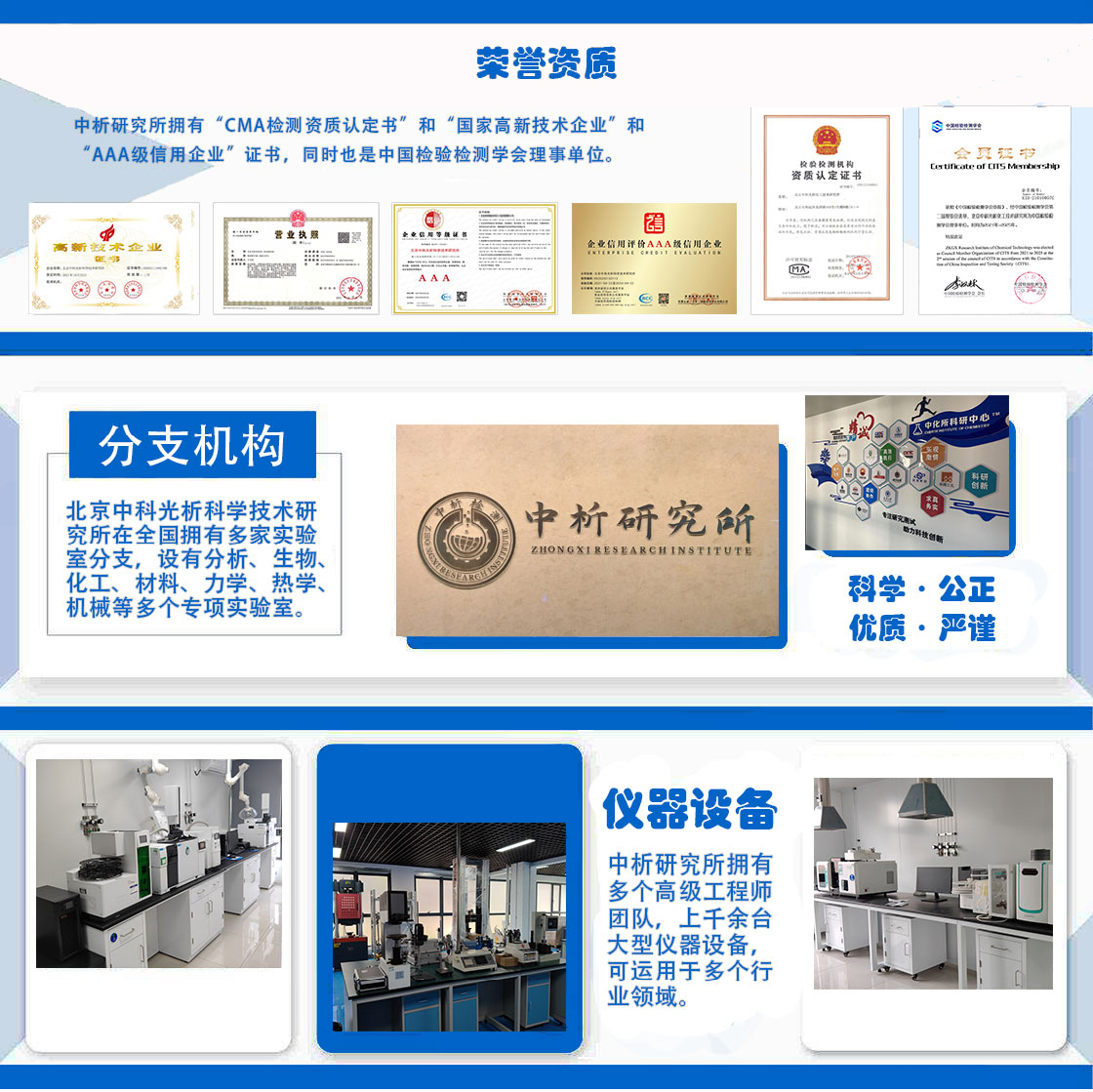
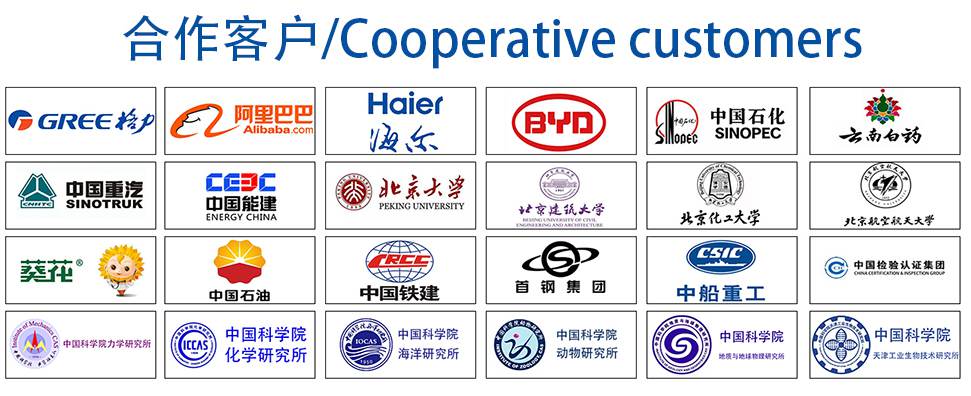