航空用钢丝绳检测的重要性
航空用钢丝绳作为飞机、直升机等航空器关键承力部件,广泛应用于起落架系统、控制缆索、安全装置等核心部位。其性能直接关系到飞行安全,一旦出现断裂或性能退化,可能引发灾难性后果。因此,针对航空钢丝绳的检测被国际航空管理机构(如FAA、EASA)列为强制性要求,需通过周期性检测和专项评估,确保其强度、耐疲劳性、耐腐蚀性等指标符合AS4792、AMS 6348等航空材料标准。检测过程需结合实验室分析与现场无损技术,覆盖从原材料到使用阶段的完整生命周期。
核心检测项目及方法
1. 结构参数检测
通过显微镜和影像分析系统,测量钢丝绳的捻距、股数、丝径及捻制均匀性,确保与设计规格一致。航空用钢丝绳通常采用6×19或7×7等特殊结构,需验证外层钢丝与芯部材料的匹配性。
2. 力学性能测试
包括破断拉力试验(依据ASTM A931)、扭转试验和反复弯曲试验,模拟极端工况下的承载能力。航空级钢丝绳的破断强度需达到1770MPa以上,同时需通过20万次以上的弯曲疲劳测试。
3. 表面缺陷检测
采用磁粉检测(MT)和涡流检测(ET)技术,识别直径0.1mm以上的表面裂纹、断丝及腐蚀坑。对于直径≤2mm的航空钢丝绳,需使用高灵敏度探头(≥120kHz)进行螺旋扫描。
4. 耐腐蚀性评估
进行盐雾试验(ASTM B117)和应力腐蚀试验,模拟海洋环境与高应力共同作用下的耐蚀表现。航空钢丝绳需在5%NaCl环境中保持720小时无明显锈蚀,Galvanic腐蚀电位差需<50mV。
5. 无损探伤技术应用
采用磁致伸缩导波检测(EMAT)和X射线衍射(XRD)技术,实现钢丝绳内部断丝、锈蚀及残余应力检测。新型相控阵技术可实现3D成像,缺陷检出率提升至99.2%。
6. 材料成分分析
通过光谱仪(OES)和能谱仪(EDS)检测碳、锰、硅等元素含量,确保符合302不锈钢或镀锌高碳钢的航空材料规范,铬含量偏差需控制在±0.15%以内。
检测周期与标准更新
根据FAR 25.571规定,航空钢丝绳的检测间隔不得超过500飞行小时或12个月(以先到者为准)。2023年更新的NAS 3610标准新增了微动磨损评估要求,需采用扫描电镜(SEM)分析钢丝表面微裂纹形貌。
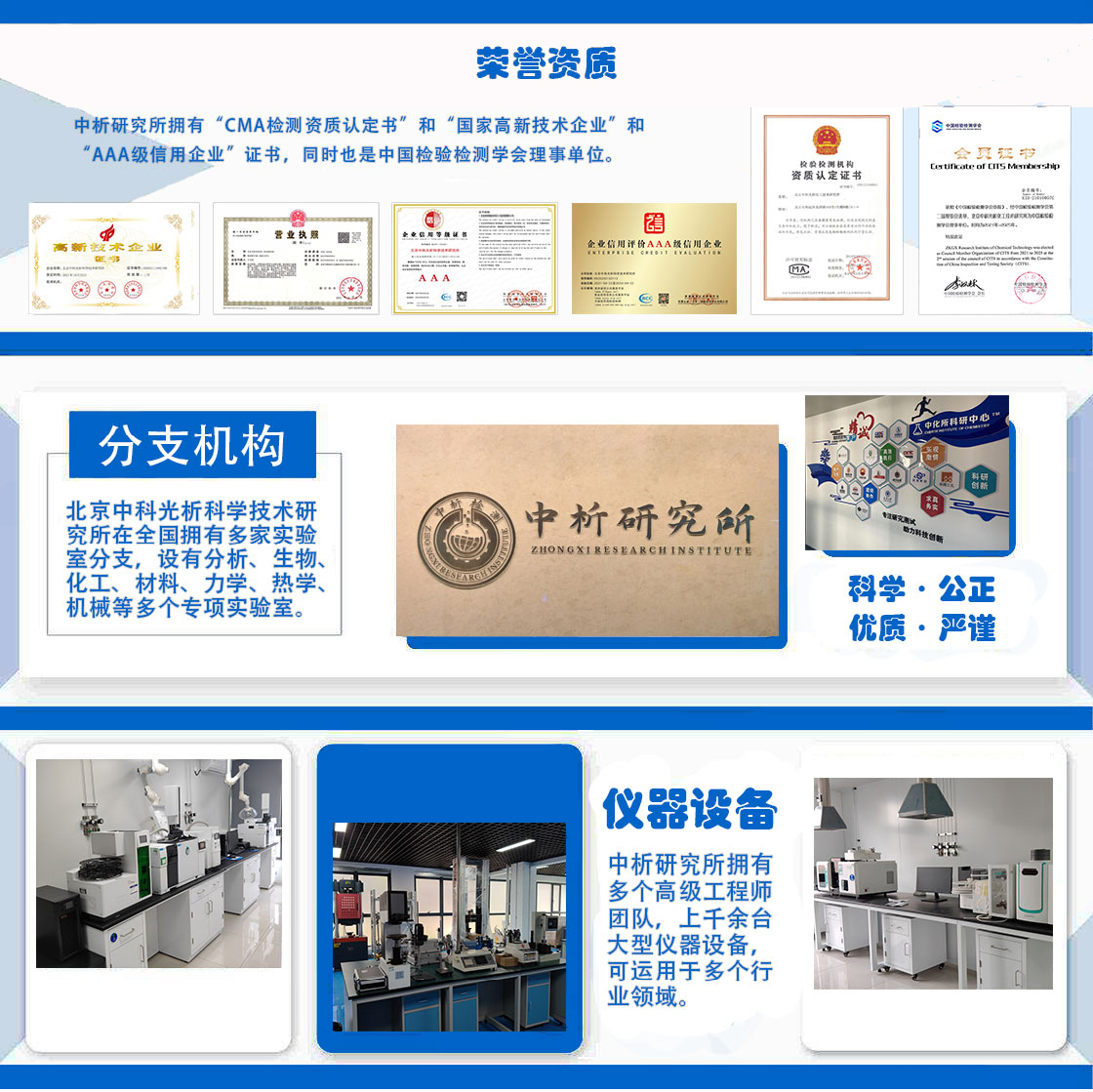
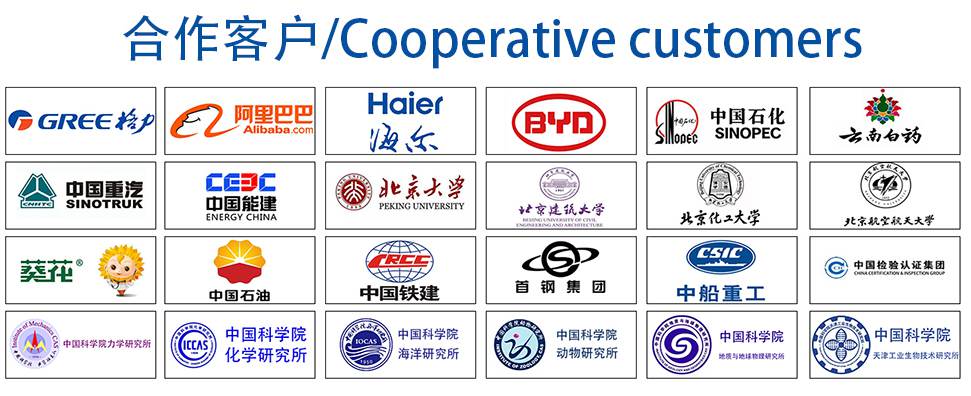