耳片厚度检测:关键检测项目与技术解析
一、耳片概述
二、耳片厚度检测的意义
- 确保结构强度:厚度不足会导致耳片变形或断裂。
- 预防疲劳失效:厚度不均可能引发应力集中,加速疲劳损伤。
- 满足装配精度:厚度偏差影响配合间隙,导致装配失效或松动。
三、核心检测项目
1. 尺寸参数检测
- 耳片厚度:垂直于耳片轴线方向的多点测量,确保符合公差(通常±0.1 mm以内)。
- 孔径与圆度:检测安装孔直径及形状误差,避免因孔变形导致应力集中。
- 对称性:检查两侧耳片厚度对称度,防止偏载。
- 倒角与过渡区:验证圆角半径和过渡区平滑度,减少局部应力。
2. 表面缺陷检测
- 裂纹与划痕:使用渗透检测(PT)或磁粉检测(MT)定位表面微裂纹。
- 腐蚀与磨损:评估表面氧化、点蚀深度对有效厚度的削弱。
- 加工缺陷:检查毛刺、刀痕等可能引发疲劳断裂的隐患。
3. 材料性能验证
- 材质一致性:通过光谱分析确认材料牌号(如航空用TC4钛合金或30CrMnSiA钢)。
- 硬度测试:布氏或洛氏硬度检测,间接评估材料强度与热处理效果。
4. 安装配合检测
- 配合间隙:模拟装配状态,测量耳片与连接件的间隙均匀性。
- 接触面贴合度:使用蓝丹或三维扫描检查接触面积占比(需≥85%)。
5. 动态性能测试(可选)
- 疲劳试验:通过循环加载检测厚度变化对疲劳寿命的影响。
- 负载形变分析:在额定载荷下测量耳片的弹性变形量。
四、检测方法与设备
检测项目 | 常用方法 | 设备示例 |
---|---|---|
厚度测量 | 数显游标卡尺、激光测厚仪 | Mitutoyo 530-122 |
孔径检测 | 气动量仪、三坐标测量机(CMM) | Zeiss CONTURA G2 |
表面缺陷 | 荧光渗透检测、工业内窥镜 | Magnaflux ZL-67 |
材料成分 | 直读光谱仪(OES) | ARL 3460 |
动态性能 | 伺服液压疲劳试验机 | Instron 8801 |
五、检测标准与规范
- 国家标准:GB/T 11345(焊缝无损检测)、GB/T 5779(紧固件表面缺陷)。
- 行业标准:HB 7681(航空耳片技术条件)、ISO 12107(金属材料疲劳试验)。
- 企业标准:根据具体工况制定更严格的内部验收准则。
六、检测流程优化建议
- 预处理:清洁耳片表面油污,确保测量基准面平整。
- 多位置测量:在耳片根部、中部、边缘选取至少5个测量点。
- 数据对比:将实测值与设计图纸、历史数据进行趋势分析。
- 自动化升级:采用机器视觉或激光扫描实现批量检测(效率提升40%以上)。
七、典型案例分析
八、挑战与对策
- 复杂结构检测:异形耳片可使用柔性三坐标探头或CT扫描重建三维模型。
- 环境干扰:高温/油污环境下优先选用激光非接触式测量。
- 数据管理:建立MES系统实现检测数据可追溯性。
九、
上一篇:空粒率检测下一篇:缺陷粒、异常果、不完善粒、损伤粒率、破损率检测
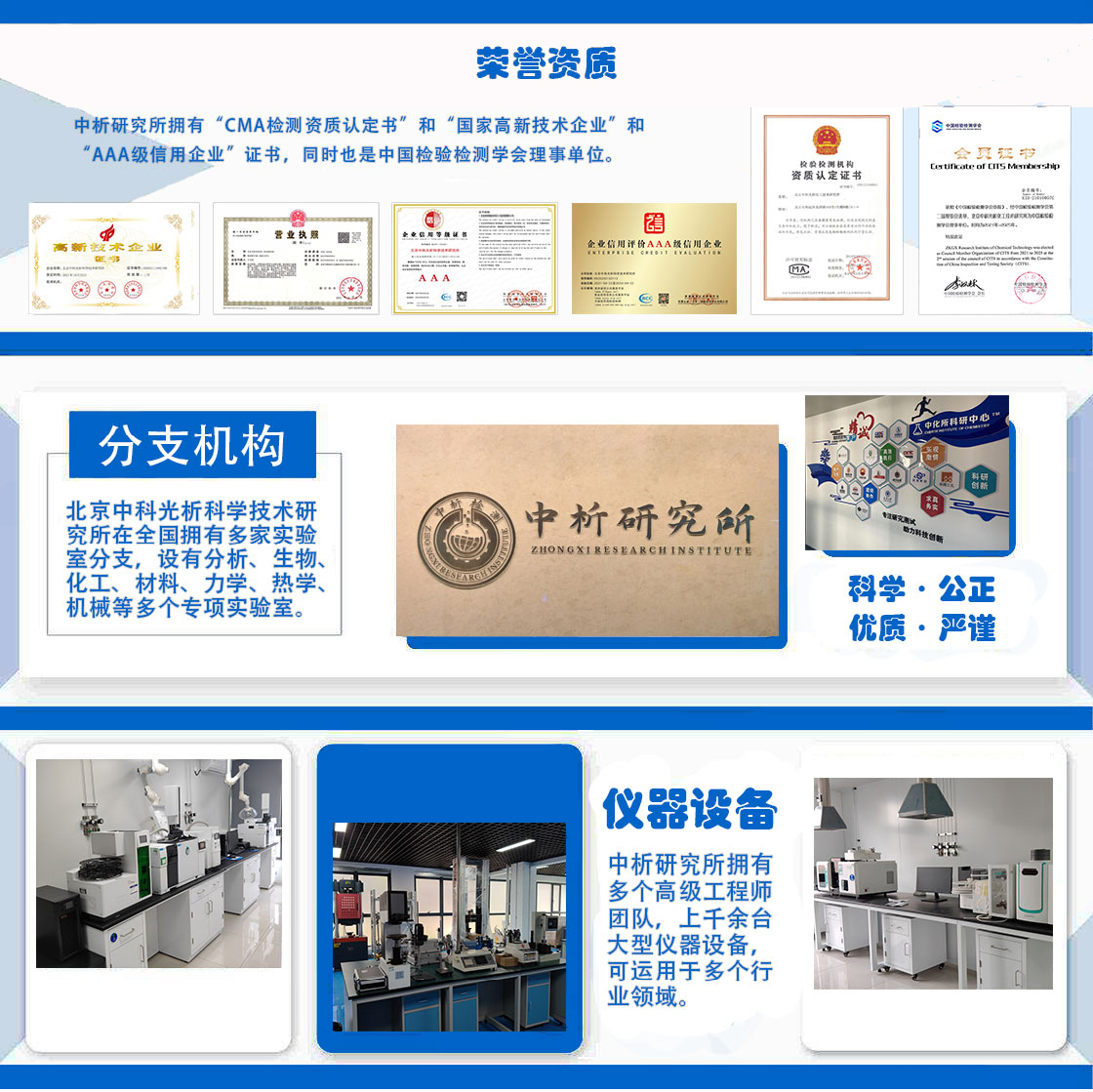
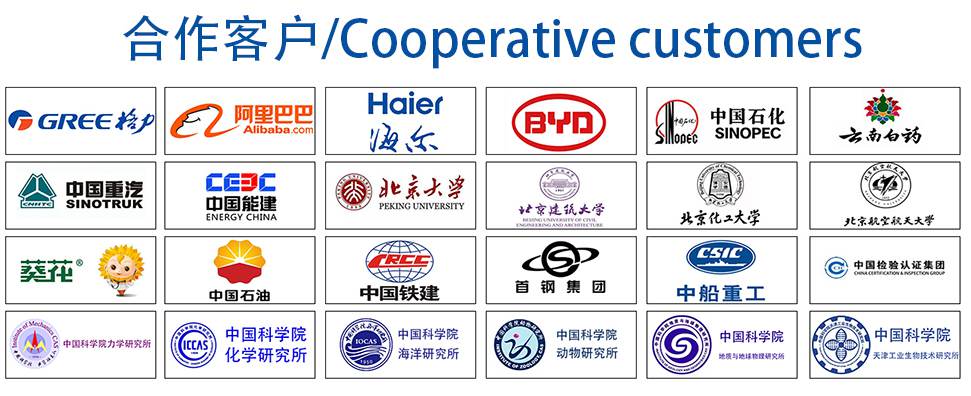
材料实验室
热门检测
12
13
17
18
23
19
18
19
21
24
24
26
23
23
25
28
23
24
25
21
推荐检测
联系电话
400-635-0567