密封箱室检测的重要性与应用范围
密封箱室作为工业生产、实验室研究及特殊环境控制中广泛使用的设备,其性能直接关系到内部环境稳定性与安全性。无论是用于存储精密仪器、生化样本,还是作为气密性实验的关键装置,密封箱室必须满足严格的密封性、耐压性及抗腐蚀性等要求。近年来,随着高精度制造需求的增加和行业标准的升级,针对密封箱室的系统性检测已成为保障设备可靠性的核心环节。
核心检测项目及技术标准
1. 气密性检测
通过压力衰减法或示踪气体法(如氦气检漏)评估箱室在静态或动态压力下的密封性能,确保无气体泄漏。标准要求通常依据ISO 14644或行业特定规范,检测精度可达10⁻⁶ Pa·m³/s级别。
2. 结构完整性测试
利用超声波探伤、X射线成像等技术检查箱体焊缝、连接部位及材料的内部缺陷,防止因结构破损导致性能失效。同时需验证门锁、铰链等机械部件的耐久性。
3. 环境适应性验证
模拟高温、低温、湿度变化或腐蚀性气体环境,测试箱室的长期耐受能力。例如,在-40℃至120℃温度范围内进行循环测试,观察材料变形或密封件老化情况。
4. 安全防护功能检测
针对防爆型或生物安全型密封箱室,需验证超压保护装置、紧急排气系统及过滤器的有效性,确保突发情况下操作人员与设备的安全。
5. 控制系统校准
检测温湿度传感器、气压监控模块及自动化控制系统的精度,确保其与预设参数的偏差符合GB/T 25915等标准要求。
检测流程与问题应对
检测通常分为预检(目视检查、基础功能测试)、专项检测(气密性/耐压性等)及复检(修复后验证)三个阶段。常见问题包括密封圈老化、焊接点微渗漏或传感器漂移,需结合红外热成像、质谱分析等技术快速定位故障点,并采用更换材料或结构加固等方案解决。
行业趋势与规范升级
随着智能制造和绿色生产理念的普及,密封箱室检测逐步向智能化、非接触式方向发展。例如,采用AI算法分析泄漏数据,或通过物联网实现远程实时监控。同时,国际标准如ASME NQA-1-2019对检测频率和记录追溯性提出了更高要求,推动企业建立全生命周期管理体系。
通过科学的检测手段和流程优化,可显著提升密封箱室的安全性与使用寿命,为高精度制造、医药研发等领域的质量控制提供可靠保障。
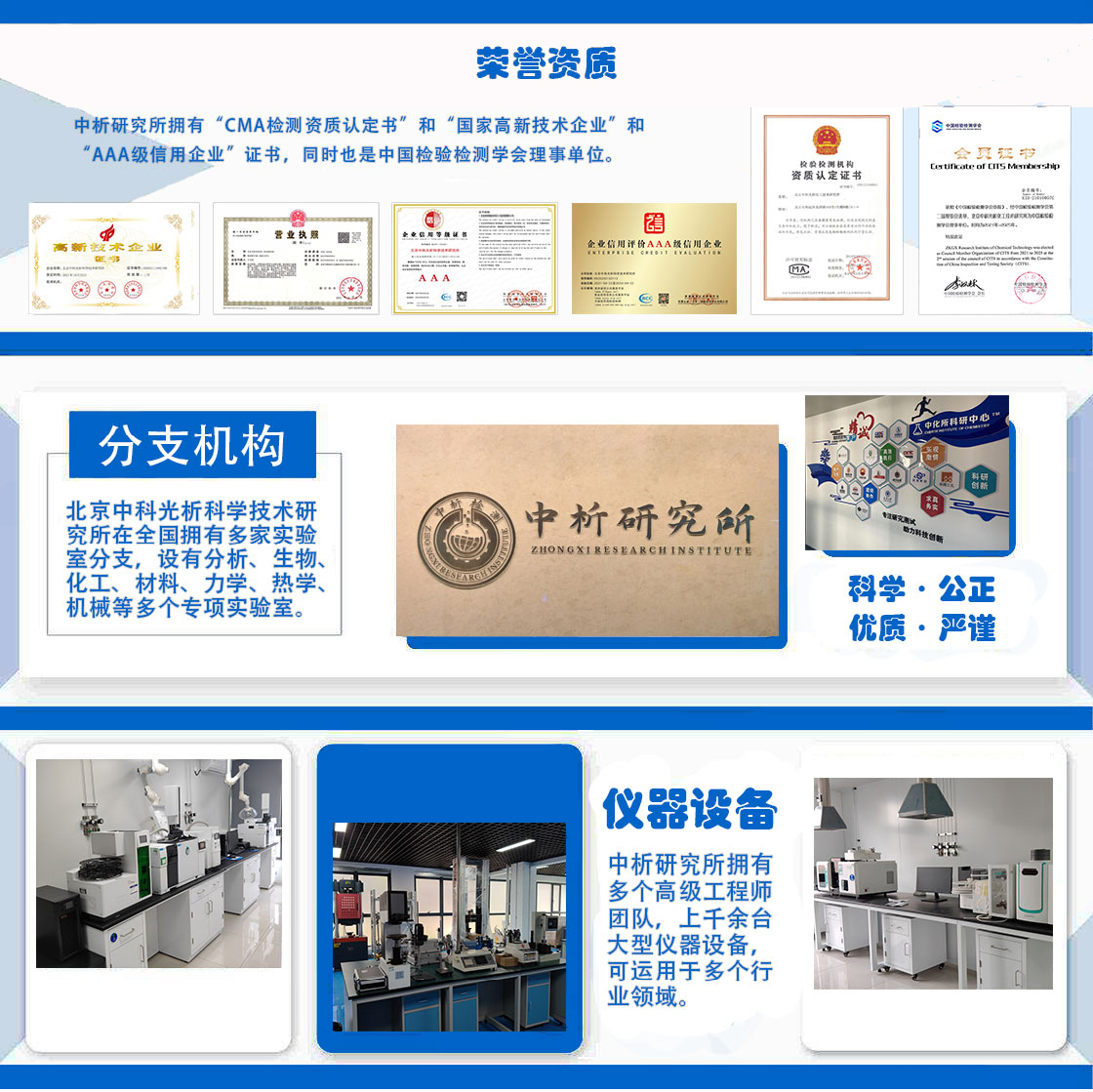
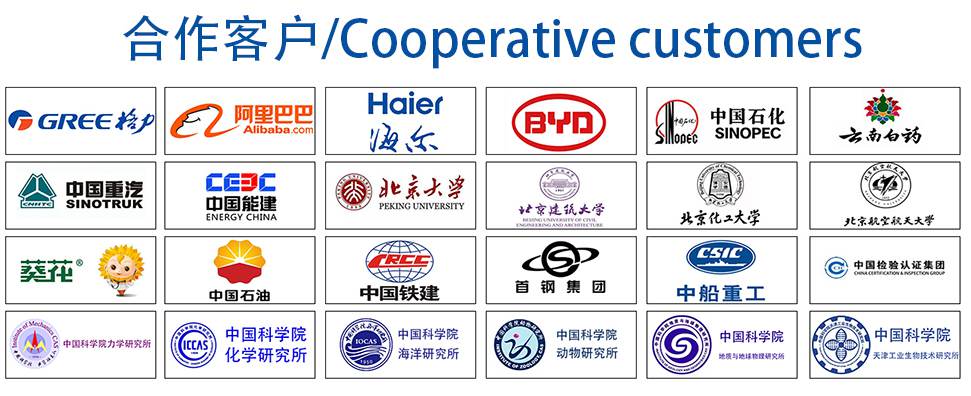