石油天然气工业用钢丝绳检测项目解析
在石油天然气行业中,钢丝绳作为关键承载部件,广泛应用于钻井平台、起重设备、缆绳系统和海底作业场景。其性能直接影响工程安全与设备可靠性。由于长期处于高压、腐蚀、高载荷等极端环境,钢丝绳的疲劳、磨损、断裂风险显著增加。因此,定期开展系统性检测是保障生产安全的核心环节,需覆盖结构完整性、力学性能及环境适应性等多维度指标。
核心检测项目分类
1. 结构参数检测
包括钢丝绳直径、捻距、股数、绳芯类型等基础参数的测量,确保符合API 9A或ISO 10425标准。通过激光测径仪与投影仪量化分析表面不规则变形,识别局部直径偏差超过2%的异常区。
2. 力学性能测试
通过破断拉力试验机进行整绳破断强度检测,验证最小破断拉力(MBL)是否达标。同时开展弯曲疲劳试验,模拟实际工况下的循环载荷,评估抗疲劳寿命。附加扭转性能测试,检测多向受力下的稳定性。
3. 表面状态评估
采用目视检查与磁粉探伤结合的方式,检测外层钢丝的断丝率(如6倍捻距内断丝超过5%需报废)、磨损深度、腐蚀面积。针对海洋环境,需特别关注氯化物腐蚀导致的点蚀与氢脆现象。
4. 内部损伤检测
使用电磁检测仪(LMA)检测内部断丝、锈蚀及绳芯劣化情况。结合超声波探伤技术定位钢丝绳横截面损伤,识别局部金属截面积损失率(超过10%需预警)。
5. 润滑剂效能检测
分析润滑剂覆盖率、黏度保持率和防锈性能,防止因润滑失效导致的微动磨损。通过红外光谱检测油品氧化程度,确保其在高硫环境中的防护能力。
行业标准与检测周期
检测需严格遵循API Spec 9A《钢丝绳规范》、ISO 10425《石油天然气工业用钢丝绳》及DNVGL-RP-0034等标准。常规陆上设备建议每6个月检测一次,海上平台因环境严苛需缩短至3个月,突发超载或冲击事件后应立即进行损伤评估。
通过上述多维度的检测体系,可显著降低钢丝绳失效风险,延长关键设备使用寿命。检测数据的数字化存档与趋势分析,更能为预防性维护决策提供科学依据,助力石油天然气行业实现本质安全。
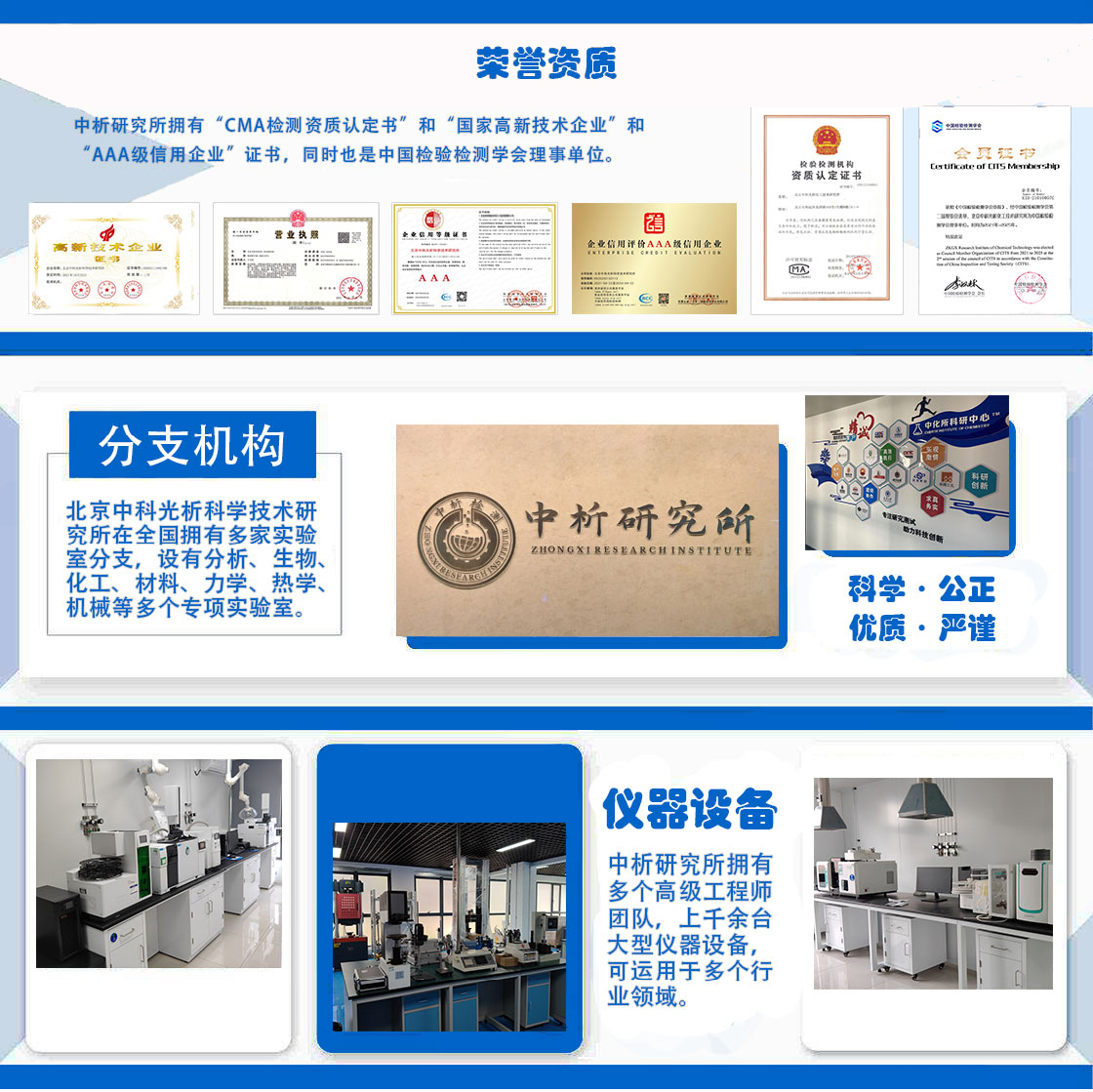
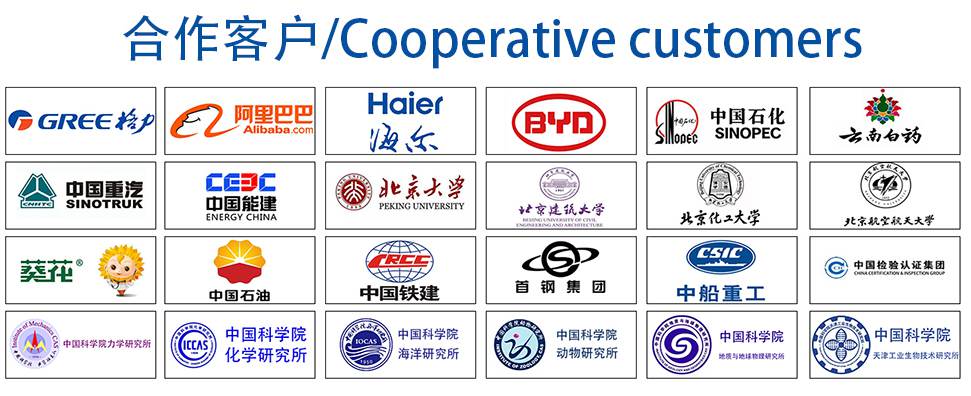