液态密封胶检测的重要性与应用领域
液态密封胶作为工业生产和日常生活中的重要粘接与密封材料,广泛应用于汽车制造、建筑工程、电子设备、航空航天等领域。其性能直接关系到产品的密封性、耐候性及使用寿命。然而,不同应用场景对密封胶的物理化学性质、环境适应能力等提出了差异化要求。为确保产品质量、安全性和合规性,液态密封胶检测成为生产、研发及使用环节中不可或缺的步骤。通过科学规范的检测项目,可精准评估密封胶的粘接强度、耐温性、耐腐蚀性等核心指标,从而优化生产工艺、降低使用风险。
液态密封胶检测的核心项目
1. 物理性能检测
液态密封胶的物理性能直接影响其施工效果与最终密封质量。主要检测项目包括: - 粘度测试:通过旋转粘度计测定液态密封胶的流动性能,确保其适应不同施工场景; - 固化时间:记录胶体从液态到完全固化的时间,评估施工效率与固化效果; - 密度与收缩率:分析胶体固化过程中的体积变化,避免因收缩导致密封失效。
2. 化学成分分析
化学成分决定了密封胶的耐候性、环保性及与其他材料的相容性。检测内容包括: - 主成分定性定量分析:通过红外光谱(FTIR)、气相色谱(GC)等技术确认有效成分含量; - 有害物质检测:检测甲醛、VOCs(挥发性有机物)等是否符合RoHS、REACH等环保标准。
3. 耐候性与环境适应性测试
模拟实际使用环境,评估密封胶的长期稳定性: - 高低温循环测试:在-40℃至150℃范围内测试胶体的热膨胀系数与抗开裂性; - 湿热老化测试:通过恒温恒湿箱加速老化,验证防水与耐潮性能; - 紫外光老化试验:评估紫外线照射下胶体的黄变、脆化等现象。
4. 力学性能与耐久性检测
针对密封胶的粘接强度与长期耐久性进行专项测试: - 拉伸强度与剥离强度:使用万能材料试验机测定胶体与基材的粘接力; - 抗剪切强度:模拟动态载荷下的抗变形能力; - 疲劳寿命测试:通过反复应力加载评估密封结构的长期可靠性。
5. 耐介质腐蚀性测试
根据应用场景接触的介质类型(如油、酸、碱等),检测密封胶的耐腐蚀性: - 浸泡实验:将胶体样品置于特定介质中,观察膨胀、溶解或强度变化; - 抗渗透性测试:评估胶体对液体或气体的阻隔能力。
检测标准与技术规范
液态密封胶检测需遵循国内外相关标准,包括: - 国际标准:ISO 11600(建筑密封胶分类与测试)、ASTM C920(弹性密封胶标准); - 行业标准:汽车行业常参照SAE J1899,电子行业参考IPC CC-830; - 国家标准:中国GB/T 13477系列标准对密封胶性能测试方法有详细规定。
结语
液态密封胶检测是保障产品质量与安全的核心环节。通过全面覆盖物理性能、化学成分、耐候性及力学强度的检测体系,企业可精准把控产品性能,提升市场竞争力。未来,随着新材料与新工艺的涌现,检测技术也将向智能化、高精度方向发展,为行业创新提供更强支撑。
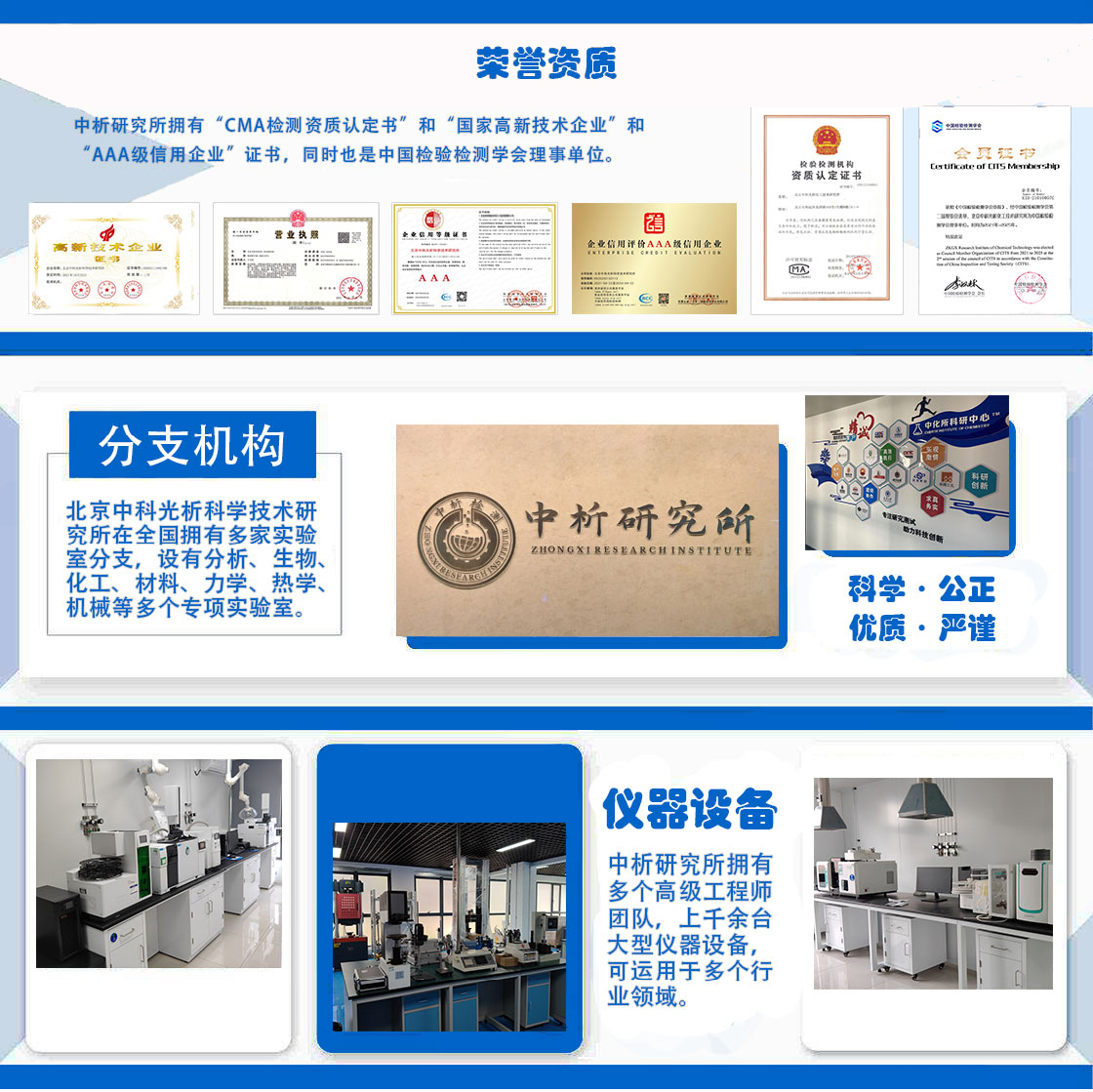
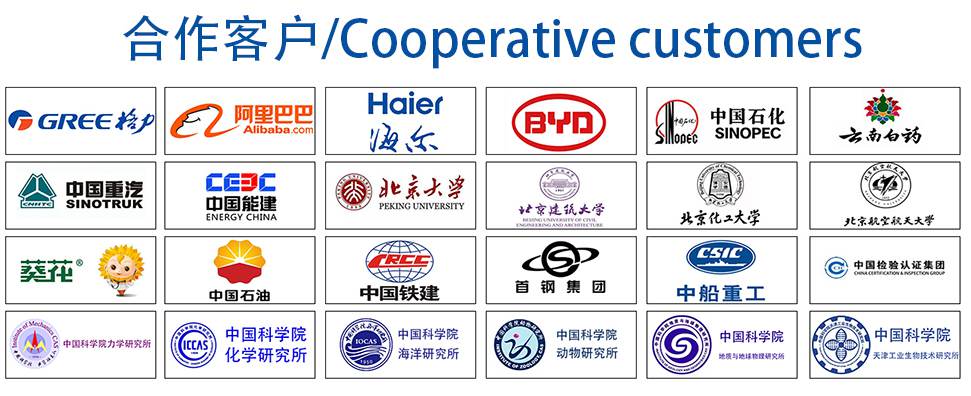