高功率型锂离子电池包及系统检测技术规范
一、检测体系框架
检测层级 | 关键指标 | 测试目的 |
---|---|---|
单体电池 | 倍率性能、内阻、热稳定性 | 验证基础电化学性能 |
电池模组 | 均一性、散热效率 | 评估成组设计可靠性 |
电池包总成 | 结构强度、IP防护、热管理 | 检验机械与环境耐受性 |
BMS系统 | 动态均衡、SOC估算精度 | 验证智能控制能力 |
系统集成 | 整车匹配、安全保障 | 确认系统级功能实现 |
二、核心检测项目详解
(一)单体电池级检测
-
- 标准要求:UN38.3 第4.3节(1C→5C梯度测试)
- 测试方法:以5C倍率连续充放电500次,容量保持率≥95%
- 关键参数:极化电压变化≤50mV/cycle,温升速率<0.8℃/min
-
- 检测设备:HIOKI BT3563内阻测试仪
- 测试条件:-20℃~55℃温箱环境
- 验收标准:全工况内阻波动≤15%初始值
(二)模组级检测
-
- 红外热成像检测:模组内单体温差<3℃(3C放电工况)
- 液冷系统验证:冷却液流速≥8L/min时的温控效率
-
- 参照标准:GB/T 31467.3 机械振动(XYZ三轴各20小时)
- 判定标准:结构无损+容量衰减≤2%
(三)电池包总成检测
-
- IP67测试:浸水1m×30min无泄漏
- IP6K9K:高压水枪喷射(80℃水温)
-
- 触发方式:针刺/过充单体电池
- 安全要求:火焰蔓延时间>5min,无爆炸发生
(四)BMS专项检测
-
- 测试场景:SOC差异15%的人工制造
- 均衡时间:≤2小时恢复至±5%区间
-
- 模拟故障:电压采样线断开/温度传感器失效
- 响应要求:诊断延迟<100ms,故障码准确率100%
三、特殊环境测试矩阵
环境类型 | 测试参数 | 性能要求 |
---|---|---|
低温环境 | -40℃冷启动 | 30s内输出功率>标称值80% |
高海拔 | 模拟5000m海拔 | 散热系统效率衰减≤15% |
腐蚀环境 | 盐雾试验480h | 外壳腐蚀面积<5% |
湿热循环 | 85℃/85%RH×48h | 绝缘电阻>100MΩ |
四、检测标准体系
-
- GB 38031-2020《电动汽车用动力蓄电池安全要求》
- ECE R100.03 电动车电池系统认证
-
- ISO 19453:2018 道路车辆-电动推进系统安全
- SAE J2929 锂离子电池系统安全标准
五、前沿检测技术发展
- 数字孪生测试平台:搭建虚拟电池模型,实现80%前期验证线上化
- AI异常检测系统:通过云端大数据分析提前识别潜在故障
- 快充老化加速测试:采用3倍电流加速模拟5年使用寿命
结语
上一篇:防静电产品检测下一篇:破碎缩分联 合制样设备检测
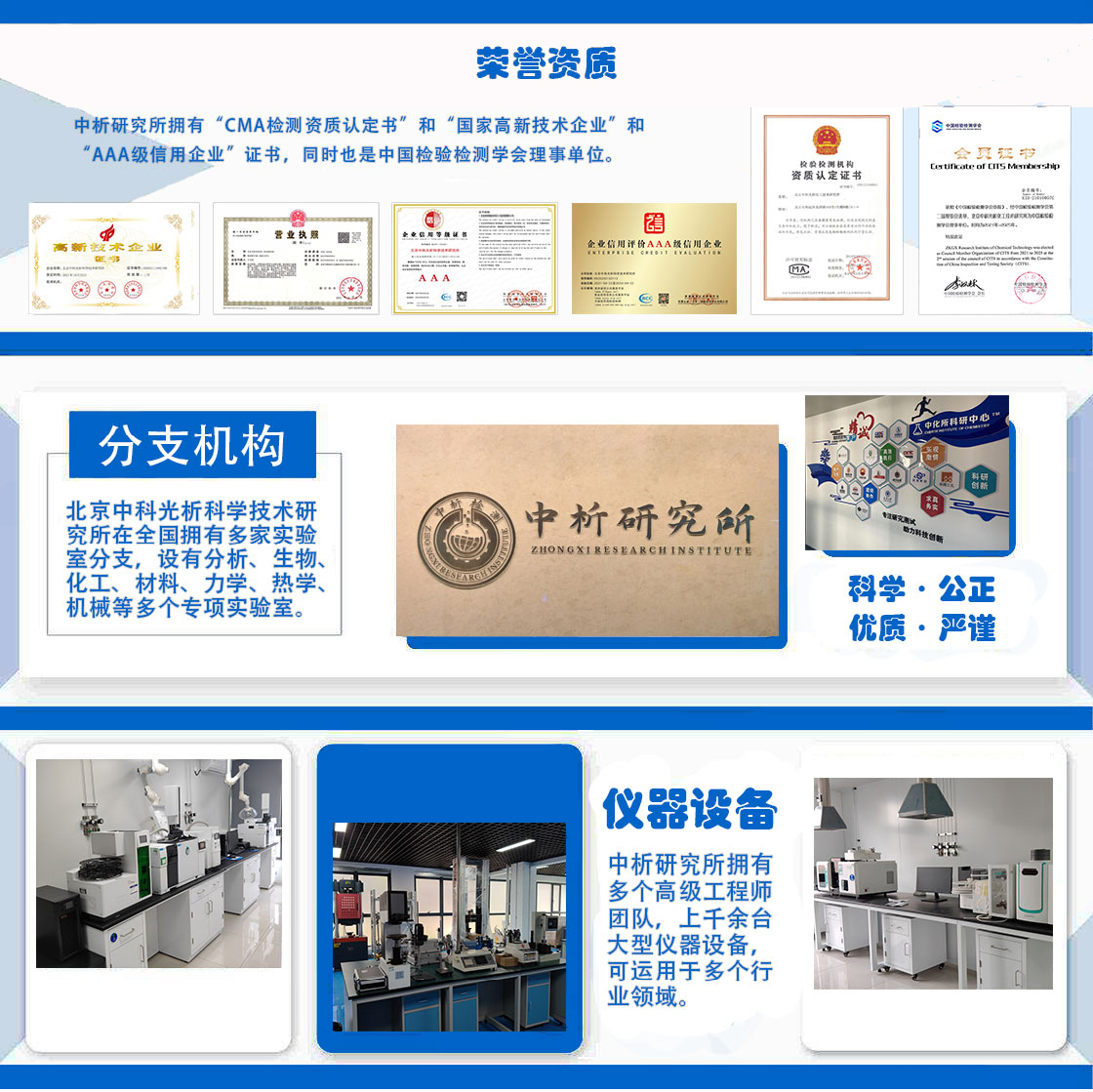
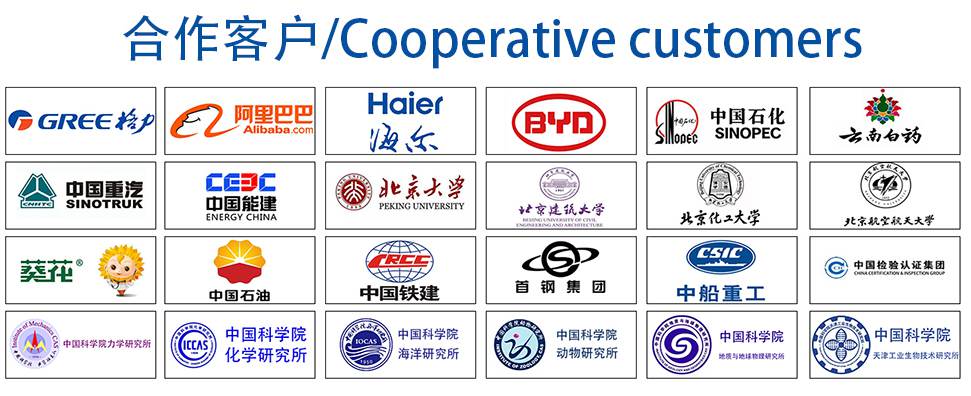
材料实验室
热门检测
271
228
202
211
210
215
225
218
228
229
215
214
218
216
210
205
221
207
220
214
推荐检测
联系电话
400-635-0567