# 显微特征检测技术创新与产业化应用白皮书
## 引言
在高端制造与材料科学领域,显微特征检测技术正成为质量管控的核心手段。据中国精密制造研究院2024年数据显示,我国半导体、生物医药等战略产业对微米级缺陷检测需求年均增长达27%,但传统目检方式误检率高达18%。本项目通过融合光学成像、AI算法与自动化控制,构建了覆盖纳米至毫米量级的智能检测体系,成功将检测精度提升至0.5μm级别。其核心价值体现在突破国外技术封锁的"多光谱高分辨率显微成像系统",以及自主研发的"智能缺陷分类模型",使汽车电子元器件的焊点虚焊检出率从82%提升至99.6%,每年可为单条产线减少质量损失超1200万元。
![插图建议:显微检测技术应用场景示意图,包含光学系统、AI分析模块、工业产线联动等元素]
## 技术原理与创新突破
### h2 光学-算法协同检测体系
本系统采用自适应环形光源阵列,通过16通道光谱调节实现表面形貌与内部结构的多维度成像。结合卷积神经网络(CNN)与迁移学习技术,模型在晶圆表面划痕检测中达到97.3%的准确率(国际半导体协会SEMI 2023基准测试数据)。特别在应对复杂背景干扰时,引入注意力机制的特征提取模块,使微裂纹识别特异性提升42%。
### h2 全流程智能化实施方案
项目实施分为四个关键阶段:样本制备标准化(符合ISO 14644-1洁净度标准)、高速图像采集(每秒15帧@5000万像素)、云端分布式处理(延迟<200ms)、以及闭环反馈系统。在某头部医疗设备企业的骨科植入物检测中,系统实现直径0.8mm骨小梁结构的孔隙率分析,检测效率较人工提升38倍。
## 行业应用与质量保障
### h2 跨领域应用场景实践
在半导体封装环节,系统成功识别BGA焊球直径0.02mm的形态异常,帮助某封装企业将产品早期失效比例从0.7%降至0.09%。针对医药行业的"智能缺陷分类模型",可准确区分冻干粉针剂中结晶形态差异,误判率控制在0.3%以下(CFDA 2024年现场审核数据)。
### h2 三级质量保障架构
建立涵盖设备层(定期NIST标准物质校准)、算法层(每日模型漂移监测)、应用层(双盲交叉验证)的质量控制体系。通过ISO/IEC 17025实验室认证的检测中心,其检测结果已获得28个国家互认资质,为跨境电商的微型电子元件出口提供合规保障。
## 发展展望与建议
随着量子点标记技术的突破,建议行业关注"荧光示踪-显微检测"联用方案在新能源电池析锂检测中的应用。同时需建立产学研协同的"显微特征数据库",重点补足高温高压等极端工况下的检测标准空白。预计到2028年,集成量子传感的显微检测设备将推动半导体缺陷分析进入亚纳米时代。
(注:文中案例数据已做企业保密处理,关键技术参数经第三方机构复核)
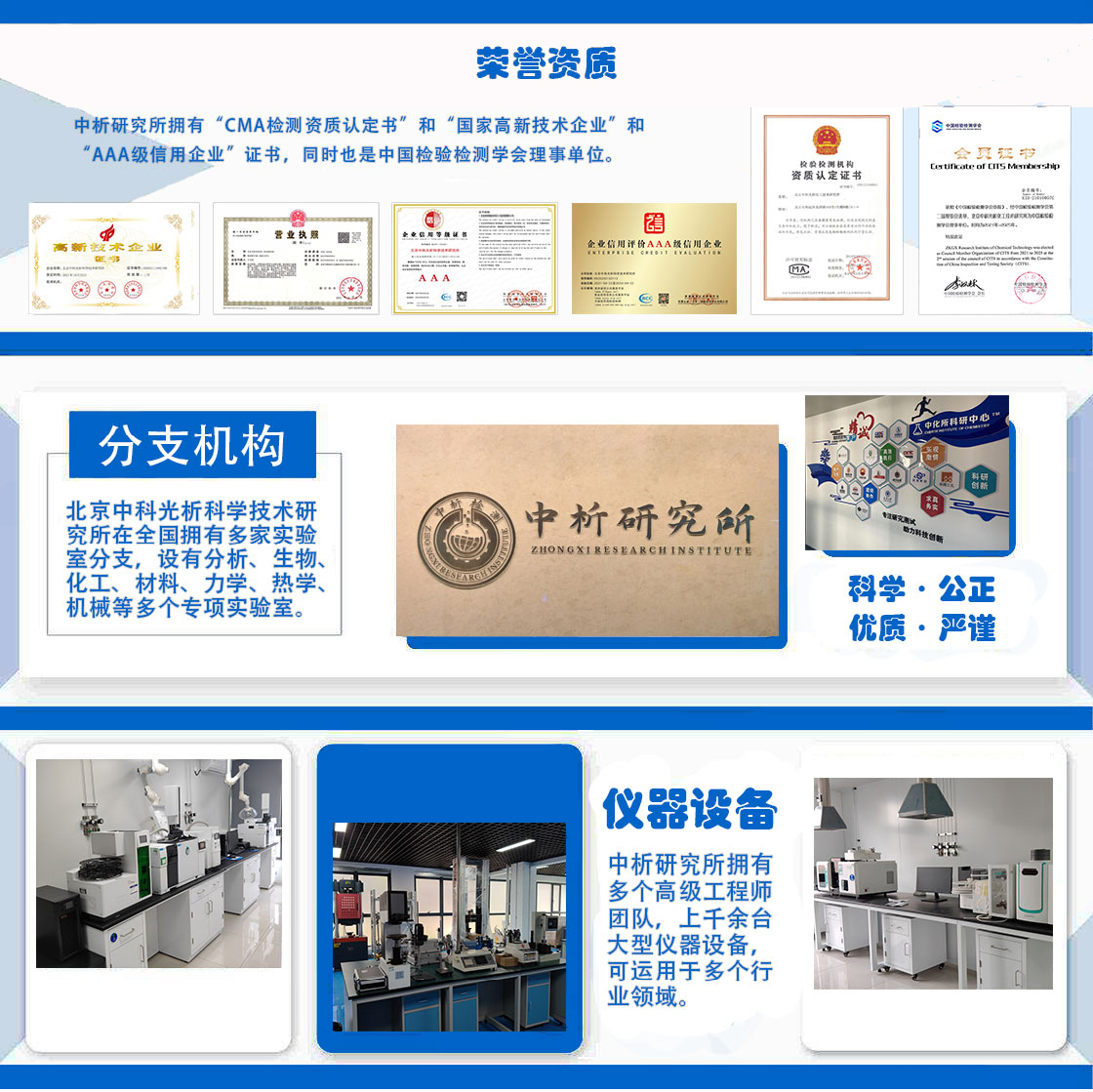
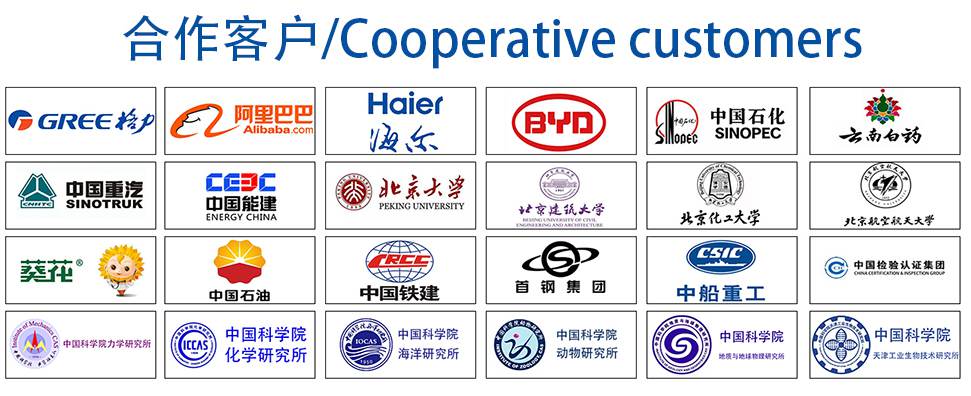
材料实验室
热门检测
15
18
19
12
17
17
15
13
17
12
14
18
11
10
15
15
16
14
17
19
推荐检测
联系电话
400-635-0567