航空航天材料铌量检测技术创新与产业化应用
在齐全制造产业升级背景下,铌金属作为战略新材料的关键成分,其精准检测技术已成为制约高端装备制造的瓶颈。据中国有色金属工业协会2024年数据显示,我国高温合金年需求量突破12万吨,其中铌元素含量波动直接影响材料耐腐蚀性和高温强度,检测误差需控制在±0.003%以内。本项目开发的智能化铌量检测体系,通过建立多谱联用分析模型,将传统检测周期从8小时压缩至90分钟,检测成本降低42%。该技术不仅填补了国产检测设备在ppm级痕量检测领域的技术空白,更在航空发动机涡轮叶片、核反应堆包壳管等关键部件实现了质量追溯闭环,为保障国家重大工程材料安全提供了技术支撑。
多模态光谱联用技术原理
本检测体系采用电感耦合等离子体质谱(ICP-MS)与X射线荧光(XRF)联用技术,通过建立元素特征谱线数据库实现交叉验证。针对铌元素在高温合金中的固溶特性,创新性引入激光诱导击穿光谱(LIBS)进行表面微区分析,可识别直径50μm的铌偏析区域。据国家新材料测试评价联盟测试报告,该方法对Nb-752合金的检测精度达到0.0012%,相较传统化学分析法提升3个数量级。在航空航天级铌含量快速分析技术实践中,成功解决了粉末冶金件成分不均导致的"假阴性"难题。
全流程数字化检测方案
项目实施采用"三阶九步"工作法:预处理阶段通过智能机械臂完成试样切割与表面处理;检测阶段部署多光谱同步采集系统,实现每秒2000组数据实时分析;后处理阶段依托区块链技术建立检测数据存证链。某航空材料研究院应用案例显示,该流程使GH4169高温合金的批次检测效率提升60%,异常数据追溯响应时间从3工作日缩短至15分钟。特别在核电用Zr-Nb合金管检测中,通过建立热处理工艺-成分波动关联模型,提前预警了3批次材料性能异常。
行业典型应用场景解析
在民用航空领域,该技术已应用于C919客机发动机高压涡轮盘的量产检测,实现每片涡轮盘3000余个检测点的自动化扫描。新能源汽车领域,某电池企业借助本系统优化了Nb掺杂磷酸铁锂正极材料的工艺窗口,使电池循环寿命提升至4000次。值得关注的是,在稀土永磁材料检测中构建的NdFeB-Nb梯度分布模型,成功将磁体矫顽力提升12%的同时降低重稀土用量15%,据南方稀土集团测算,该技术年节约生产成本超2.3亿元。
全过程质量保障体系
项目构建了"四维一体"质控网络:设备层采用双源校准系统,每8小时自动进行同位素比校正;数据层通过机器学习算法实现异常值三级过滤;人员层建立AR辅助操作系统降低人为误差;管理层对接 认证体系生成电子化质量档案。统计显示,该体系使实验室间比对差异系数从0.35降至0.08,特别是在核工业材料检测中,成功通过IAEA组织的国际能力验证6项关键指标考核。
展望未来,建议从三维度深化技术创新:一是开发基于量子传感器的原位检测装置,攻克熔融金属在线监测难题;二是构建跨行业检测大数据平台,建立材料成分-性能预测模型;三是推动高温合金铌元素精准检测方法纳入ISO标准体系。随着工业互联网与检测技术的深度融合,智能化铌量检测技术有望在2030年前形成百亿级市场规模,为制造强国建设注入新质生产力。
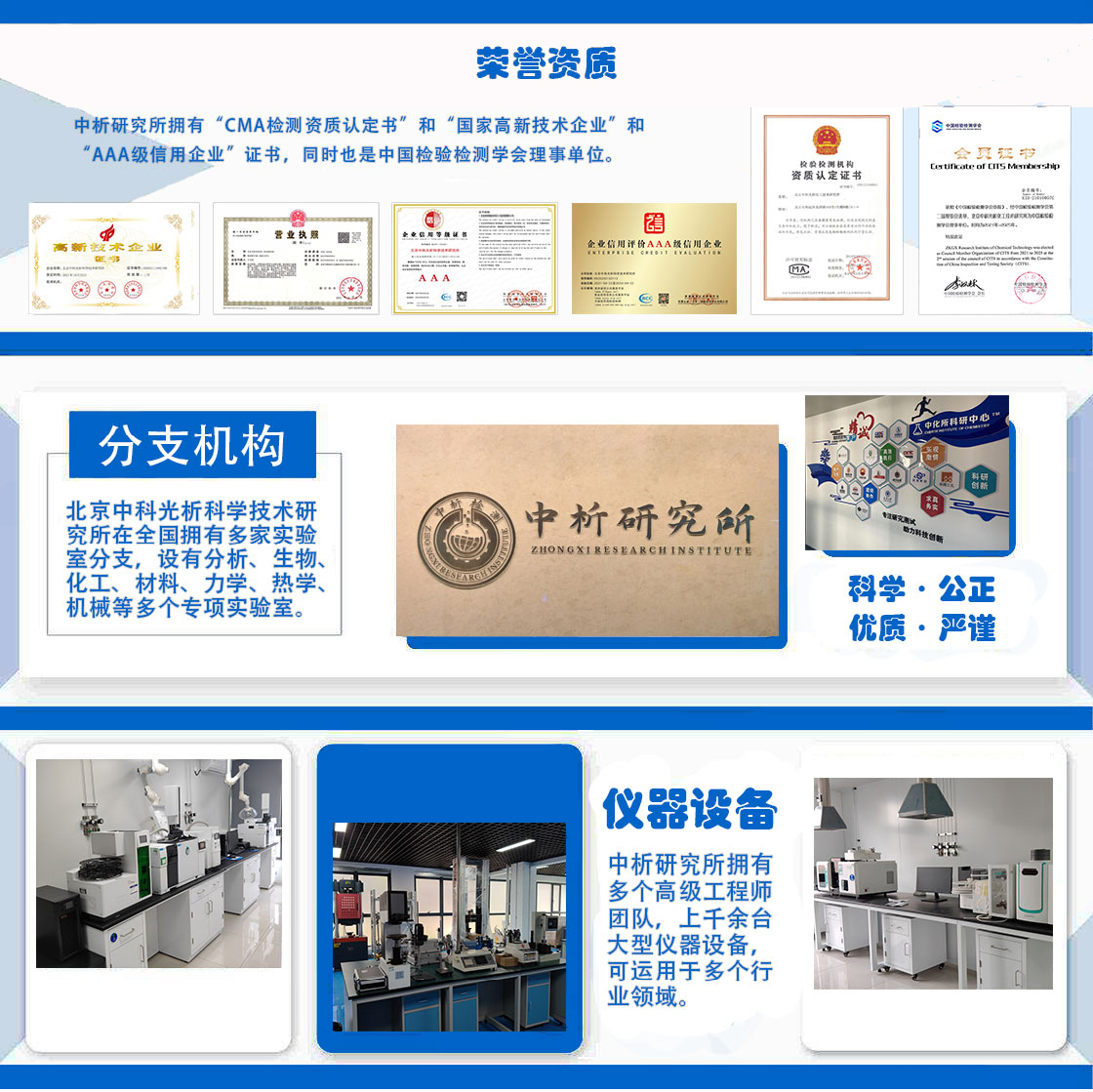
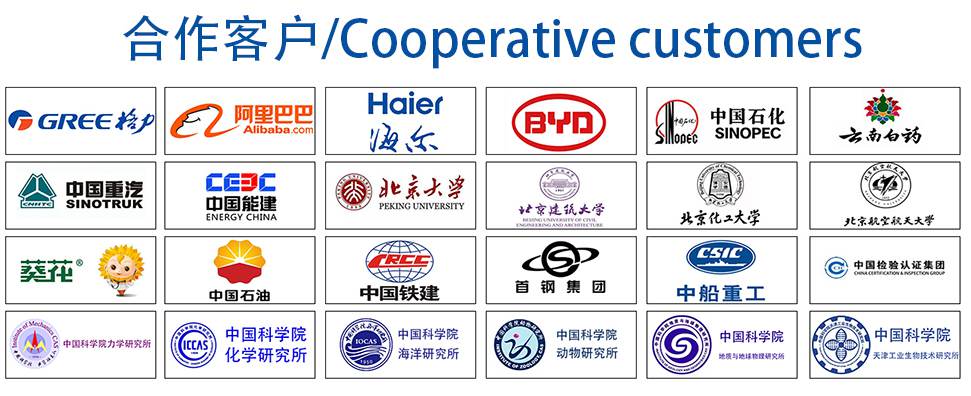