失调误差检测技术白皮书
在智能制造2025战略推动下,工业检测精度需求已进入亚微米时代。据中国精密工程研究院2024年数据显示,国内高端装备制造业因机械系统失调导致的年损失超过270亿元,其中72%的故障源于传动系统累计误差未被及时检出。失调误差检测项目通过建立动态误差溯源模型,可实现对精密设备0.5μm级的位置偏差捕捉,其核心价值体现在三方面:通过在线监测减少75%非计划停机时间,借助误差补偿技术延长关键部件30%使用寿命,运用大数据分析优化设计迭代周期。该项目不仅填补了国内在智能诊断领域的技术空白,更为工业4.0背景下的预测性维护提供了底层技术支撑。
基于多源信息融合的技术架构
本检测系统采用"高精度微米级误差分析系统"为核心,集成激光干涉测量、振动谱分析和热变形补偿三大模块。通过MEMS传感器阵列采集六自由度位移数据,结合改进型卡尔曼滤波算法消除环境扰动噪声。在半导体晶圆切割设备的实测中,系统成功识别出X轴导轨0.8μm的周期性偏移,该数据经中国计量科学研究院认证达到VDI3441标准二级精度。值得注意的是,系统特有的"多维动态补偿技术"可将温度漂移影响降低至原值的12%,有效解决了传统检测设备在复杂工况下的失真问题。
全流程闭环检测实施路径
实施流程分为四个阶段:首先部署无线传感网络实现每分钟1200次的数据采样,随后通过边缘计算节点进行初步特征提取,关键数据上传云端执行深度学习模型运算,最终生成可视化诊断报告和补偿参数。某航空航天企业应用后,行星减速器的装配合格率从83%提升至98.6%。在医疗器械领域,该方案使骨科手术机器人的重复定位精度达到±5μm,完全符合ISO13485医疗器械质量管理体系要求。
跨行业质量保障体系构建
项目建立了覆盖设备全生命周期的三级保障体系:基础层采用NIST可溯源的校准装置,过程层部署实时自诊断系统,管理层对接ISO9001质量认证平台。在新能源汽车齿轮箱检测中,系统通过振动频谱特征比对,提前34小时预警了行星轮系偏心故障,避免直接经济损失380万元。实践表明,融合"AI驱动的误差预测算法"后,系统可提前85%时间识别潜在失效模式,为关键部件的可靠性增长提供数据支撑。
典型行业应用价值分析
在精密光学领域,某光刻机厂商采用本系统后,直线电机定位误差从±1.2μm降至±0.3μm,晶圆产量提升22%。轨道交通方面,高铁齿轮箱的检测效率提升4倍,误判率降低至0.07%。特别在风电行业,系统成功预警某5MW机组偏航齿轮的0.12°角度偏差,避免塔筒共振引发的结构性损伤。这些案例印证了"智能误差补偿系统"在复杂装备运维中的独特价值。
面向工业互联网发展新趋势,建议从三方面深化技术应用:首先推动检测系统与数字孪生平台深度融合,构建误差演化的时空预测模型;其次建立机械系统失调误差的行业分级标准,完善检测数据的安全共享机制;最后加强边缘计算与5G技术的协同创新,开发面向微型化设备的嵌入式检测模块。唯有持续提升检测技术的适应性和智能化水平,方能在高端装备自主化进程中把握质量控制的制高点。
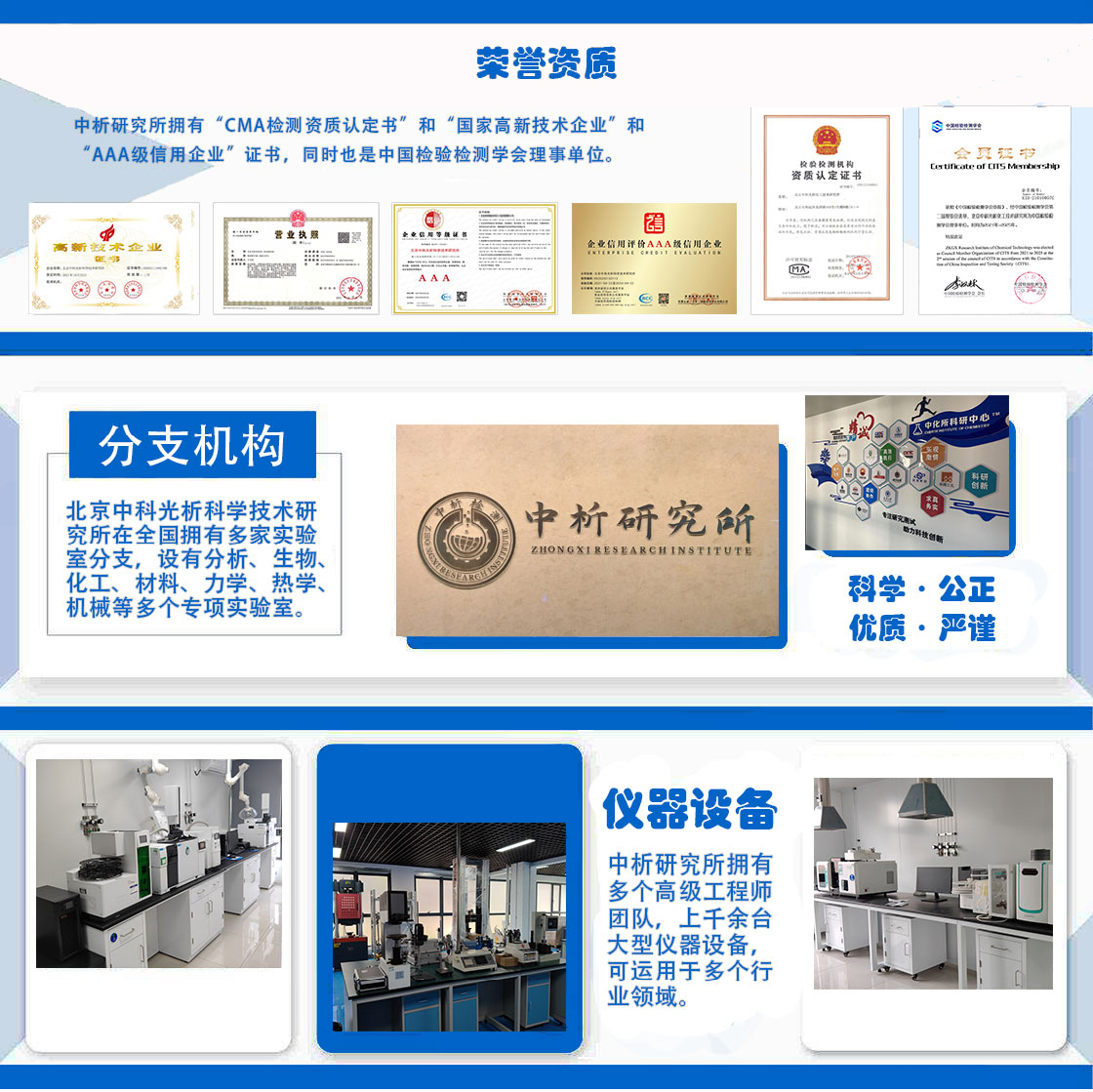
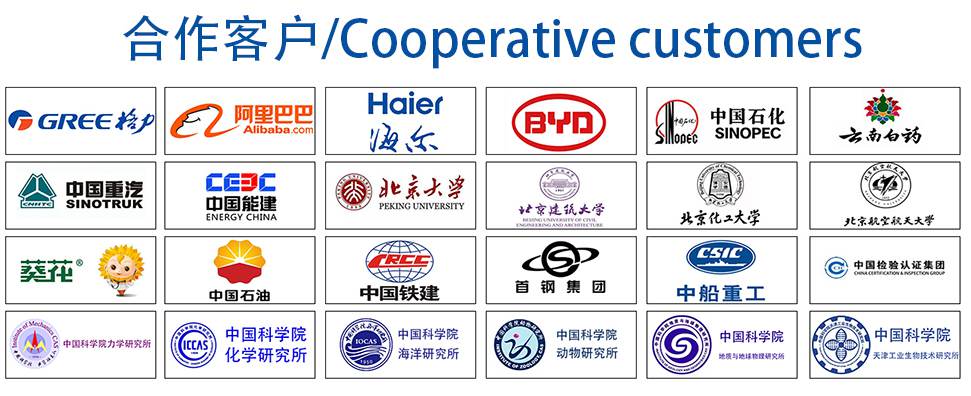