# 焦炭反应性及反应后强度检测技术研究与应用
## 行业背景与核心价值
在钢铁冶金领域,焦炭作为高炉冶炼的骨架材料和主要热源,其质量直接影响高炉顺行效率与生铁成本。据中国冶金研究院2024年数据显示,我国钢铁行业焦炭年消耗量达4.8亿吨,其中因焦炭热态性能不达标导致的燃料比升高,每年造成经济损失超120亿元。焦炭反应性(CRI)与反应后强度(CSR)作为评价其高温冶金性能的核心指标,可通过模拟高炉实际工况检测焦炭与CO₂的反应损耗率及残存强度。构建标准化的检测体系,对实现高炉高效低耗运行、推动"双碳"战略落地具有显著价值,尤其在优化配煤方案、降低碳排放强度等方面形成关键支撑。
## 技术原理与检测方法
### h2 热态反应动力学检测机理
焦炭CRI/CSR检测基于国际通用的ISO 18894:2018标准,通过高温反应炉模拟高炉软熔带环境(1100℃±5℃)。焦炭试样在CO₂气氛中反应2小时后,计算质量损失率得CRI值,再经转鼓试验测定未粉化焦炭占比得CSR值。该过程精准复现焦炭溶损反应与机械磨损的耦合效应,其中反应活化能测定(采用TGA-DSC联用技术)可解析不同煤种焦炭的微观结构差异,为建立"焦炭CRI检测技术规范"提供理论依据。
### h2 全流程标准化实施体系
检测流程涵盖采样、制样、检测、数据分析四大环节:(1)按GB/T 1997-2008进行工业焦炭取样,确保样本代表性与粒度分布合规;(2)使用颚式破碎机与筛分设备制备6-8mm标准试样;(3)在程序控温反应装置中完成恒温反应,全过程氮气保护防止氧化干扰;(4)通过智能图像分析系统(如Malvern Morphologi 4)量化焦炭孔隙结构变化,结合Minitab软件进行统计过程控制(SPC),数据误差控制在±0.5%以内。
## 行业应用与质量管控
### h2 高炉工艺优化实证案例
鞍钢集团在2023年实施"焦炭热态性能精准调控"项目,通过建立CSR>65%、CRI<25%的焦炭质量评价体系,使4350m³高炉燃料比降低8kg/t,年节约焦炭成本逾2.3亿元。宝武集团采用X射线微区分析(EPMA)技术关联焦炭各向异性指数(OTI)与CSR值,开发出基于煤岩组成的配煤优化模型,使焦炭质量波动率从12%压缩至5%以内。
### h2 全链条质量保障系统构建
检测实验室需通过 认可(依据ILAC-MRA/ -CL01),实施三级质量监督:(1)设备层采用多点校准法,反应炉温场均匀性≤±3℃;(2)操作层执行"双人平行实验"制度,CRI重复性限r≤2%;(3)数据层应用区块链存证技术,实现检测报告全生命周期可追溯。中国质量认证中心(CQC)的统计表明,该体系使焦炭质量事故率同比下降42%。
## 技术展望与发展建议
随着智能化检测装备的普及,建议从三方面深化技术应用:其一,开发在线热态性能监测装置,嵌入"高炉用焦炭质量评价体系"数字化转型;其二,建立区域性焦炭性能数据库,运用机器学习预测不同配煤方案的CRI/CSR值;其三,研制低反应性超高强度焦炭,支撑氢冶金等低碳工艺发展。据麦肯锡《冶金技术路线图》预测,至2030年智能焦炭检测技术将带动钢铁行业能效提升15%-20%,为"双碳"目标实现提供关键技术支点。
上一篇:巨尾阿丽蝇成虫形态鉴定检测下一篇:基孔肯雅病毒核酸检测
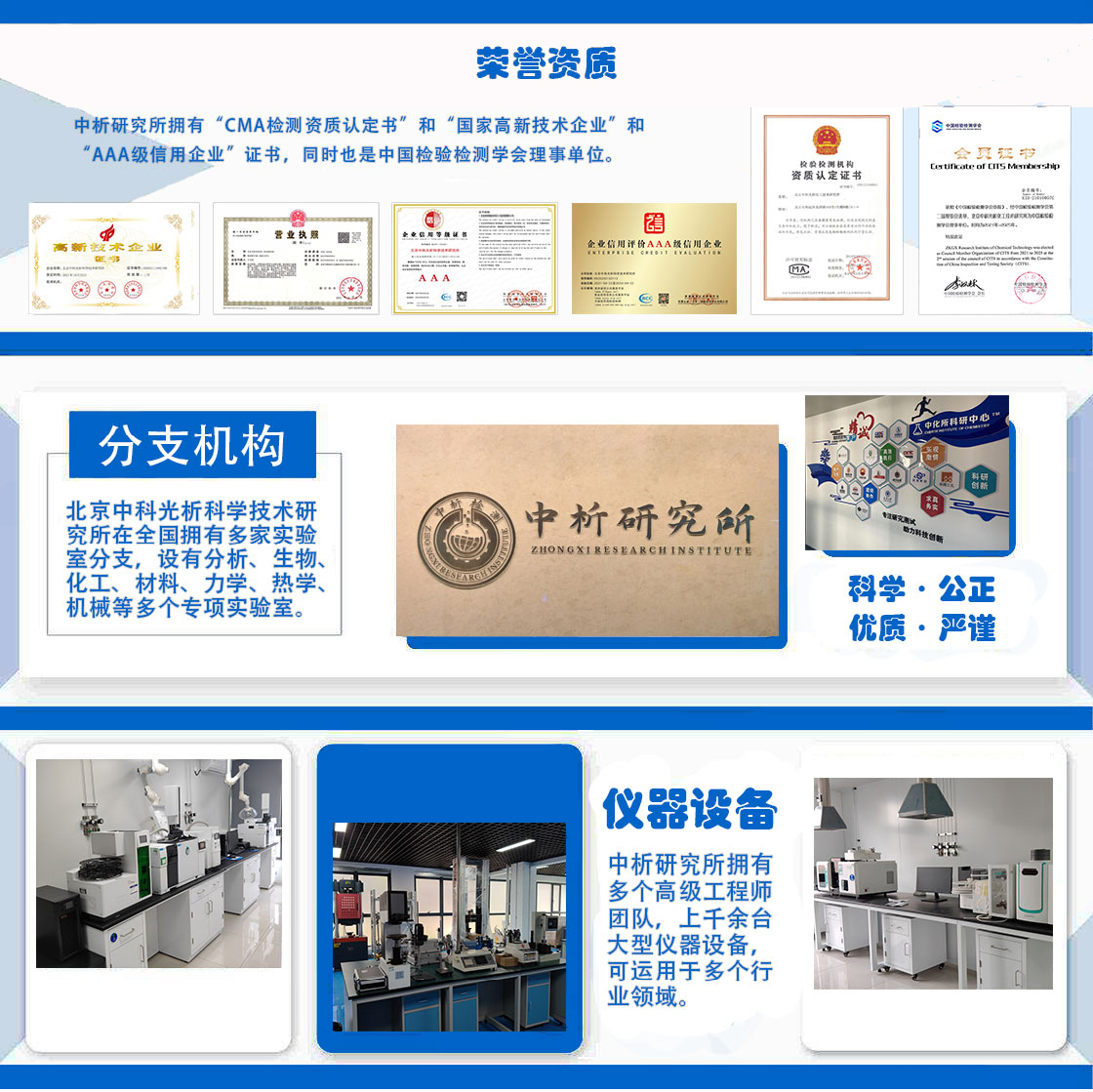
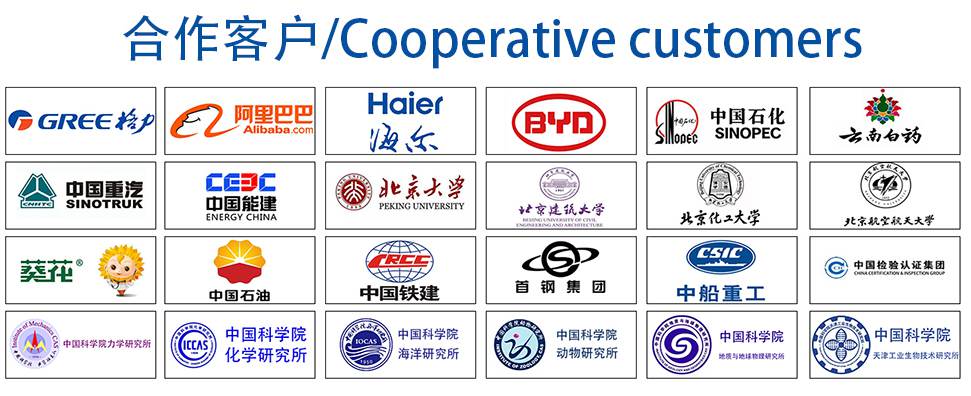
材料实验室
热门检测
15
16
13
10
14
14
13
13
15
12
14
15
9
9
12
13
14
13
16
18
推荐检测
联系电话
400-635-0567