机电设备节能监测检测的重要性与实施要点
随着工业领域能源消耗占比的持续攀升,机电设备的节能性能已成为企业降低运营成本、实现可持续发展的核心关注点。节能监测检测作为评估设备能效水平的关键手段,能够通过对设备运行参数的精准分析,发现潜在的能源浪费问题,并为技术改造提供科学依据。据统计,通过系统性节能检测与优化,机电设备平均可减少15%-30%的能源损耗,显著提升经济效益和环保效益。
主要检测项目及技术规范
1. 设备能效参数测试
包括电机输入功率、输出功率、效率值等核心指标的动态监测,采用功率分析仪和扭矩传感器等专业设备,依据GB/T 12497《三相异步电动机经济运行》标准,判断设备是否符合国家能效等级要求。
2. 负载特性与运行匹配度分析
通过实时采集设备在不同工况下的负载曲线,评估电机与负载的匹配程度。重点检测空载率、过载时长及轻载运行占比,避免“大马拉小车”等低效现象,确保设备处于最佳能效区间。
3. 能源损耗量化评估
针对设备的热损耗、机械摩擦损耗、电磁损耗等隐性能源浪费,使用红外热像仪、振动传感器等工具进行多维度检测。结合GB 17167《用能单位能源计量器具配备和管理通则》,建立损耗模型并提出改进措施。
4. 控制系统能效优化验证
对变频器、软启动器等控制装置的调节性能进行测试,验证其响应速度、调速范围和节能效果。通过对比传统工频运行与智能控制模式下的能耗差异,量化节能改造的实际收益。
5. 环境参数关联性监测
同步记录设备运行环境的温度、湿度、电压稳定性等参数,分析外部条件对能耗的影响规律。例如高温环境可能引发电机绕组电阻增加,导致额外电能损耗。
检测数据应用与优化建议
通过建立设备能效数据库,结合AI算法进行趋势预测和异常诊断。针对检测结果提出定制化改进方案,如更换高效电机、加装能源回收装置或优化控制逻辑。典型案例显示,某制造企业经检测后实施变频改造,年节电量达120万kWh,投资回收期仅1.8年。
定期开展机电设备节能监测检测不仅是履行国家《节约能源法》的法定要求,更是企业实现精细化能源管理的必要路径。通过构建覆盖设备选型、运行监控、维护升级的全生命周期能效管理体系,可有效推动工业领域向绿色低碳方向转型。
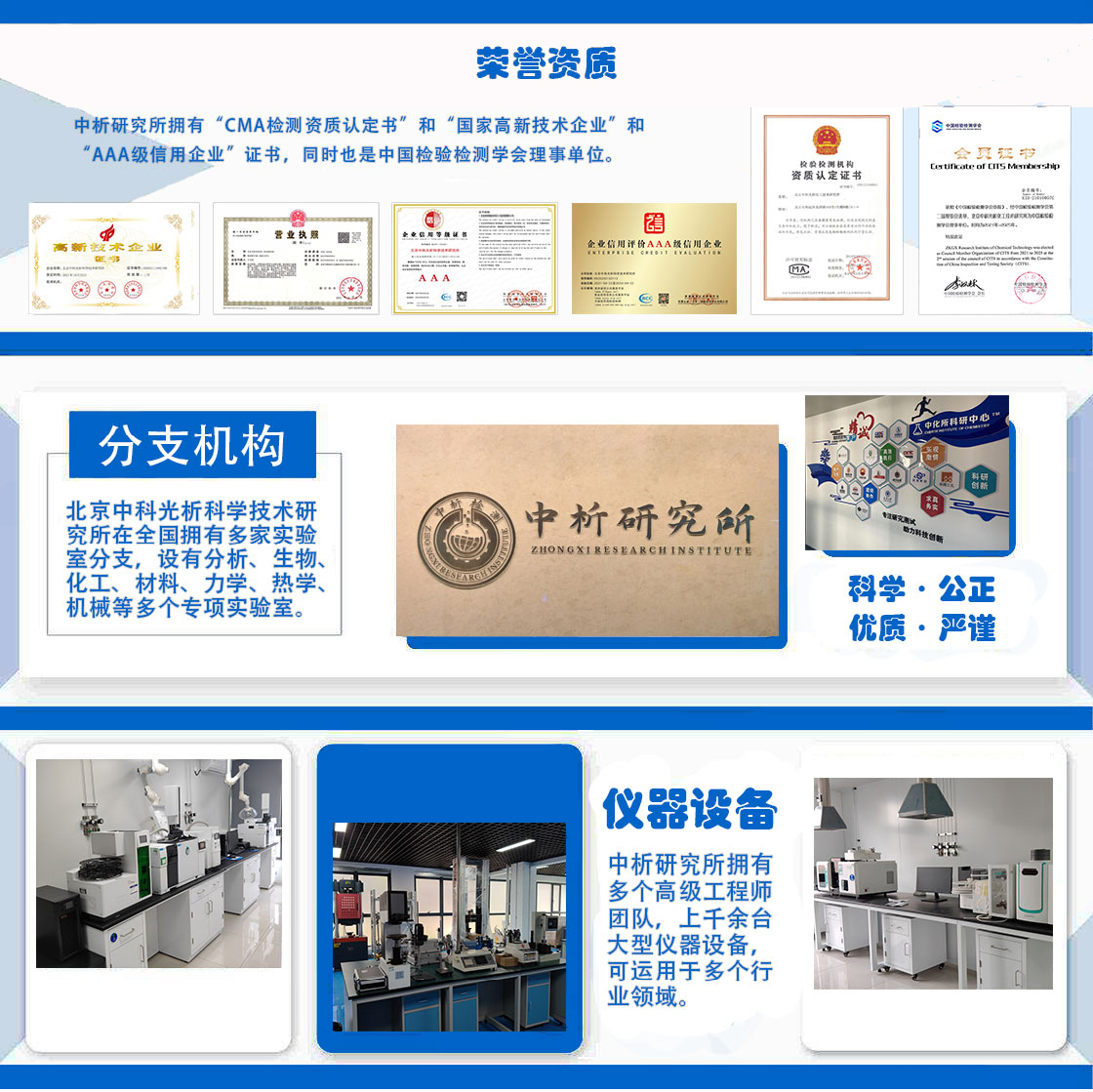
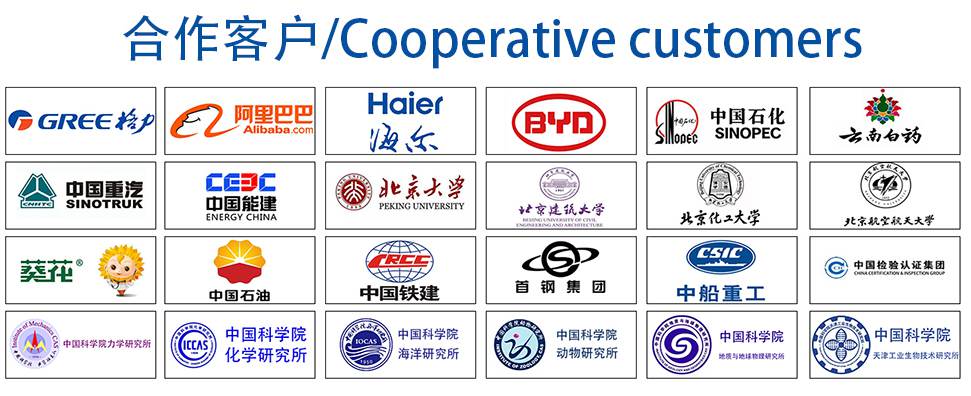