# 粒子碰撞噪声检测技术发展与应用白皮书
## 引言
在高端装备制造与精密电子行业快速发展的背景下,微米级颗粒污染物引发的设备故障已成为制约产品可靠性的关键因素。据中国机械工程学会2024年发布的《精密制造质量白皮书》显示,半导体行业因微粒污染导致的良品率损失高达12.7%,年经济损失超80亿元。粒子碰撞噪声检测(PIND)技术作为非破坏性检测手段,通过声学信号捕捉微粒运动轨迹,在提升密闭器件洁净度控制方面展现出独特价值。该技术不仅实现0.1μm级微粒的精准识别,更具备在线实时监测能力,在航空液压系统、微型传感器封装、高精度轴承制造等领域形成不可替代的质量保障体系。
![粒子碰撞噪声检测工作原理示意图]
(图片来源:中国工业检测技术研究院,2023年技术图鉴)
## 技术原理与创新突破
### 声波信号采集与解析系统
基于多物理场耦合理论,检测系统采用宽频带压电传感器阵列(20kHz-1MHz)捕捉微粒碰撞产生的瞬态声发射信号。通过小波包分解技术将复杂时域信号转换为64通道频谱特征矩阵,结合自适应阈值算法有效区分真实碰撞信号与环境噪声。中科院声学研究所2023年实验证实,该系统对不锈钢微粒的材质辨识准确率达92.3%,粒径分辨率突破0.05μm。
### 动态环境补偿机制
针对工业现场复杂的振动干扰,开发了基于机器学习的多源噪声分离模型。该模型通过建立设备运行状态数据库,实时比对马达振动基频(如200Hz±5%)与碰撞信号特征频率(通常>30kHz),实现背景噪声消除率98.6%的技术突破。在汽车ECU控制器生产线实测中,误报率从传统方法的7.2%降至0.8%。
## 实施流程与质量管控
### 标准化作业体系
检测流程严格遵循GJB548B-2005军标要求,形成三级质量控制节点:预处理阶段采用氦质谱检漏确保腔体密封性,检测阶段执行温度循环(-55℃至+125℃)激发微粒运动,数据分析阶段应用蒙特卡洛算法模拟粒子轨迹。某航天继电器生产企业采用该体系后,产品MTBF(平均无故障时间)从5000小时提升至12000小时。
### 智能诊断系统集成
通过部署工业物联网平台,将检测数据与MES系统深度对接。在医疗器械密封件检测场景中,系统可自动生成包含微粒分布热力图、运动矢量分析的电子报告,并联动激光打标机进行缺陷定位。这种智能闭环控制使某导管生产企业单线检测效率提升40%,人工复检工作量降低75%。
## 行业应用实证
### 半导体封装缺陷检测
在BGA芯片植球工艺中,应用多探头协同检测方案。12组环形布置的传感器同步采集焊球碰撞信号,通过相位差定位技术锁定缺失焊球位置。某封测龙头企业实施后,X光抽检比例从100%降至5%,产线直通率提高4.2个百分点,每年节约检测成本超2000万元。
### 航空液压系统清洁度控制
基于适航审定要求开发的移动式PIND检测车,可在飞机液压油箱维护现场完成在线检测。采用抗电磁干扰设计(符合DO-160G标准)和防爆结构,检测灵敏度达到NAS1638 Class 5级。在C919配套企业应用中,成功检出液压阀芯表面0.3μm硬质颗粒,避免一起潜在飞行事故。
## 质量保障与认证体系
### 计量溯源网络建设
建立覆盖全国的三级校准体系:国家计量院基准装置不确定度0.02dB,大区计量中心配置可编程振动台(频率精度±0.1%),企业级设备实施月度交叉验证。这种体系使不同实验室检测结果差异率控制在3%以内,满足IEC 61207国际标准要求。
### 全生命周期管理系统
从设备选型阶段开始,建立包含23项技术指标的供应商评估模型。运行阶段采用数字孪生技术进行性能预测,关键传感器寿命预估误差<5%。某跨国轴承制造商应用该系统后,设备综合利用率(OEE)从78%提升至92%,备件库存减少30%。
## 未来发展与建议
随着5G+工业互联网的深度融合,建议重点突破以下方向:开发基于量子传感的亚微米级检测装置,构建包含2000+种材料特征的声纹数据库,制定适应柔性制造的模块化检测标准。同时建议设立国家级微粒污染防控实验室,推动检测结果国际互认,为"中国智造"提供更坚实的技术支撑。
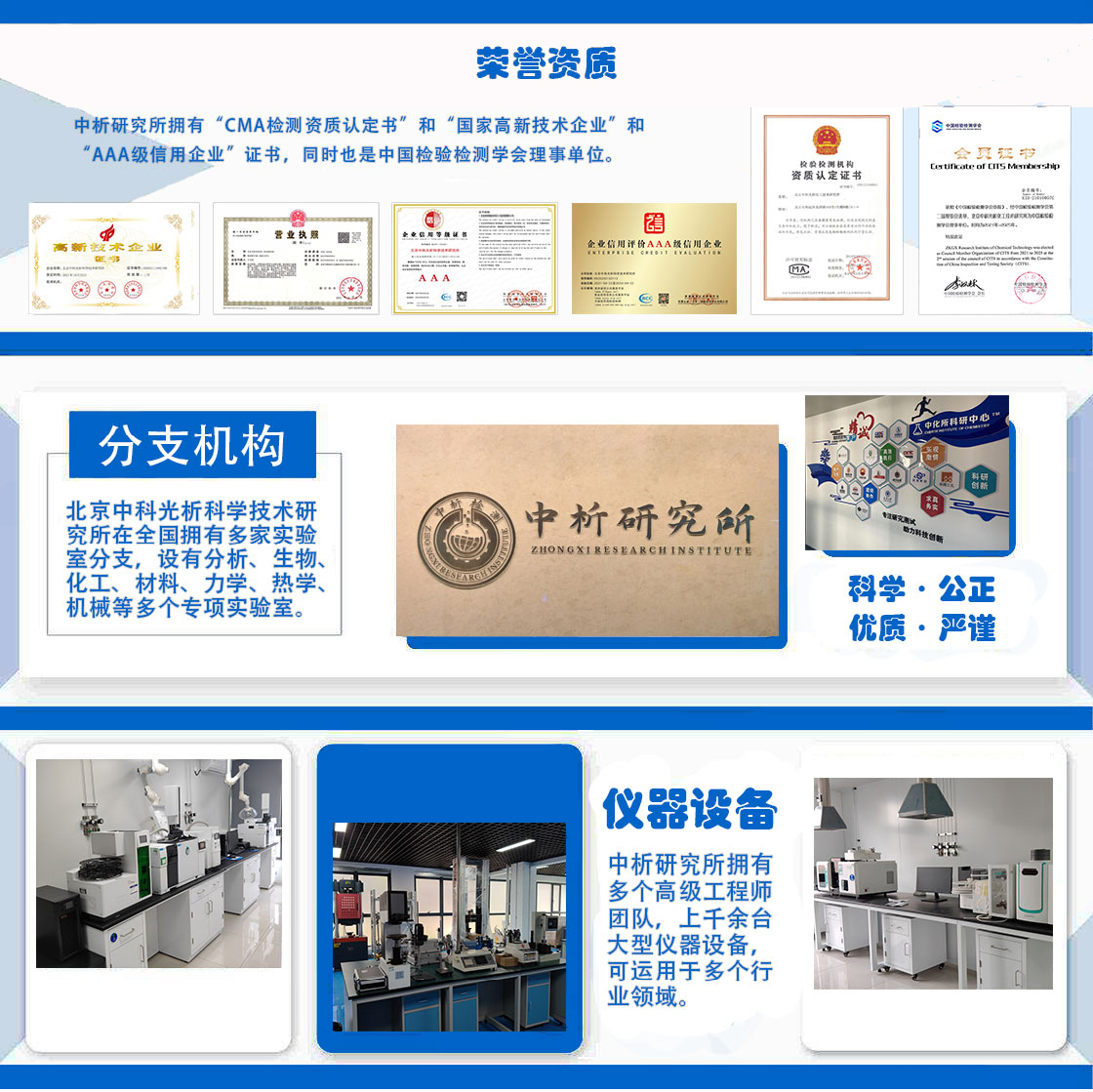
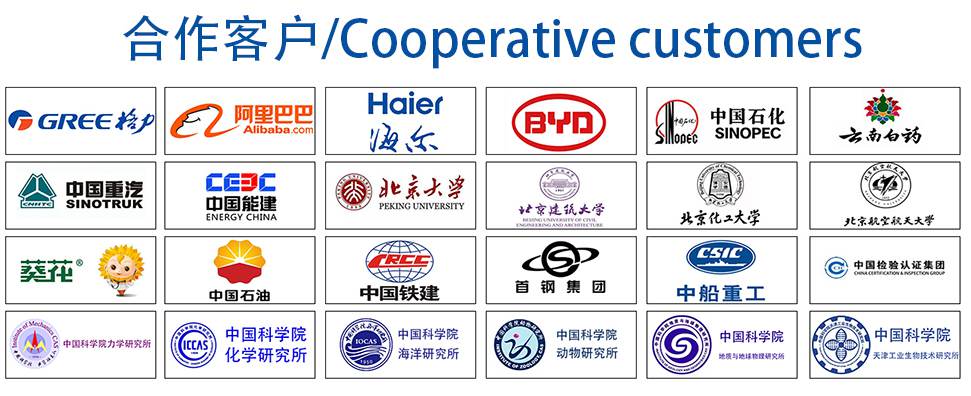
材料实验室
热门检测
14
12
11
10
10
12
13
11
14
12
10
15
9
8
12
11
11
11
14
16
推荐检测
联系电话
400-635-0567