机车船舶用电加温玻璃检测的必要性
机车与船舶用电加温玻璃是保障驾驶员视野安全的核心组件,尤其在低温、高湿、结冰等极端环境下,需通过电热功能快速除雾除霜。由于其应用场景的特殊性,这类玻璃需具备耐冲击、抗高压、温度响应快等综合性能。为确保产品满足国际标准(如ISO 3537、ASTM C1048)和实际工况需求,必须进行全面的检测项目验证,涵盖电气性能、机械强度、环境适应性及光学特性等维度。
核心检测项目及方法
1. 电热性能测试
通过温升效率测试验证玻璃加热速度,要求初始低温(-30℃)至目标温度(20℃)的时间不超过5分钟,温控精度误差≤±5%。同时需检测电阻均匀性,使用四点探针法测量导电膜层的电阻分布,确保发热均匀性偏差<10%。
2. 结构强度与安全性检测
依据GB/T 5137.2-2020标准进行冲击试验:以227g钢球从2m高度自由落体冲击玻璃表面,要求无破裂或裂纹扩展。同时执行抗压疲劳测试,模拟船舶航行中频繁振动(频率5-50Hz,振幅±2mm)下的耐久性,累计测试时长≥200小时。
3. 环境适应性试验
包括高低温循环试验(-40℃至85℃循环100次)及湿热老化测试(湿度95%RH,温度55℃,持续1000小时),检测玻璃的电气稳定性与边缘密封性。针对船舶应用还需增加盐雾腐蚀测试,模拟海洋环境下的涂层耐蚀性。
4. 光学性能验证
使用分光光度计测量透光率(可见光波段≥75%)和雾度值(加热状态下≤2%),并通过霜雾模拟试验评估在骤冷条件下的自动除霜能力。
5. 电气安全检测
检测绝缘电阻(≥100MΩ/500VDC)和耐电压强度(500V交流电压持续1分钟无击穿),并验证接地连续性(电阻≤0.1Ω),确保漏电风险可控。
质量控制的关键节点
除上述检测外,需在原材料阶段验证导电膜层材料(如ITO、银浆)的附着力(划格法≥4B级),并在成品阶段执行红外热成像扫描,定位发热盲区。动态场景测试(如机车高速行驶时的风压冲击)亦为关键,需结合风洞试验验证玻璃在200km/h风速下的稳定性。
结语
通过系统化的检测流程,可确保电加温玻璃在机车、船舶等严苛场景下的可靠性与安全性。随着智能温控技术发展,未来检测体系将融入更多数字化手段(如AI缺陷识别),进一步提升质量控制精度与效率。
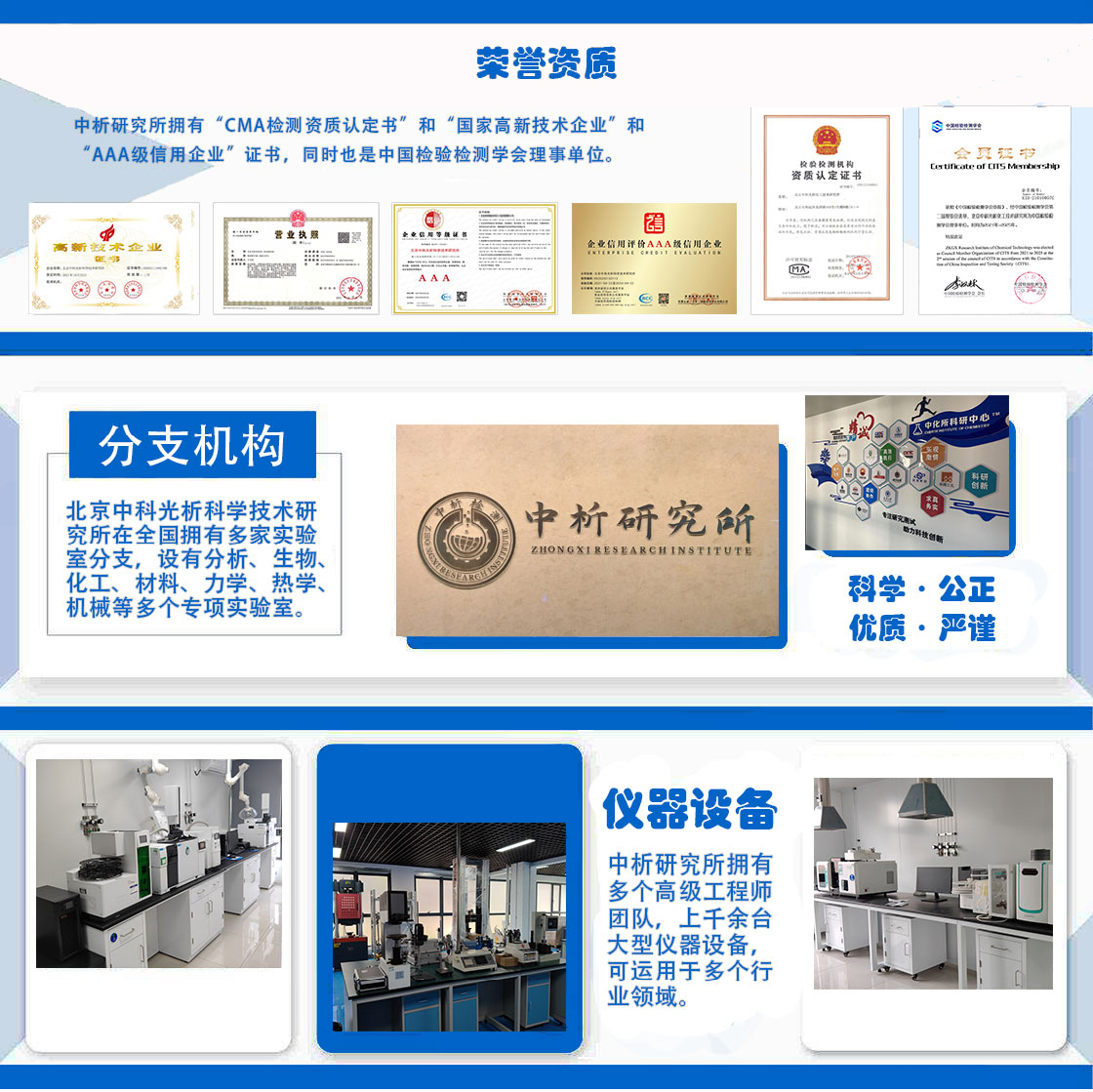
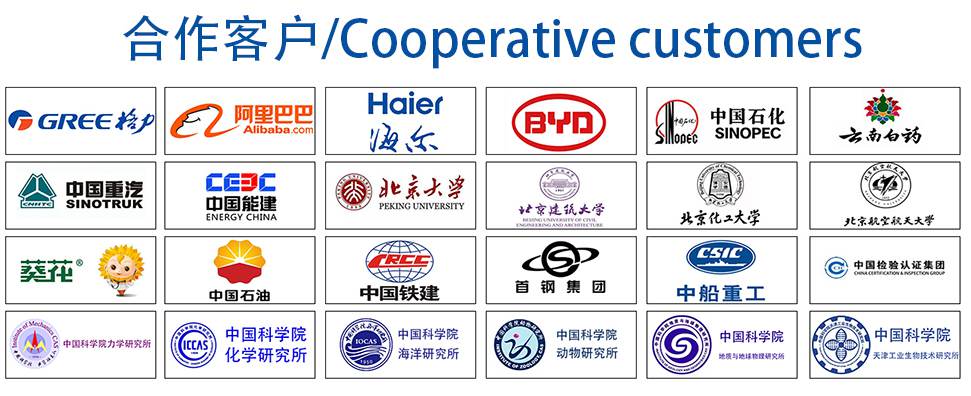