煤炭机械化采样系统检测的重要性
煤炭机械化采样系统是煤炭生产、贸易和质量控制中的关键设备,其采样结果的准确性直接关系到煤炭品质评价的公平性与科学性。随着我国对能源质量控制要求的不断提高,GB/T 19494《煤炭机械化采样》系列标准的实施,对采样系统的规范性和检测精度提出了更高要求。定期开展系统性能检测,既是保证采样数据真实有效的基础,也是企业通过计量认证、规避贸易纠纷的必要手段。通过系统性检测,可发现设备老化、参数偏移、部件磨损等隐患,确保采样过程符合“无偏差、等概率、代表性”的核心原则。
核心检测项目及技术要点
1. 采样精度验证
采用标准物质对比法,选取不同灰分、粒度的标准煤样进行全流程采样测试。通过计算系统采样结果与标准值的相对误差(Bias)及精密度(RSD),验证采样器切割速度、开口尺寸与煤流速度的匹配性。重点检测煤样残留率、粒度破碎率等指标,确保采样过程不改变物料原始特性。
2. 设备机械性能检测
对采样头、破碎机、缩分器等核心部件进行动态测试。检测内容包括:采样臂运动轨迹偏差不超过±5mm,切割速度误差≤0.1m/s,缩分器分样比波动值控制在±2%以内。采用激光测距仪和高速摄像技术记录设备运行参数,同步校验PLC控制系统指令响应精度。
3. 样品代表性评估
通过全断面采样试验验证系统抓取煤流的时空均匀性。采用分层取样法对比不同时间段、不同位置采集样品的工业分析结果,计算灰分、发热量等关键指标的F检验值,确保批次内样品方差不超过标准限值。特别关注煤流分层、粒度离析对采样代表性的影响。
4. 系统智能化检测
对自动除尘、防堵报警、数据追溯等智能模块开展功能性验证。检测包含:湿度传感器在RH30%-90%范围内的响应精度,堵煤报警触发时间≤3秒,样品编码系统的性及可追溯性。通过模拟极端工况测试系统容错能力,确保异常状态下的数据完整性。
检测流程与标准依据
完整检测应包含空载调试、负荷试验、校准验证三个阶段,严格遵循JJF(煤炭) 01-2018《煤炭机械化采样系统校准规范》。检测周期建议每12个月实施一次全面检测,在设备大修、部件更换或采样量超50万吨时增加临时检测。检测报告需包含偏差修正系数、不确定度评估及改进建议,形成完整的质量闭环管理。
通过系统化、标准化的检测方案实施,可有效提升煤炭采样设备的运行可靠性,为煤炭贸易结算、电厂配煤优化、环境排放控制提供坚实的数据支撑。随着智能传感技术和物联网平台的应用,未来机械化采样系统的检测将向实时监控、预测性维护方向发展,推动煤炭质量检测进入数字化新阶段。
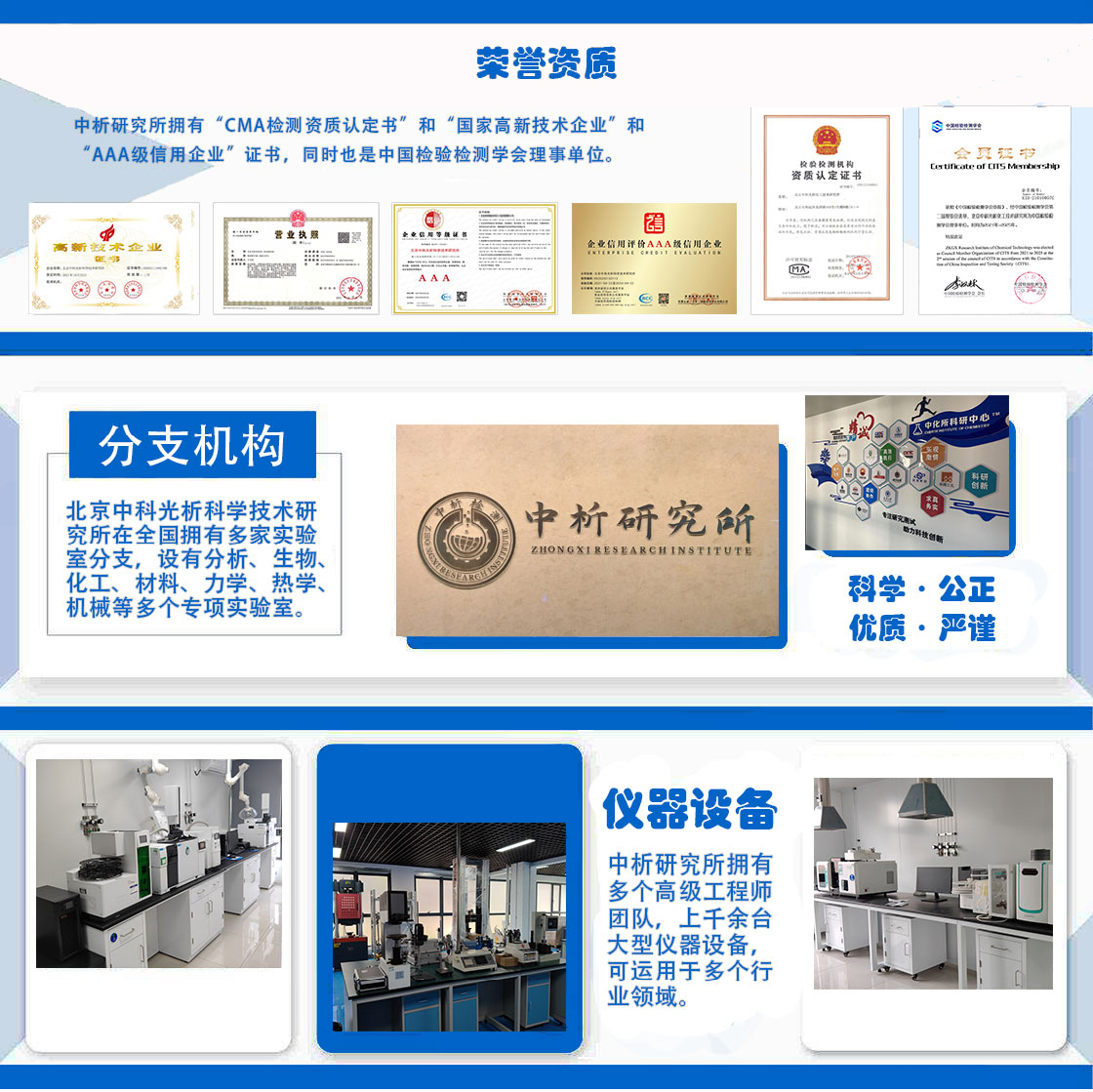
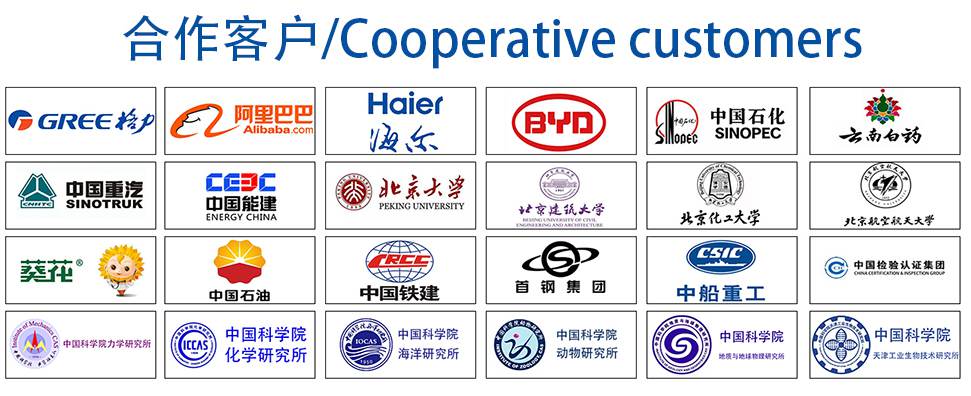