水泥工业用通过式分离器的重要性与应用场景
在现代化水泥生产工艺中,通过式分离器作为核心分选设备,承担着粉磨系统物料分级的重要职责。其通过动态气流与机械运动的协同作用,对粒径不同的颗粒进行高效分离,直接影响生料粉磨效率、成品细度以及系统能耗水平。随着水泥行业节能降耗要求的不断提高,通过式分离器的性能检测已成为保障生产稳定性和提升经济效益的关键环节。定期开展专业化检测不仅能及时发现设备隐患,更能通过参数优化实现系统提产5-10%、节电15%以上的显著效果。
关键检测项目体系
1. 分离效率动态监测
采用激光粒度分析仪对进出口物料进行粒径分布测定,通过绘制Tromp曲线计算切割粒径(d50)和分级精度指数(K值)。要求细粉提取率≥85%,粗粉回料含细量≤12%,确保分选过程符合工艺设计参数。
2. 转子结构强度测试
使用三维振动分析仪对转子系统进行全速工况下的动平衡检测,径向跳动量需控制在0.15mm以内。通过有限元分析验证叶片应力分布,重点检测焊缝区域的疲劳强度,确保承受8000小时连续运行考验。
3. 密封系统气密性验证
采用氦质谱检漏法对壳体法兰、检修门等关键密封部位进行检测,局部泄漏率应≤1×10⁻⁵Pa·m³/s。动态工况下使用红外热成像仪监测温度场分布,异常温差超过15℃需立即排查密封失效点。
4. 传动系统性能评估
通过功率分析仪测量主电机负载特性,对比设计值与实测值的偏差。齿轮箱振动速度应≤4.5mm/s(ISO10816标准),轴承温升不超过环境温度35℃。同步检测减速机润滑油的金属磨损颗粒浓度。
5. 智能控制系统校验
模拟不同工况测试变频器调速响应特性,速度调整偏差需≤±1rpm。利用OPC通讯协议验证PLC与DCS系统的数据交互完整性,确保转速、压差等关键参数的采样频率达到100Hz级别。
6. 耐磨件剩余寿命预测
采用超声波测厚仪对导向叶片、撒料盘等易损件进行厚度测量,结合EDX能谱分析检测表层硬化层完整性。建立磨损速率数学模型,准确预测部件更换周期,避免突发性停机事故。
检测周期与优化建议
常规检测应每6个月系统开展一次,高强度工况下需缩短至3个月检测周期。建议建立设备全生命周期数据库,通过AI算法分析历史检测数据,动态调整风机转速、导流板角度等17项关键参数,实现分选效率的持续优化。同步开展能效对标管理,推动分离器单位处理量电耗下降至0.8kWh/t以下。
结语
科学规范的检测体系是保障通过式分离器高效运行的基础,通过引入智能化检测装备和大数据分析技术,水泥企业可显著提升设备管理水平。这不仅关系到生产系统的稳定运行,更是实现清洁生产、降低碳排放的重要技术支撑,为行业绿色转型提供坚实保障。
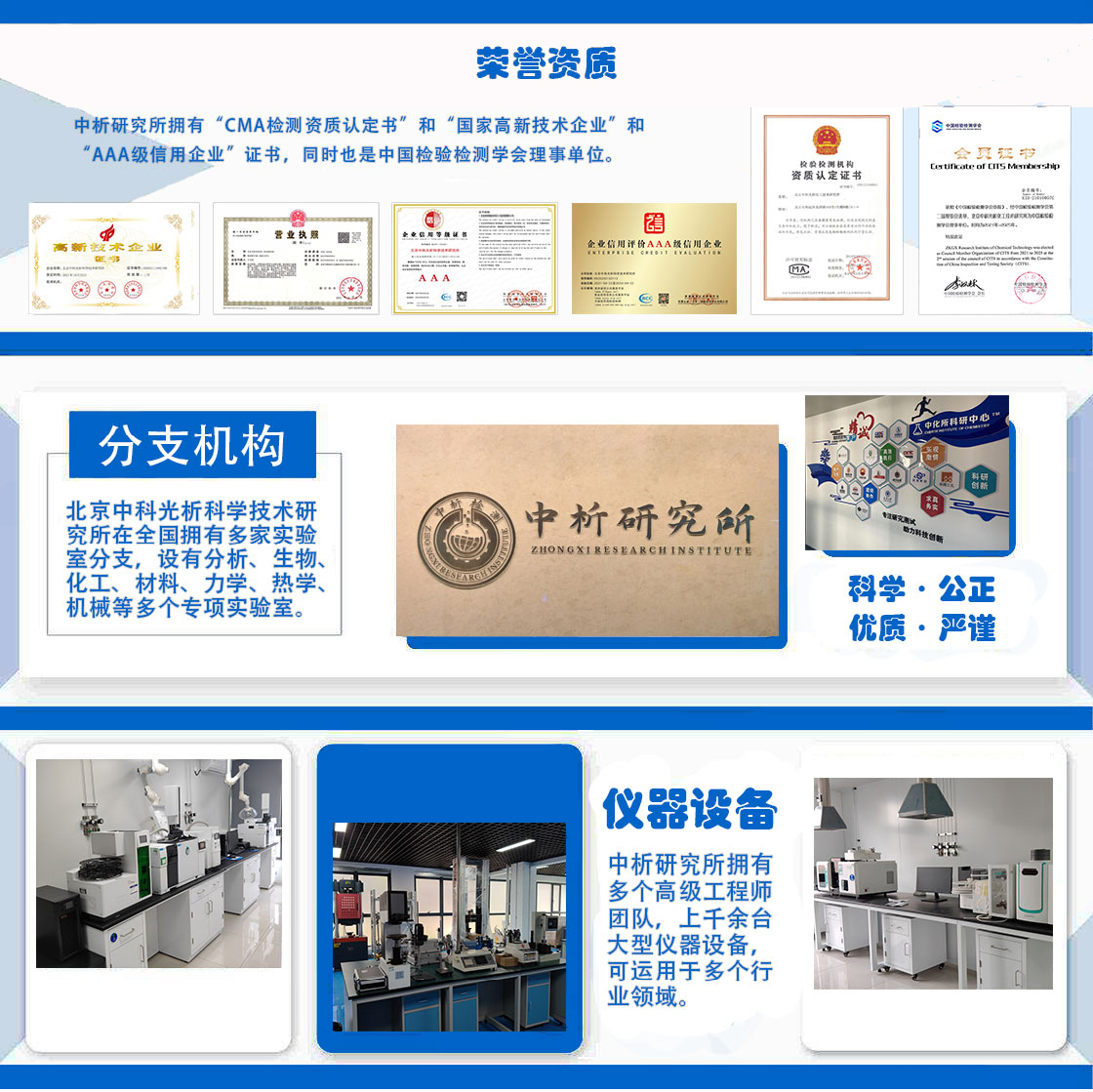
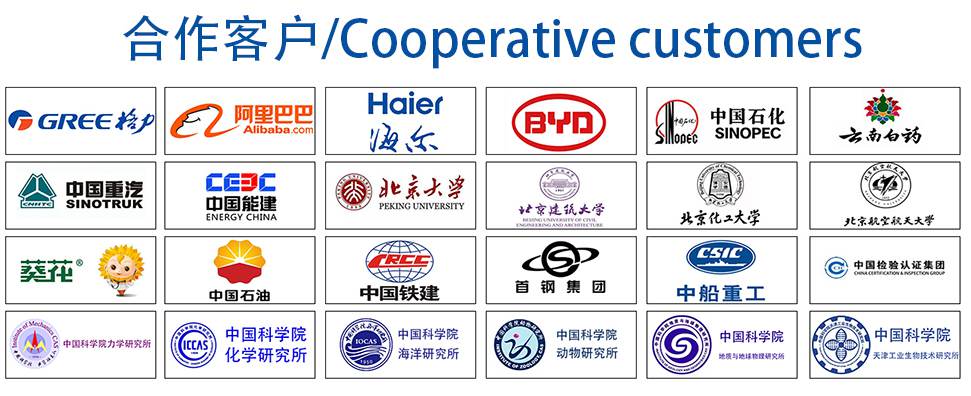