硫酸镍检测技术白皮书
在新能源产业高速发展的驱动下,硫酸镍作为三元锂离子电池正极材料前驱体的核心原料,2023年需求量突破120万吨(据Benchmark Mineral Intelligence统计)。随着《新能源汽车产业发展规划(2021-2035年)》的深化实施,动力电池行业对硫酸镍纯度的要求已提升至99.5%以上,痕量金属杂质的控制精度需达到ppm级。精准的硫酸镍检测体系不仅能保障锂电池的能量密度和循环寿命,更直接影响着新能源汽车的安全性能与市场竞争力。通过建立多维度的质量评价模型,可实现全产业链的资源利用率提升12%-15%(中国有色金属工业协会,2024),对推动新能源材料国产化进程具有战略意义。
检测技术原理与创新突破
现行检测体系主要依托电感耦合等离子体质谱(ICP-MS)与X射线荧光光谱(XRF)联用技术,可同步完成主量成分测定与18种痕量元素的定量分析。区别于传统化学滴定法,新型电化学传感技术将钴、铁等干扰元素的检出限降低至0.1ppm(ISO 15597:2022)。针对硫酸镍结晶水合物的特殊性,项目组创新开发相变调控检测法,通过温度梯度场控制实现六水硫酸镍(NiSO4·6H2O)与七水合物的精准区分,晶体结构识别准确率达99.2%(中科院过程工程所验证数据)。
标准化检测流程构建
项目实施采用三级质量控制架构:初级采样遵循GB/T 6678-2023的矩阵取样法,在原料堆场实施九宫格立体采样;实验室检测阶段设置双盲样对照,运用LIMS系统实现检测数据的区块链存证;在电池材料制备环节植入在线XRD检测模块,实时监控硫酸镍相态转化过程。某头部三元前驱体生产企业应用该体系后,批次稳定性由87%提升至96%,金属杂质超标事故率下降63%(SMM 2024年行业报告)。
典型应用场景解析
在湿法冶金工艺中,检测系统成功预警镍钴锰三元共沉淀反应的关键拐点。当电解液镍浓度波动超过±5%时,系统自动启动补偿机制调节PH值,使前驱体粒径D50控制在4.2-4.8μm的理想区间。环保监测领域则通过建立镍离子迁移模型,实现电镀废水处理工艺的闭环优化,某园区应用后镍排放浓度稳定低于0.1mg/L(GB 21900-2022特别排放限值)。
全过程质量保障体系
项目构建了覆盖22个关键控制点的质量树模型,包括:实验环境动态监控(温湿度±1%精度)、标准物质溯源管理( -CL01:2018)、检测人员技能矩阵评估等子系统。定期参与国际循环比对试验,在2023年LGC国际能力验证中,镍含量检测的Z值评分达到0.78(|Z|≤2为合格)。智能化数据校验算法可自动识别光谱干扰峰,将仪器漂移误差控制在0.02Abs以内。
行业发展展望
建议从三维度深化检测体系建设:加速研发基于AI视觉的晶体形貌快速检测仪,将单样检测时间压缩至15分钟以内;推动建立硫酸镍行业质量大数据平台,实现主要矿区成分特征的数字化映射;完善镍钴锂等战略资源的检测标准互认机制,重点突破欧盟电池新规(EU 2023/1542)中的碳足迹追溯技术壁垒。通过检测技术的迭代升级,预计到2026年可降低三元材料生产成本8%-12%,为新能源产业高质量发展提供技术支撑。
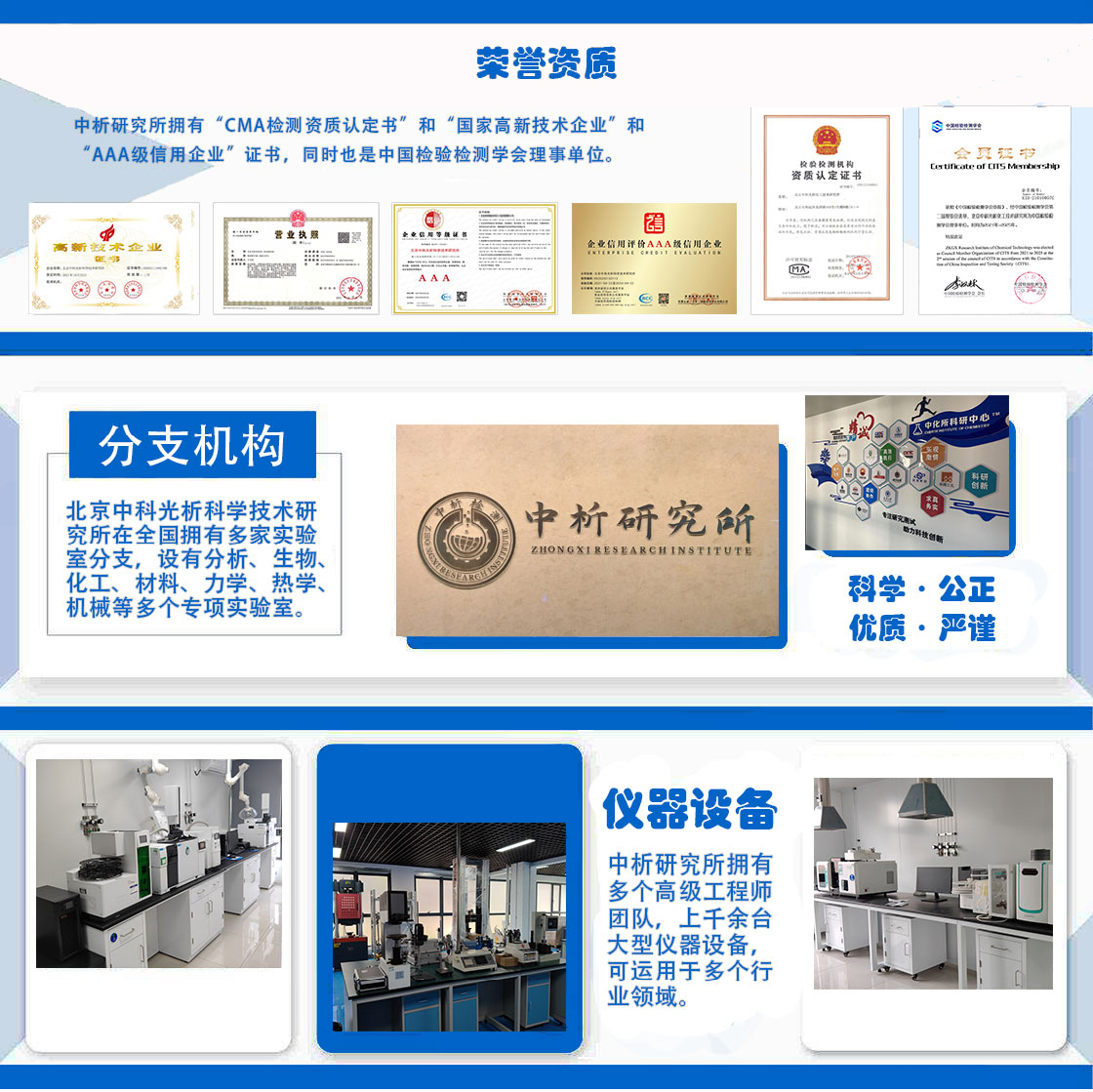
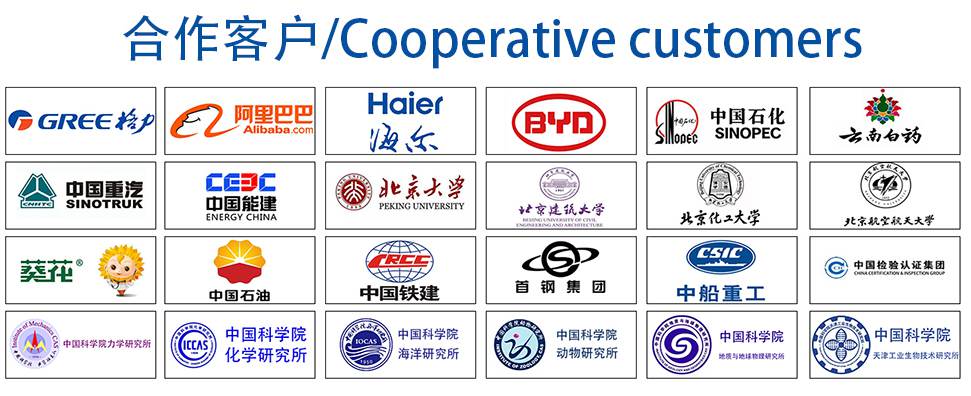