固定锥形阀检测的重要性及常见项目
固定锥形阀作为水利工程、石油化工及输水系统中广泛使用的流量控制设备,其性能稳定性直接关系到管道系统的安全运行。这类阀门通过锥形阀芯与阀座的配合实现流量调节,长期承受高压、高速流体冲击,易产生磨损、变形或密封失效。因此,定期开展系统性检测是预防泄漏、延长使用寿命的核心手段。本文将从材料性能、结构完整性、密封性等多个维度,详细解析固定锥形阀的关键检测项目。
核心检测项目分类
1. 材质与耐腐蚀性检测
通过光谱分析仪和硬度计对阀体、阀芯的金属成分及表面硬度进行验证,确保符合GB/T 12225或ASTM A276标准。针对腐蚀性介质工况,需进行盐雾试验或化学溶液浸泡测试,评估镀层(如镍基合金)的耐蚀性能。
2. 密封性能测试
采用阶梯式升压法进行静压密封试验:
- 低压阶段(≤0.6MPa)检测微泄漏量,使用气泡法或氦质谱检漏仪
- 高压阶段(1.5倍工作压力)保压30分钟,压降不超过5%为合格
动态密封测试则需模拟实际工况下的高频启闭动作,记录密封面磨损速率。
3. 结构完整性检查
使用三维激光扫描仪对锥形阀芯的锥度(通常为30°-60°)进行精度检测,配合阀座内径测量确保配合间隙≤0.05mm。焊缝需进行100%渗透探伤(PT)和20%射线探伤(RT),尤其关注阀体与法兰的过渡区域。
4. 执行机构功能性验证
对于电动/液压驱动装置,需检测:
- 行程精度(全开/全闭位置误差<1°)
- 启闭时间是否符合设计要求
- 紧急切断功能响应速度(通常要求≤3秒)
同步记录不同开度下的流量-压差曲线,验证调节线性度。
5. 振动与疲劳试验
在液压脉动试验台上模拟高频流体冲击,检测:
- 固有频率是否避开系统谐振区间
- 阀杆连接处是否出现松动
- 周期载荷下的裂纹萌生情况(建议≥10万次循环测试)
检测标准与周期建议
常规检测应参照API 598、GB/T 13927等标准执行,大修周期通常为3-5年或5000操作小时。对于核电站等特殊场景,需增加射线探伤比例至100%并缩短检测周期。检测数据建议采用数字化管理系统,建立全生命周期性能档案。
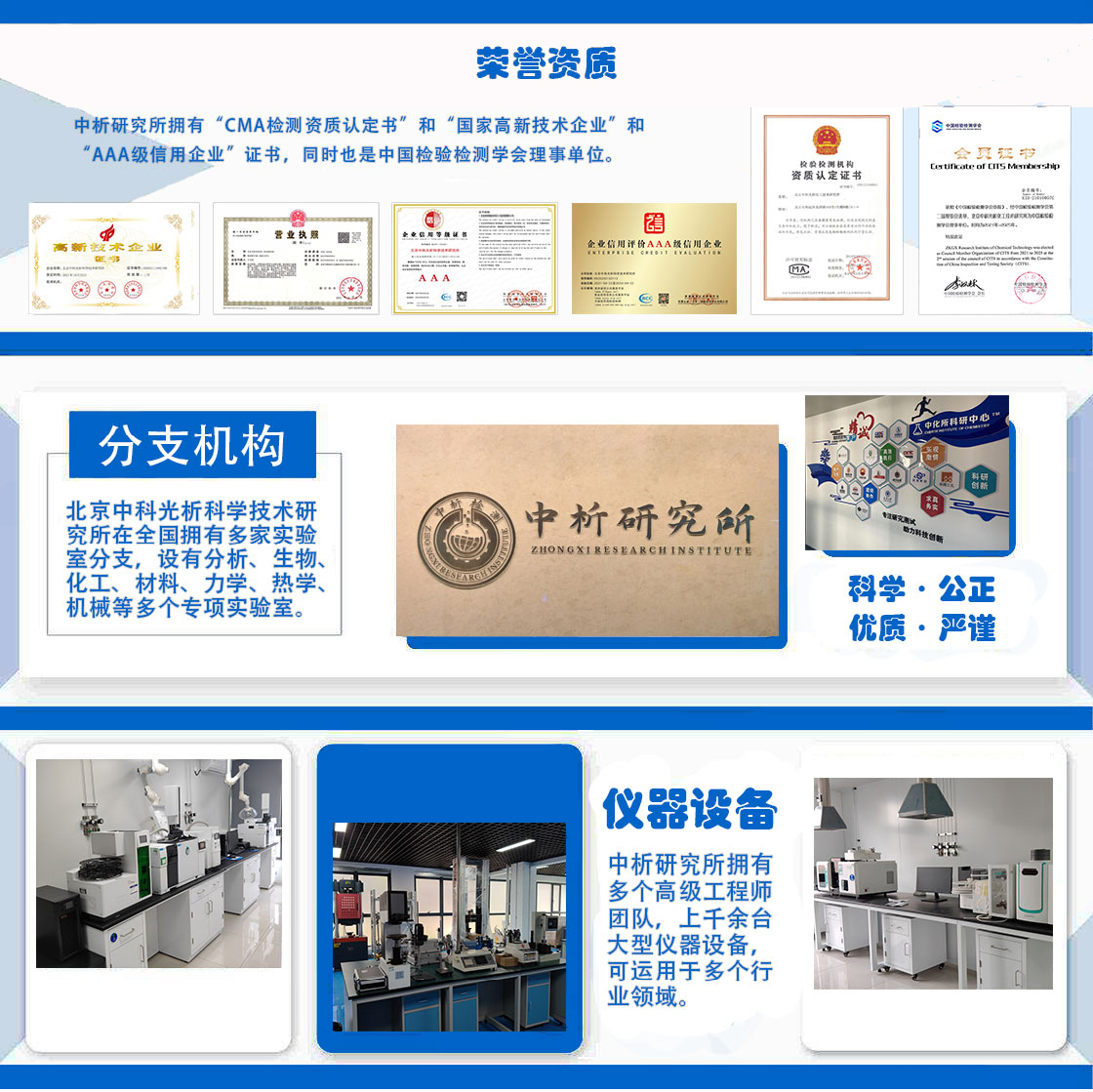
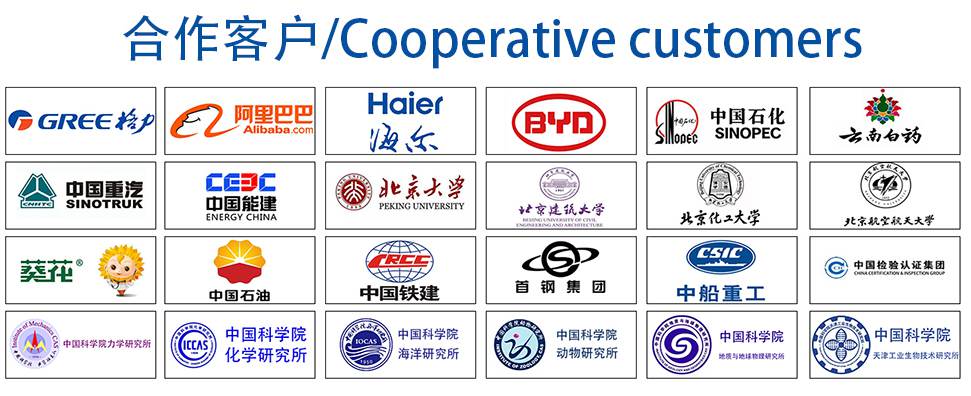