金属材料及其覆盖层检测:核心检测项目详解
一、金属材料本体的检测项目
-
- 检测内容:测定金属材料中元素种类及含量(如碳钢的C、Mn、Si元素,铝合金的Mg、Zn元素等)。
- 常用方法:
- 光谱分析(OES、ICP-AES)
- 化学滴定法(GB/T 223系列)
- X射线荧光光谱(XRF, ISO 3497)
- 标准参考:ASTM E415(碳钢)、GB/T 20975(铝合金)。
-
- 检测内容:评估材料强度、塑性和韧性。
- 核心指标:
- 拉伸性能(屈服强度、抗拉强度、延伸率,ASTM E8/E8M)
- 硬度(布氏HB、洛氏HRC、维氏HV,ASTM E10/E18)
- 冲击韧性(夏比冲击试验,ASTM E23)
-
- 检测内容:观察显微组织,评估工艺质量。
- 重点项目:
- 晶粒度(ASTM E112)
- 夹杂物评级(ISO 4967)
- 热处理效果(如淬火马氏体形态)
-
- 检测内容:模拟环境下的耐蚀能力。
- 常用方法:
- 盐雾试验(中性/酸性,GB/T 10125)
- 电化学极化曲线(ASTM G5)
- 晶间腐蚀测试(不锈钢,ASTM A262)
-
- 检测内容:检测内部缺陷(裂纹、气孔等)。
- 主流技术:
- 超声波检测(UT,ASTM E317)
- 射线检测(RT,ISO 17636)
- 渗透检测(PT,ASTM E165)
二、覆盖层(涂层/镀层)的检测项目
-
- 检测方法:
- 磁性法(铁基体+非磁性镀层,ISO 2178)
- 涡流法(非导磁基体,ISO 2360)
- 金相显微镜法(ISO 1463)
- 检测方法:
-
- 检测目的:评估覆盖层与基体的结合强度。
- 常用方法:
- 划格法(ISO 2409,适用于薄涂层)
- 拉开法(ASTM D4541,定量测量)
- 弯曲试验(GB/T 5270)
-
- 加速试验:
- CASS试验(铜加速盐雾,ISO 9227)
- 循环腐蚀试验(如Prohesion,ASTM G85)
- 实际暴露试验:户外大气腐蚀(ASTM G50)
- 加速试验:
-
- 适用场景:电镀层、喷涂层的致密性。
- 常用方法:
- 贴滤纸法(ISO 10309,酸性溶液显色)
- 电解法(ASTM B798)
-
- 显微硬度:针对硬质镀层(如镀铬,ASTM E384)
- 摩擦磨损试验:评估涂层耐磨性(ASTM G99)
-
- 检测内容:颜色、光泽、表面缺陷(针孔、气泡)。
- 工具:目视检查、光学显微镜、光泽度仪(ASTM D523)
三、检测标准的选择与趋势
- 标准依据:需结合产品用途(如汽车件参照ISO/TS 16949)、客户要求及行业规范。
- 智能化趋势:自动化检测设备(如AI图像识别缺陷)、在线监测技术(实时涂层厚度控制)的应用日益普及。
四、总结
上一篇:破碎缩分联 合制样设备检测下一篇:电动汽车用锂离子电池模块检测
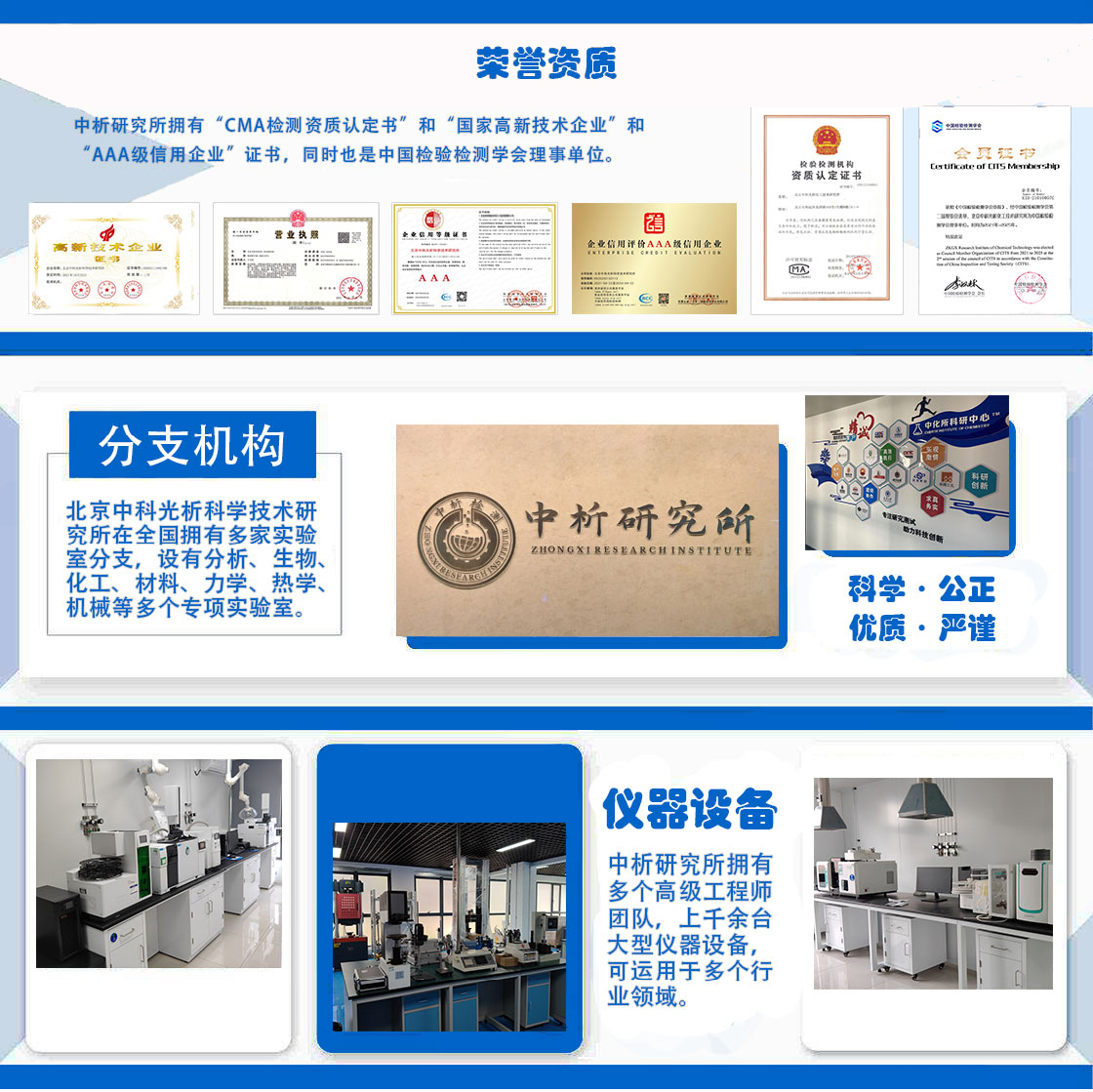
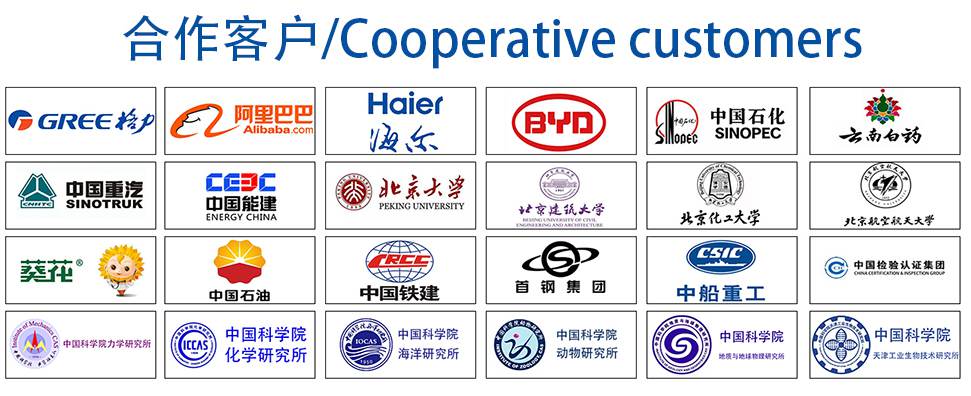
材料实验室
热门检测
276
233
208
217
215
220
230
223
233
233
220
219
222
219
213
210
227
212
224
218
推荐检测
联系电话
400-635-0567