一、航空机轮检测的必要性
- 轮胎爆裂:因老化、异物刺穿或胎压异常导致;
- 轮毂裂纹:金属疲劳或腐蚀引发结构性失效;
- 刹车系统故障:制动效率下降或热衰退引发安全隐患。
二、核心检测项目与技术要求
1. 轮胎检测
-
- 标准:胎纹深度≥1.6mm(FAA Part 25.733),无可见帘线层暴露;
- 方法:使用深度规测量,目视检查割伤、鼓包、异物嵌入(如金属屑);
- 案例:2020年某航司因未检出轮胎侧壁3cm割伤,导致起飞时爆胎。
-
- 标准:冷胎压力误差≤±5%(参照机型手册,如B737NG为200-220psi);
- 操作:使用数字压力计每日航前检测,环境温度补偿校准。
-
- 要求:动平衡偏差≤30g·cm(需使用专用平衡机检测);
- 处理:通过配重块调整,避免高速滑行时振动超标。
2. 轮毂检测
-
- 区域:重点检查轮缘螺栓孔、气门嘴座、刹车盘安装面;
- 缺陷判定:裂纹长度>1.5mm或腐蚀深度>壁厚10%需更换;
- 技术:使用荧光渗透剂(FPI)或磁粉检测(MT)提高微裂纹检出率。
-
- 项目:轮毂内径椭圆度≤0.1mm,法兰盘平面度<0.05mm;
- 工具:三坐标测量仪(CMM)或激光扫描设备。
3. 刹车系统检测
-
- 标准:碳刹车片剩余厚度≥制造商报废限值(如Honeywell规定最小3.2mm);
- 检测:超声波测厚仪多点测量,避免热斑导致的厚度不均。
-
- 氧化层检查:刹车盘表面蓝紫色氧化区域面积>30%需更换;
- 微裂纹检测:涡流检测(ET)识别亚表面裂纹。
-
- 压力测试:刹车作动筒密封性需在3000psi下保压5分钟无泄漏;
- 响应时间:从踏板输入到最大制动力生成时间<2秒(空客A320标准)。
4. 轴承与密封组件
-
- 轴向游隙:使用千分表测量,范围0.02-0.08mm(波音787标准);
- 润滑状态:检查油脂污染度(颗粒物尺寸>25μm需清洗更换)。
-
- 泄漏测试:充气至1.5倍工作压力,保压10分钟压降<5%;
- 老化评估:橡胶硬度变化(邵氏A)超过±10点需更换。
5. 辅助系统检测
-
- 校准:传感器信号与机械表读数偏差<±2%;
- 线路检查:高频振动环境下线缆绝缘层破损防护。
-
- 功能测试:模拟湿跑道条件下ABS触发频率与刹车力调制曲线;
- 传感器校准:轮速信号误差<0.5%。
三、检测周期与齐全技术应用
-
- 航线检测:每飞行循环(Flight Cycle)目视检查轮胎与刹车;
- 深度检测:每300-500次起落执行轮毂渗透检测及轴承分解检查。
-
- 红外热成像:实时监控刹车温度分布,识别局部过热区域;
- 3D数字孪生:通过扫描数据比对历史模型,预测剩余寿命;
- 声发射监测:捕捉轮毂裂纹扩展时的应力波信号。
四、维修决策与安全管理
-
- A类缺陷(如贯穿性裂纹):立即停飞更换;
- B类缺陷(如轻微腐蚀):记录跟踪并在下一级定检处理。
五、
- FAA AC 43.13-1B - Acceptable Methods for Aircraft Repair and Maintenance
- Airbus AMM (Aircraft Maintenance Manual) - Wheels and Brakes Chapter
- SAE AIR5793 - Aircraft Wheel and Brake Maintenance Best Practices
转成精致网页
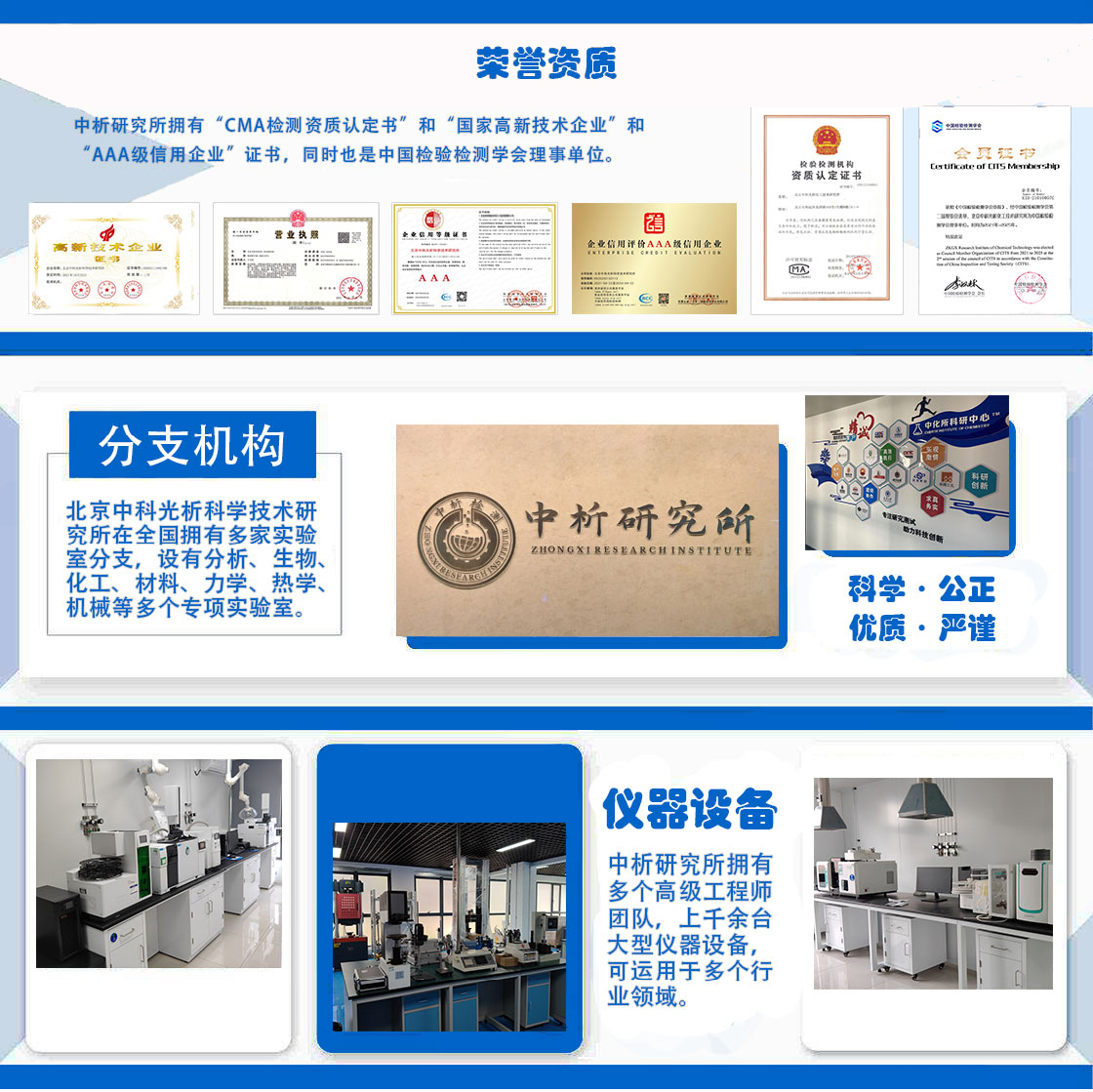
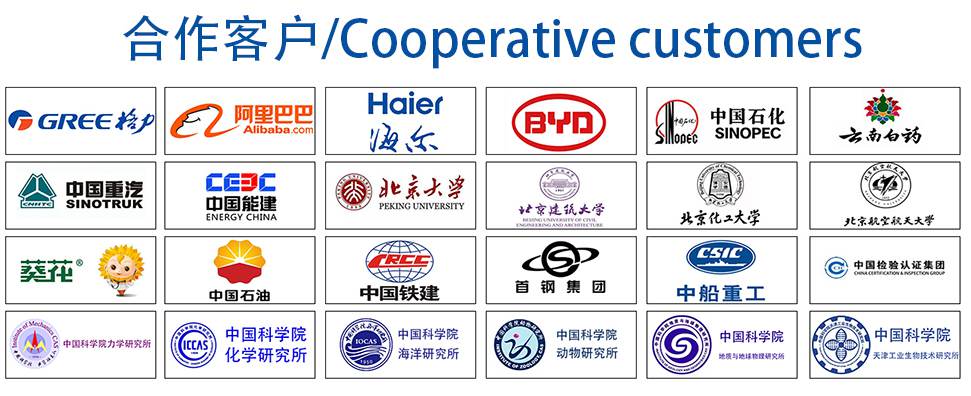
材料实验室
热门检测
推荐检测
联系电话
400-635-0567