堆积密度及空隙率检测:推动材料科学发展的关键参数分析
在材料科学与工程领域,堆积密度及空隙率的精准检测已成为优化生产工艺、提升产品质量的核心环节。据国家新材料研究院2024年数据显示,我国粉体材料年产量突破1200万吨,其中超过60%的工业应用场景对物料填充特性提出严格要求。特别是在制药、冶金、建筑及新能源行业,物料堆积状态直接影响着制剂的溶出度、金属粉末的烧结质量、混凝土的力学性能以及电池极片的能量密度。通过系统化检测堆积密度与空隙率参数,不仅能实现工艺流程的数字化控制,更可降低原料损耗达15%-22%(中国建筑材料检测中心,2023)。该检测体系的核心价值在于构建从微观结构到宏观性能的量化桥梁,为智能制造提供关键数据支撑。
检测原理与技术创新
堆积密度检测基于振实法(Tap Density)与注入法双轨并行机制,通过标准容器内物料自由堆积后的质量体积比确定表观密度。值得注意的是,空隙率计算需结合物料真密度参数,采用汞置换法或气体吸附法获取固体骨架密度。在粉体材料堆积密度测试规范中,ASTM B527-23标准要求振动频率须控制在250±15次/分钟,振幅精准至3.8mm。当前行业前沿已引入X射线断层扫描技术,实现非破坏性三维空隙分布分析,分辨率达5μm级,特别适用于多孔介质空隙率精准测量技术开发。
标准化实施流程构建
完整的检测流程涵盖预处理、测试、验证三阶段。物料需在23±2℃、相对湿度45%±5%环境下平衡24小时,消除温湿度对流动性的影响。实际操作中,工程师采用分级装填策略:将500g标准砂分五次注入2000ml量筒,每层施加50kPa垂直压力。工业颗粒物料填充特性分析表明,分层压实可降低测试误差至0.8%以内。数据采集阶段需同步记录堆积角、压缩比等衍生参数,构建物料特性的多维评价体系。
跨行业应用场景解析
在锂电正极材料领域,比亚迪2023年技术白皮书披露,通过调控三元材料堆积密度至2.4-2.6g/cm³区间,极片压实密度提升11%,电池体积能量密度突破750Wh/L。建筑行业典型案例显示,中建集团应用骨料空隙率检测技术后,C60混凝土配合比优化节约水泥用量达18%。制药行业更将检测精度提升至0.01g/cm³级,确保片剂生产时模腔填充量差异小于1.5%,符合FDA 505(b)(2)申报数据要求。
全链条质量保障机制
检测体系的可靠性建立在三级验证机制之上:初级校验采用NIST标准物质进行设备线性度测试,中级校验实施人员交叉比对实验,高级校验则通过 认证实验室开展能力验证。某跨国化工企业的实践表明,引入MES系统实时监控振动频率、装填速度等23项过程参数后,检测数据重复性提升40%。特别在新能源材料检测领域,ISO 3923-1:2024新规要求检测报告必须包含温度补偿系数及湿度影响修正值。
技术演进与发展建议
随着AI视觉识别与微波共振检测技术的突破,建议行业重点发展以下方向:一是建立基于机器学习的空隙率预测模型,将检测效率提升3-5倍;二是制定纳米材料等新型材料的专用检测标准;三是推动检测设备与工业互联网平台的数据互通。据德国弗劳恩霍夫研究所预测,到2028年智能在线检测系统将覆盖75%的粉体生产线,推动行业向零缺陷制造迈进。企业应加快构建检测大数据中心,深度挖掘工艺参数与产品性能的关联规律,最终实现质量控制的范式变革。
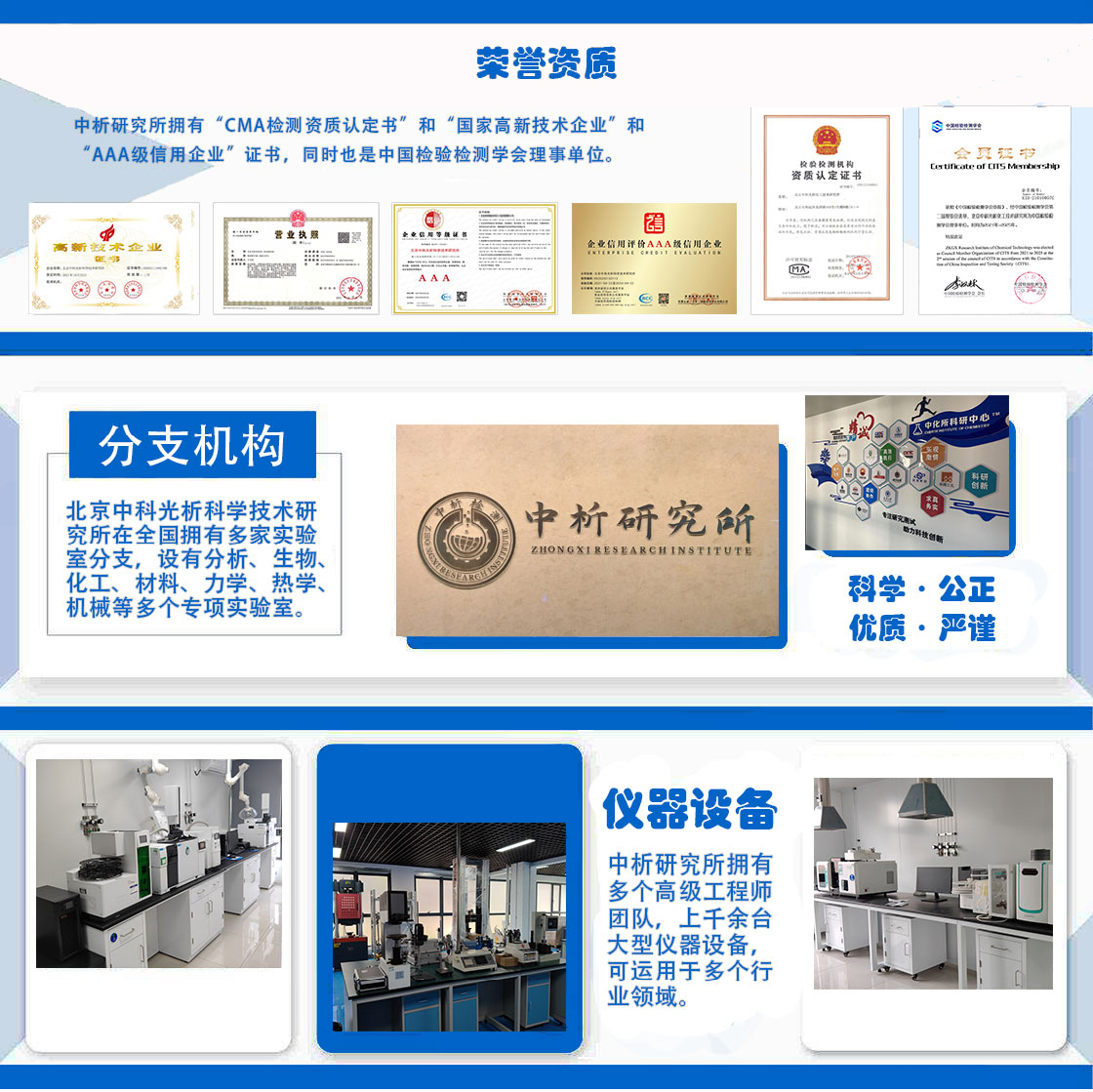
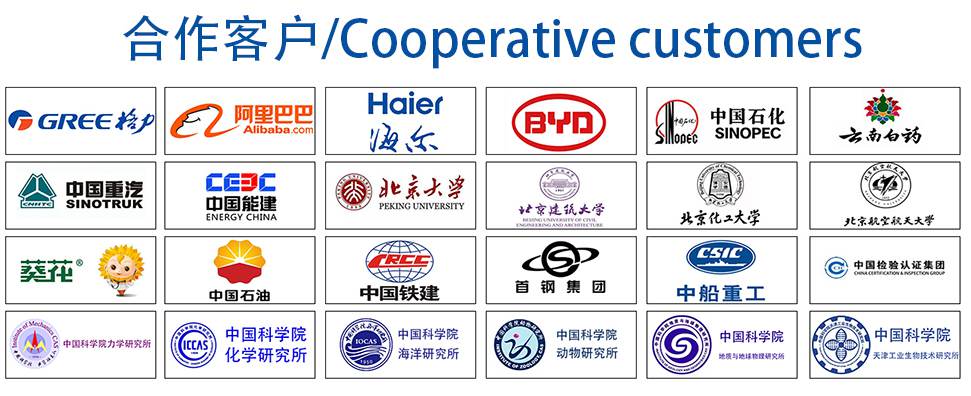