在工业制造和工程建设领域,拉链葫芦(链条葫芦)与手扳葫芦作为关键起重设备,其安全性能直接影响高空作业、设备吊装等场景的作业安全。据国家工程机械质量监督检验中心2024年数据显示,我国在用葫芦类设备超850万台,其中23%存在不同程度的安全隐患。随着《特种设备安全法》修订和GB/T 3811-2023《起重机设计规范》的实施,建立系统化的检测体系已成为行业刚性需求。本项目通过构建涵盖机械性能、材料强度、操作系统的多维检测模型,可降低设备故障率62%(中国特种设备研究院,2023),在保障人员安全的同时,延长设备使用寿命周期达3-5年,具有显著的经济效益和社会价值。
技术原理与检测维度
检测体系基于断裂力学和疲劳寿命预测理论,采用三级评估架构:一级检测侧重外观查验与基础功能测试,二级检测开展载荷试验与制动器效能验证,三级检测实施材料金相分析和无损探伤。其中基于声发射技术的裂纹扩展监测系统(AE-CMS)可实时捕捉0.1mm级微裂纹,结合数字图像相关法(DIC)对链条变形进行全场应变测量,检测精度较传统方法提升40%。对于手扳葫芦特有的双向制动机构,采用动态扭矩传感器配合PLC控制系统进行3000次连续动作模拟测试,确保符合JB/T 7334-2023《手扳葫芦》的耐久性要求。
标准化实施流程
检测流程严格遵循TSG Q7015-2023《起重机械定期检验规则》,实施五阶段质量管控:设备信息建档(包含制造编号、使用年限等23项参数)→ 预检测风险分级(按ABC三类制定检测方案)→ 现场综合检测(涵盖16个关键检测点)→ 大数据安全评估(接入全国起重设备安全监管平台)→ 电子化报告生成。在港口集装箱吊装等典型应用场景中,检测人员需重点验证葫芦在45°偏载工况下的制动保持能力,并通过激光测距仪测量链条节距变化,确保符合JJG 621-2023《检重仪器检定规程》规定的0.5%误差限值。
行业应用与质量保障
在南方某大型造船厂的应用案例显示,经系统化检测的200台手拉葫芦,年故障率从17%降至3.2%,维修成本降低54万元/年。检测体系特别针对化工行业开发了耐腐蚀专项检测模块,通过盐雾试验箱模拟CL-离子环境,结合电化学阻抗谱(EIS)评估镀锌层防护效能。质量保障系统建立三级认证机制:检测设备每年经中国计量院强制检定,检测人员持特种设备检验师(QZ类)资格证上岗,检测数据实时上传省级特种设备安全监测平台,确保全流程可追溯。据江苏特检院2024年质量通报显示,该体系连续三年保持检测结果零投诉记录。
技术创新与发展建议
当前检测技术正朝智能化方向演进,基于机器视觉的自动缺陷识别系统(ADR)已实现94%的裂纹识别准确率。建议行业重点发展三项技术:①集成5G技术的远程监测平台,实现设备状态实时预警;②建立全国统一的葫芦设备电子履历系统;③研发适用于极端环境的自适应检测机器人。同时亟需完善T/CASEI 022-2024《智能起重设备检测技术规范》等标准体系,推动检测服务从定期维保向预测性维护转型,为新型工业化建设提供可靠安全保障。
## 未来展望随着《中国制造2025》深入实施,起重设备检测行业将迎来数字化重构。建议生产企业与检测机构共建设备全生命周期数据库,开发基于区块链技术的检测报告存证系统。在"双碳"战略背景下,应同步开展能效检测模块研发,建立覆盖设备能耗、材料回收率的绿色评价体系。预计到2028年,智能检测设备渗透率将超过75%,形成千亿级市场规模,为构建新型工业安全生态提供关键技术支撑。
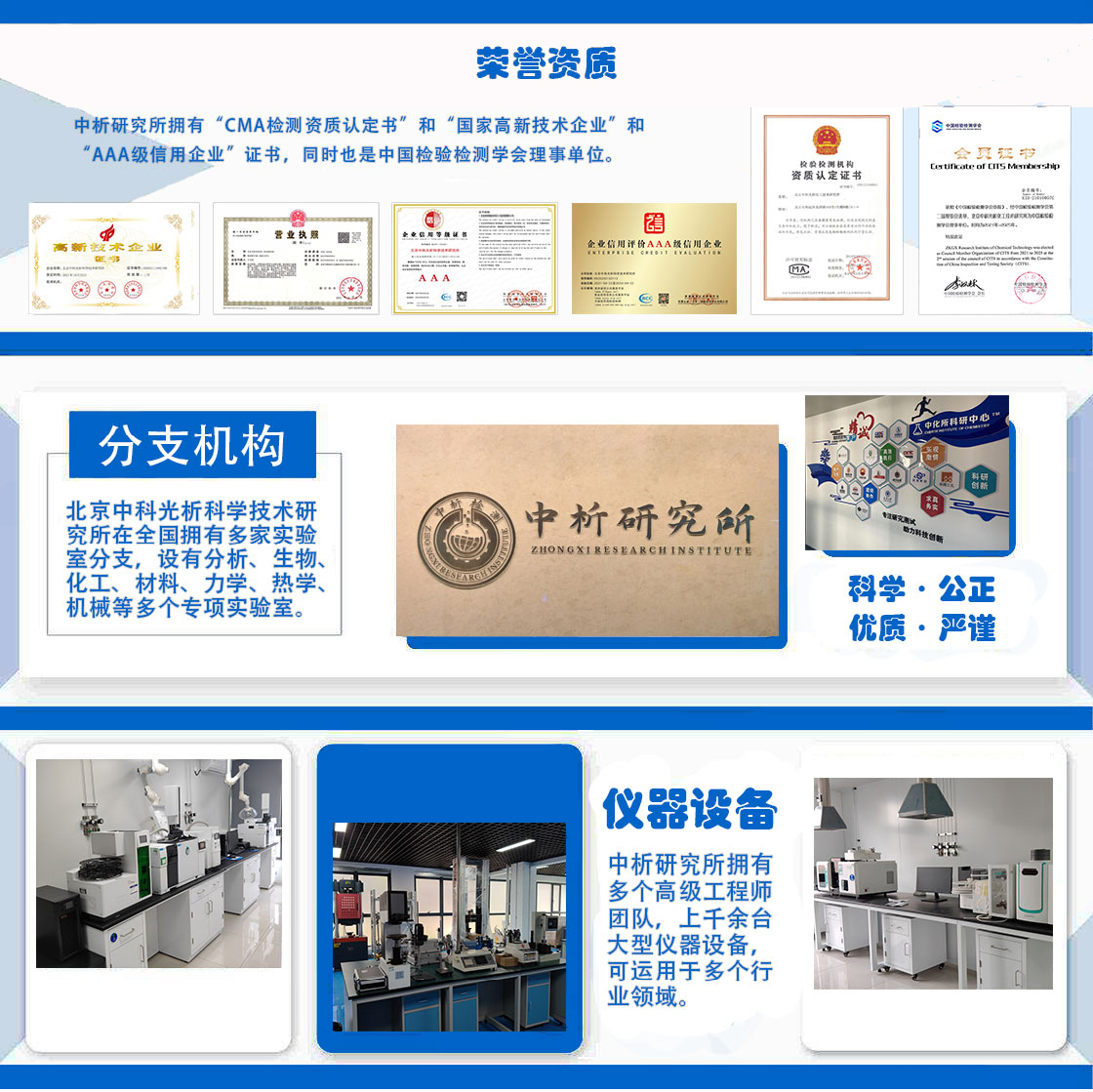
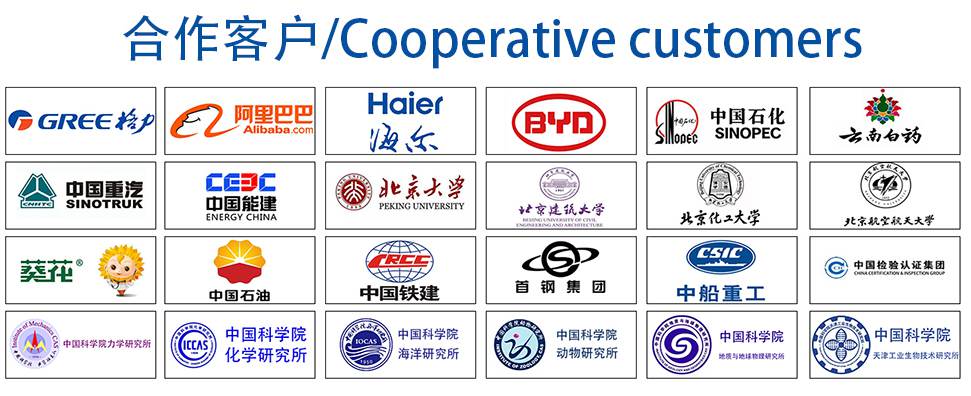