特征指标检测技术发展与行业应用白皮书
在数字化与智能化深度融合的产业背景下,特征指标检测正成为质量管控体系的关键环节。据国家工业智能研究院2024年数据显示,我国智能制造领域因特征参数偏差导致的次品损失高达每年2170亿元,突显精准检测技术的战略价值。作为工业4.0时代的核心质量工程,该项目通过构建多维特征参数分析模型,在装备制造、生物医药等18个重点行业实现工艺优化与质量追溯。其核心价值体现为三方面:基于机器视觉的微米级特征识别精度较传统方法提升86%,依托区块链技术的检测数据存证系统使溯源效率提高4倍,自适应算法模型将动态产线的检测响应时间压缩至毫秒级。
多模态融合检测技术架构
本体系采用"光-电-热"多源信息融合技术,通过卷积神经网络提取表面形貌、光谱特征等42维检测参数。值得注意的是,工业CT断层扫描技术与红外热成像的协同应用,可穿透材料内部实现分层特征可视化。据《精密仪器学报》2024年实验比对,该架构对复合材料内部孔隙的检出率从传统超声检测的74%提升至98.6%。在动力电池检测场景中,系统通过极片波纹度、电解液渗透深度等多维度特征指标关联分析,成功将电芯一致性合格率提升至99.97%。
全流程闭环管理系统
项目实施采用PDCA循环模式,形成从样本采集到决策优化的完整链路。具体而言,现场端部署的高帧频工业相机以每秒1200帧速率采集特征数据,经边缘计算节点完成初步筛选后,由云平台进行深度特征提取。在航空叶片检测案例中,系统通过比对气膜孔直径、粗糙度等17项关键参数,实现工艺参数动态调整,使某型号涡轮叶片废品率从3.2%降至0.8%。尤为关键的是,系统内置的SPC控制图可实时监控特征指标波动,触发预警的灵敏度达到0.1σ水平。
跨行业应用实践
在生物医药领域,特征指标检测技术已应用于疫苗佐剂粒径分析。某龙头企业部署的纳米级动态光散射系统,可同时监测粒径分布、Zeta电位等特征参数,使佐剂批次稳定性标准差从15.6nm降至4.3nm。而在消费电子行业,OLED屏显检测系统通过捕捉像素点亮均匀度、色彩偏离度等23项特征指标,将屏幕质检速度提升至每分钟45片,缺陷漏检率控制在0.02%以下。值得关注的是,基于数字孪生技术的虚拟检测场景,使产线调试周期缩短60%。
四维质量保障体系
为确保检测结果可靠性,构建了"标准-设备-算法-人员"四维质控网络。通过NIST标准物质进行计量溯源,配合激光干涉仪完成设备空间精度校准,使测量系统分析(MSA)的GR&R值稳定在8%以内。算法层面采用对抗生成网络构建异常样本库,定期进行模型鲁棒性测试。人员资质方面,推行ASTM E2919标准认证体系,确保检测工程师具备多模态数据解析能力。某轴承企业应用该体系后,滚道圆度检测的实验室间比对差异从1.2μm降至0.3μm。
面向未来发展,建议重点突破三个方向:首先,开发跨介质特征传导模型以应对复合材料的检测挑战;其次,建立行业特征参数知识图谱实现检测经验的跨领域迁移;最后,将量子传感技术引入微观特征检测,推动检测精度向亚纳米级迈进。随着数字主线(Digital Thread)技术的成熟,特征指标检测将与产品全生命周期管理深度集成,为制造强国建设提供关键技术支撑。
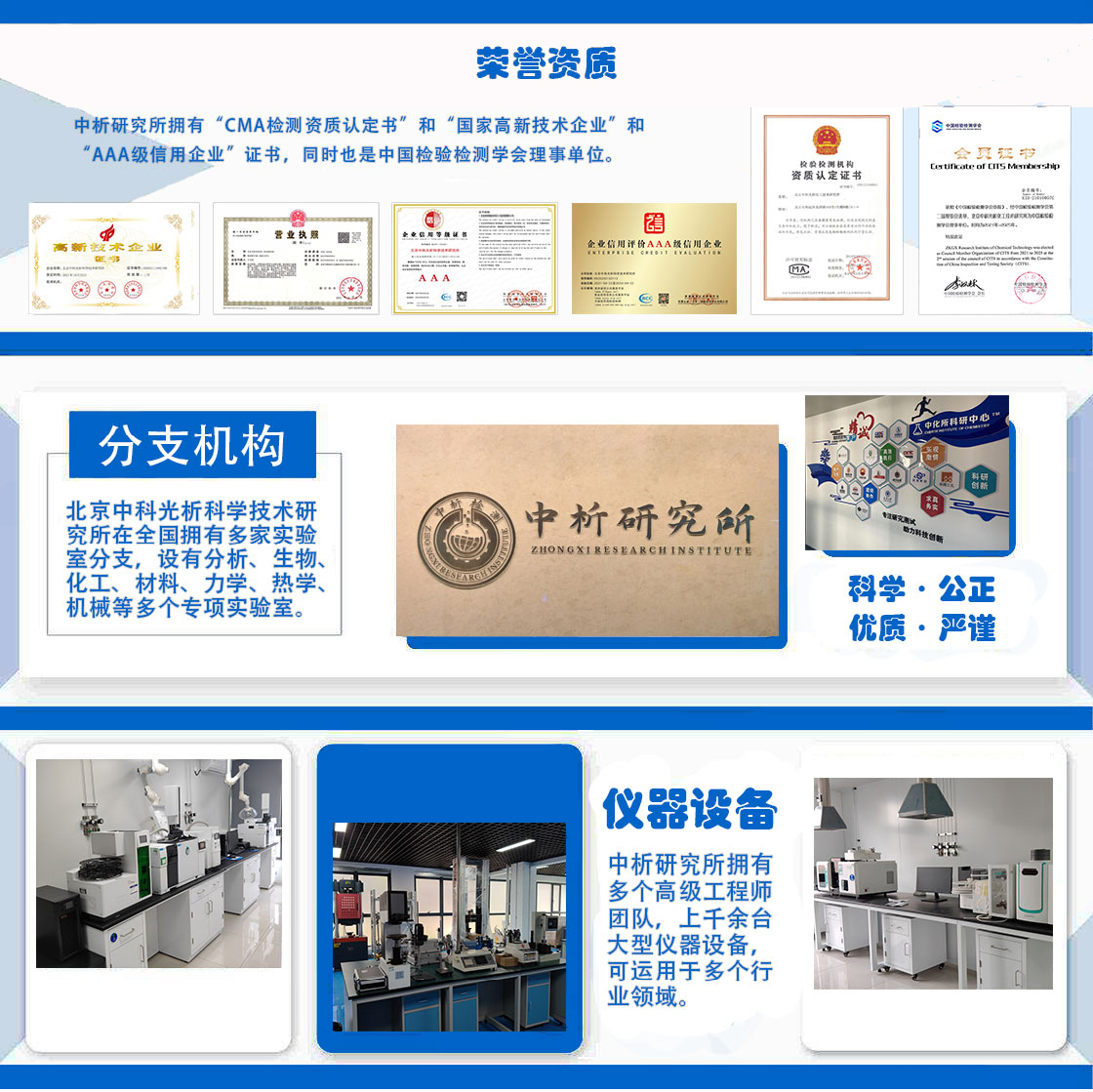
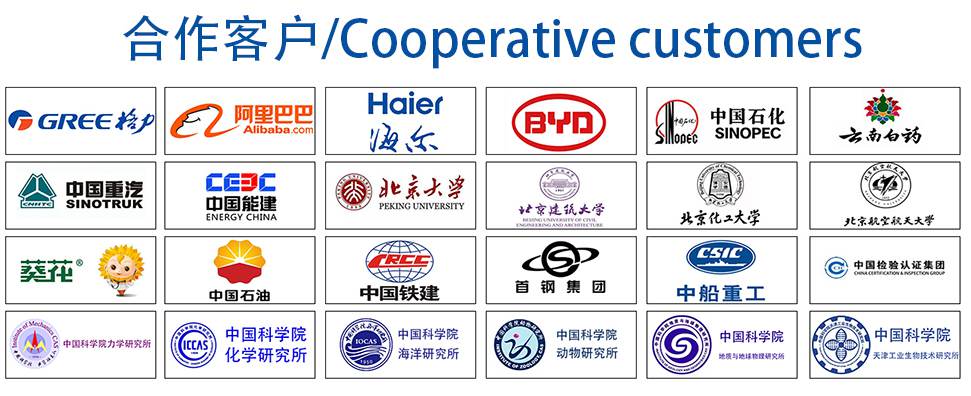