在能源转型加速推进的背景下,油气行业正面临碳排放强度考核与能效提升的双重压力。据中国石油经济技术研究院《2024年油气田开发能耗分析报告》显示,我国陆上油田集中处理站的单位原油生产综合能耗平均达到28.6千克标准煤/吨,较国际齐全水平高出12-15%。开展系统性能耗检测不仅响应了《2030年前碳达峰行动方案》中"加强重点用能设备能效评估"的要求,更是实现油气生产数字化管控的关键切入点。本项目通过构建全要素能耗计量体系,可精准识别工艺设备能效瓶颈,为实施蒸汽热泵替代、余压发电等技术改造提供数据支撑,预计可使单站年节能率达8-12%,推动油田生产向绿色低碳转型。
多维度检测技术架构
检测系统采用能量流-物质流耦合分析方法,集成智能化监测装置与边缘计算单元。通过部署高精度电磁流量计(精度±0.5%)、红外热成像仪和振动频谱仪,实时采集分离器电耗、加热炉热效率等12类核心参数。依托OPC-UA协议实现DCS系统数据互联,建立包含设备级、单元级、系统级的三层能效评价模型。在克拉玛依油田的试点应用中,该技术成功识别出电脱水电耗异常波动问题,经设备改造后每日节电达4200kWh。
标准化实施流程体系
项目实施遵循PDCA循环管理模式,具体分为四个阶段:首先通过现场勘查确定48个关键计量节点布局,然后进行为期15天的连续数据采集与异常值清洗,随后运用回归分析法建立能耗基准线,最终形成包含设备能效对标、工艺优化建议的专项报告。值得关注的是,在长庆油田某联合站的应用中,通过实施"分时电价策略+压缩机变频改造"组合方案,使单位处理能耗从31.2kgce/t降至27.8kgce/t,年节约标准煤超6000吨。
全周期质量保障机制
项目建立三级质量验证体系:初级校验采用标准表比对法,中级校验实施动态能量平衡分析,高级校验引入第三方 认证实验室。针对常见的管路热损失测量难题,创新应用分布式光纤测温技术,将空间分辨率提升至0.5米级。在胜利油田的应用实践中,该机制成功发现3处隐蔽性保温层失效点,仅此单项年减少热能损失折合标煤850吨。同时建立能耗数据区块链存证系统,确保检测结果可追溯、不可篡改。
智能化应用场景拓展
在塔里木油田的深度应用中,系统已实现与生产指挥平台的深度融合。通过接入气象数据与原油物性参数,构建了基于LSTM神经网络的能耗预测模型,使注水泵等关键设备的负荷调节响应时间缩短40%。在极端气候条件下,该系统可自动触发应急预案,如2023年寒潮期间及时调整加热炉运行参数,避免管线冻堵的同时降低燃气消耗15%。这些实践为油田构建数字孪生体系提供了重要技术支撑。
## 行业未来发展方向建议行业从三方面深化能耗检测应用:一是加快制定《油气处理场站能耗在线监测技术规范》等行业标准;二是推动检测系统与碳核算体系的衔接,实现能耗-碳排放协同管理;三是探索基于数字孪生的虚拟计量技术,在井口至外输全链条构建动态能效画像。据国家能源局规划,到2025年油气田数字化覆盖率将达85%,这为智能化能耗检测技术的规模化应用创造了良好条件,有望推动我国油田单位能耗指标进入国际第一梯队。
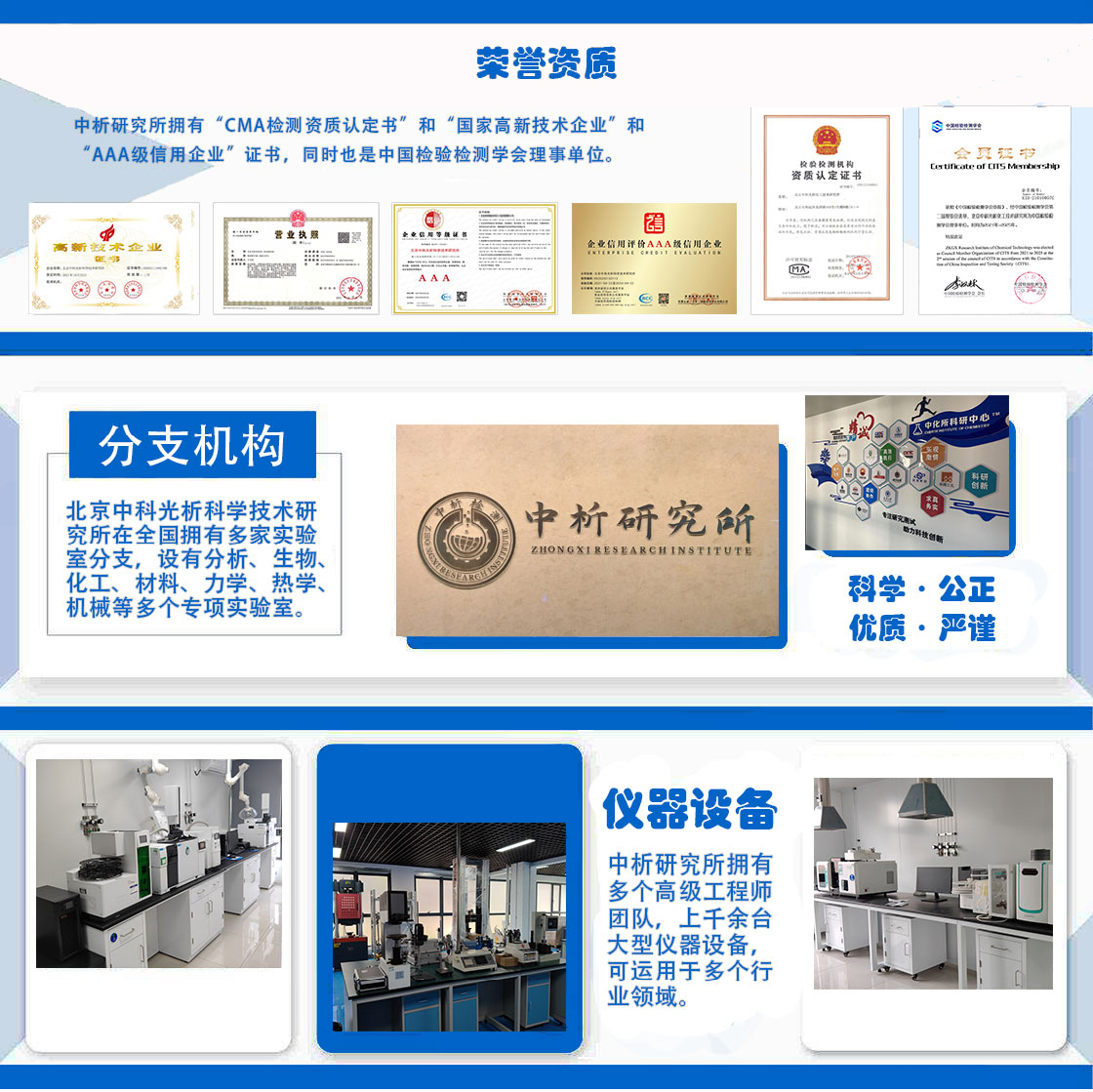
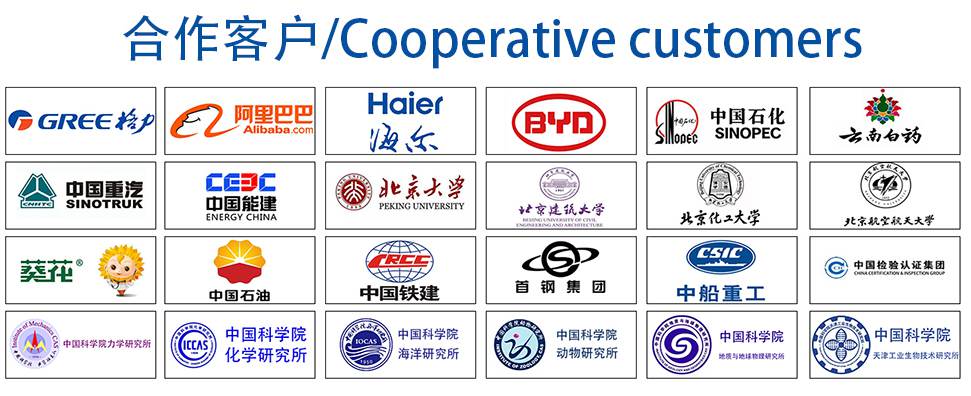