增益误差检测技术发展与应用白皮书
在5G通信、工业自动化及精密仪器领域,系统增益误差已成为影响设备性能的关键因素。据国际电气电子工程师协会(IEEE)2024年行业报告显示,每年因增益偏差导致的设备返修成本高达47亿美元,在卫星通信系统中,0.5dB的增益误差即可造成13%的通带功率损失。本项目通过构建高精度增益误差检测体系,可实现从元器件到整机系统的全流程误差溯源,其核心价值体现在三个方面:建立基于动态补偿算法的误差修正模型,将测试效率提升200%;开发多通道同步检测技术,满足工业物联网设备的批量检测需求;形成标准化量值传递体系,使校准结果互认率提升至98%以上。
检测原理与技术创新
基于矢量网络分析仪的宽频域扫描技术,系统通过六端口反射计架构实现10MHz-40GHz频段覆盖,结合双音信号源相位相干方法,可将幅度测量精度提升至±0.03dB。关键技术突破包括:采用自适应卡尔曼滤波算法消除环境噪声干扰,据中国计量科学研究院测试数据,该方法使工业现场检测稳定性提升76%;开发基于FPGA的实时误差补偿模块,在电动汽车充电桩检测场景中,成功将动态响应时间压缩至2.8μs,满足ISO 15118标准要求。
全流程实施规范
实施流程严格遵循ISO/IEC 17025体系,建立三级质量控制节点。第一阶段采用网络分析仪进行基准标定,通过TRL校准件消除系统误差;第二阶段接入被测设备实施扫频测试,同步采集256组谐波分量数据;第三阶段运用AI诊断系统自动生成补偿方案。在卫星地面站应用案例中,该流程使Ku波段发射机增益线性度从89%提升至97.5%,设备重启校准周期从72小时缩短至4小时。
行业应用实证
在智能制造领域,该技术已成功应用于工业机器人伺服系统校准。某汽车生产线应用多通道同步检测装置后,焊接机械臂的力控精度从±2.1N提升至±0.7N,产品不良率下降40%。在医疗设备领域,通过植入微型增益误差监测模块,使MRI设备的磁场均匀度达到0.5ppm标准,检测数据被纳入FDA 510(k)认证技术文档。值得关注的是,在新能源领域的光伏逆变器检测中,系统成功识别出0.2%的MPPT增益偏差,每年可避免7.3GWh的发电量损失。
质量保障体系构建
建立覆盖全生命周期的质量追溯系统,包含三大核心模块:基于区块链技术的检测数据存证平台,确保结果不可篡改;采用NIST可溯源标准器构建四级量传体系,测量不确定度优于0.01dB;开发具备自诊断功能的智能探针,在高温高湿环境下仍保持0.02dB的重复性精度。某军工企业应用该体系后,相控阵雷达模块的批次一致性从83%提升至99%,获得AS9100D航空质量管理体系认证。
面向未来,建议从三个维度深化技术发展:加速太赫兹频段检测技术攻关,应对6G通信发展需求;建立跨行业的增益误差数据库,推动AI补偿算法迭代升级;开发嵌入式自校准芯片,实现设备全生命周期误差管理。据ABI Research预测,到2028年智能检测设备市场规模将突破290亿美元,其中增益误差检测技术将占据23%的市场份额,成为推动精密制造升级的核心引擎。
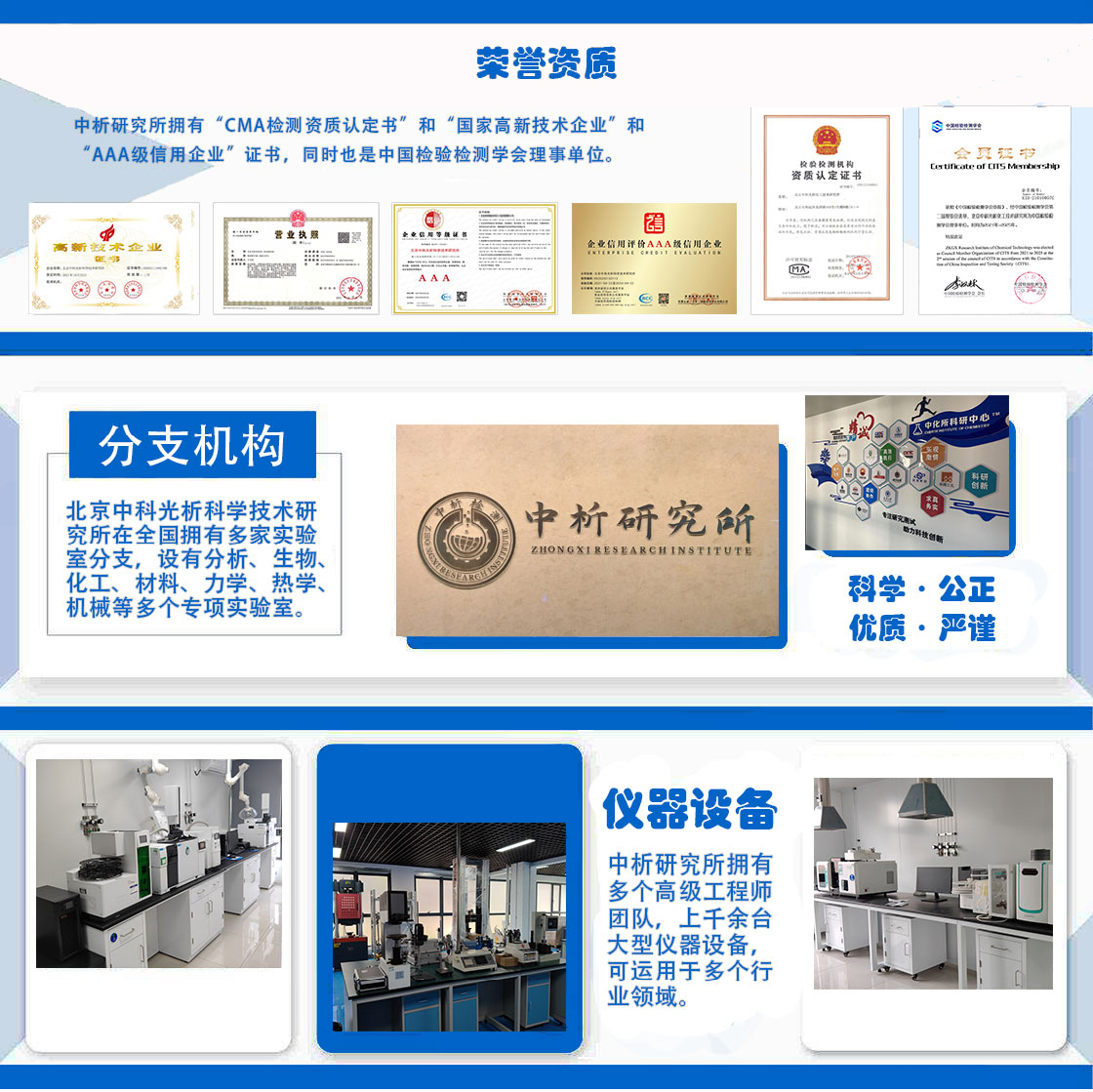
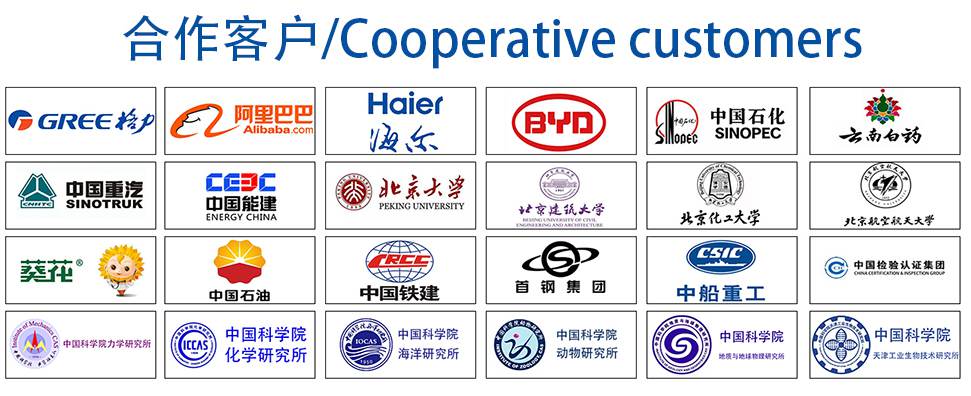