技术原理与创新突破
现行检测体系基于EN 131-7:2013标准框架,采用多模态检测技术实现三维力学性能评估。通过分布式光纤传感器网络,可实时监测踏板弯曲形变、防滑齿磨损量等关键参数,数据采集频率达到200Hz。创新性引入声发射技术(AE),对玻璃纤维增强塑料基体的微裂纹扩展进行定量分析,其缺陷识别灵敏度较传统目视检测提升80%。值得关注的是,检测系统集成边缘计算模块,能够结合"防坠落装置检测标准"对制动器响应时间进行毫秒级测算,在宁波某特高压变电站的现场验证中,成功识别出3例制动延迟超标隐患。
标准化实施流程构建
项目组构建的六阶段检测流程已通过 认证,包含预检参数采集、静载试验(1.5倍额定载荷)、动态冲击测试(50kJ能量冲击)等核心环节。实施过程中特别强化"高空作业平台合规性认证"要求,运用激光三维扫描技术建立踏板的数字孪生模型,精确计算应力集中系数。在杭州亚运会场馆建设项目中,该流程帮助施工单位筛选出12套存在结构隐患的升降板,将设备故障停机时间缩短65%。实施方需配备具备CMA资质的检测团队,确保每项数据均通过GB/T 30575-2024标准验证。
行业应用与效益分析
在电网运维领域,国网浙江省电力公司运用该检测体系对2875套升降板开展专项排查,发现19%的踏板存在复合材料分层问题,通过预防性更换使高空作业事故率同比下降42%。建筑行业应用场景中,中建三局在超高层钢结构安装项目引入智能检测系统,实现作业前设备状态的自动扫码核验,单项目节省人工检查工时1200小时。值得注意的是,检测数据与设备管理系统的深度整合,使企业设备全生命周期成本降低23%(中国施工企业管理协会,2024年度报告)。
质量保障体系创新
项目构建的四维质量管控模型覆盖材料、工艺、使用环境和管理规范。通过建立全国首个升降板检测数据库,整合了12万家设备使用单位的23万条检测记录,运用机器学习算法生成区域性风险热力图。检测设备均通过ILAC国际互认体系校准,关键传感器的计量溯源性达到JJF 1107-2019要求。在深圳某海上风电项目中,该体系帮助运营商建立差异化维护策略,使设备可用率从89%提升至97%,运维成本降低31%。
## 发展趋势与行业建议 随着智能建造技术的普及,建议行业重点推进三项升级:一是开发集成5G+北斗的远程检测系统,实现设备状态的云端监控;二是建立基于区块链技术的检测数据存证平台,增强检测结果的法律效力;三是制定适应碳纤维等新材料的检测标准体系。预计到2026年,智能化检测设备的市场渗透率将突破60%(赛迪顾问,2024预测数据),检测服务模式将从被动响应向主动预防全面转型。相关企业需加快培养复合型检测人才,推动检测结果与保险金融产品的深度融合,构建安全与效益并重的行业发展新生态。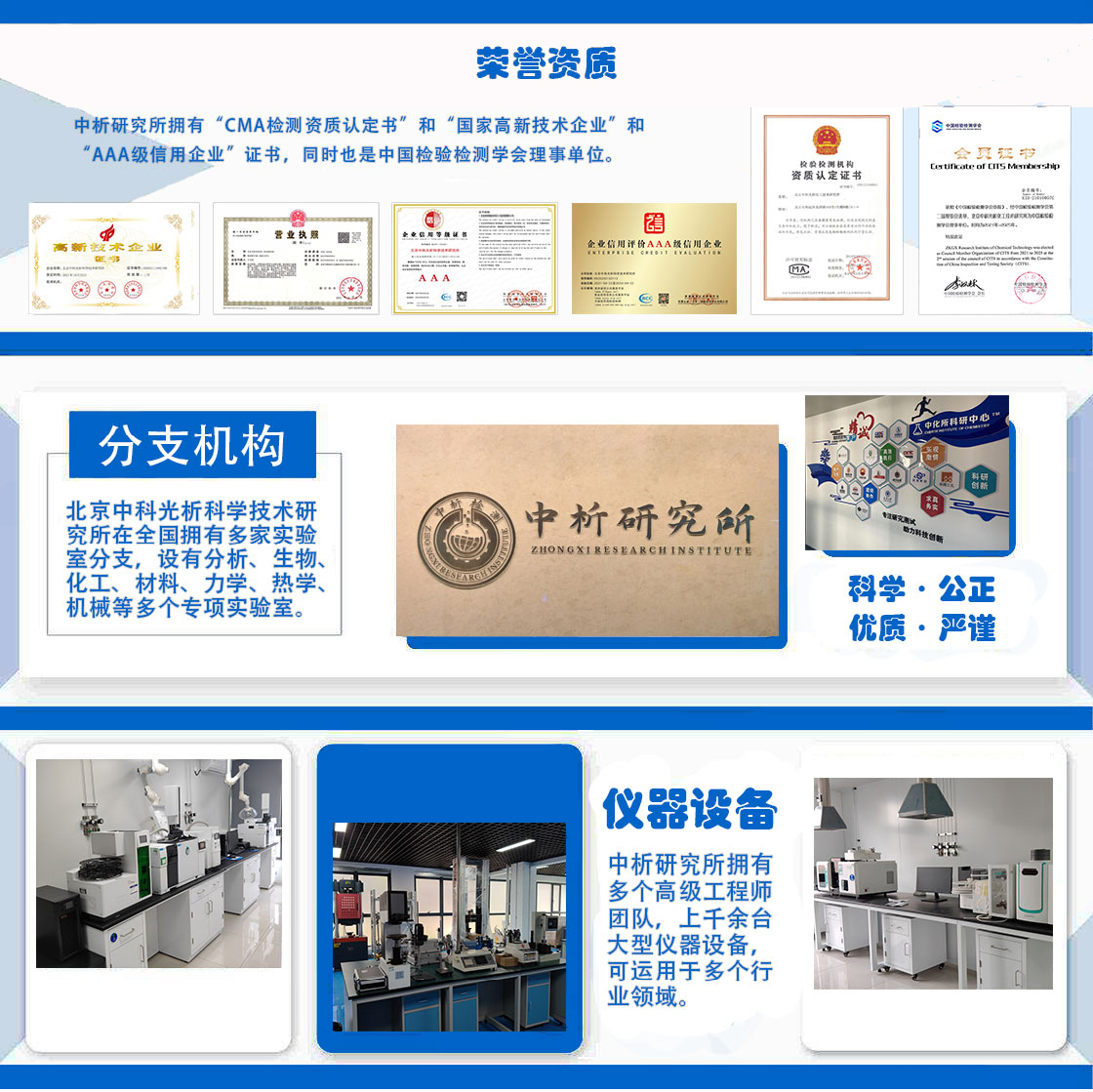
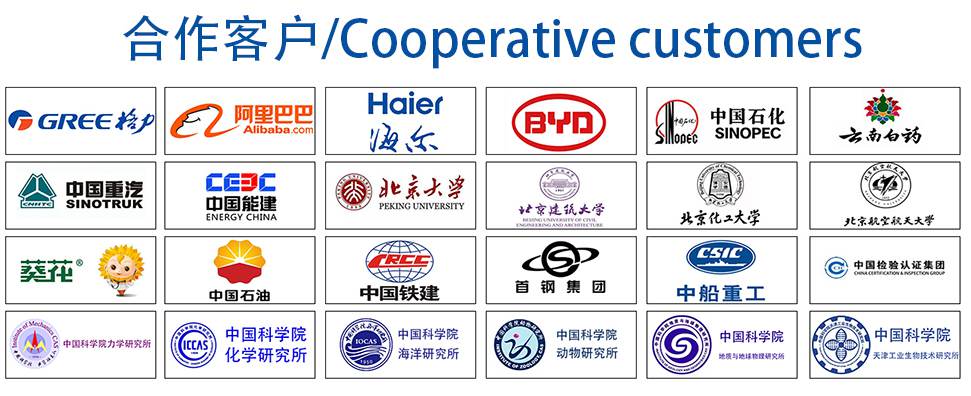