油漆工业用溶剂油检测的重要性
在油漆生产过程中,溶剂油作为关键成分之一,主要用于调整涂料的黏度、促进成膜以及改善施工性能。其质量直接影响油漆的干燥速度、光泽度、附着力及环保性。然而,溶剂油中可能含有对人体有害的苯系物、硫化物等杂质,或存在挥发速度不匹配等问题,导致漆膜缺陷或环境污染。因此,对油漆工业用溶剂油进行全面检测是确保产品质量、符合环保法规、保障生产安全的重要环节。
溶剂油的主要检测项目及方法
1. 馏程检测
馏程反映溶剂油的挥发性能,通过测定其初馏点、终馏点及馏程范围,判断其是否符合挥发速度要求。若馏程过宽可能导致漆膜起泡或流平性差,常用GB/T 6536标准进行测试。
2. 闪点检测
闪点是衡量溶剂油安全性的核心指标,过低的闪点会增加生产、储存和运输中的火灾风险。通常采用闭口杯法(GB/T 261)测定,确保其闪点高于工作环境温度。
3. 苯系物含量检测
苯、甲苯、二甲苯等物质具有毒性和致癌性,需通过气相色谱法(GB 18581)严格控制其含量。尤其针对环保型油漆,苯系物限量需符合国家强制标准。
4. 硫含量检测
硫化物会腐蚀生产设备并污染环境,通过紫外荧光法(SH/T 0689)检测总硫含量,确保其低于500mg/kg的行业限值。
5. 芳烃含量分析
高芳烃溶剂可能导致漆膜黄变或VOCs排放超标,需依据ASTM D3257标准测定芳烃比例,优先选用低芳或无芳溶剂油。
6. 密度与挥发性测试
密度(GB/T 1884)影响溶剂与树脂的相容性,而挥发性残留物(GB/T 9722)需低于0.5%,以避免漆膜表面产生雾影或发黏。
7. 铜片腐蚀试验
通过GB/T 5096测试溶剂油对金属的腐蚀性,要求铜片变色等级≤1级,确保储罐和管道的长期稳定性。
8. 水分及杂质检测
水分(卡尔费休法,GB/T 6283)和机械杂质(GB/T 511)超标会导致漆膜缩孔或雾化不良,需分别控制在0.05%和0.01%以下。
综合检测的意义
系统性检测不仅能筛选符合工艺要求的溶剂油,还能帮助企业优化配方、降低VOCs排放,同时规避因溶剂质量问题引发的产品召回风险。通过建立从原料入厂到成品出厂的全流程检测体系,油漆生产企业可显著提升市场竞争力和可持续发展能力。
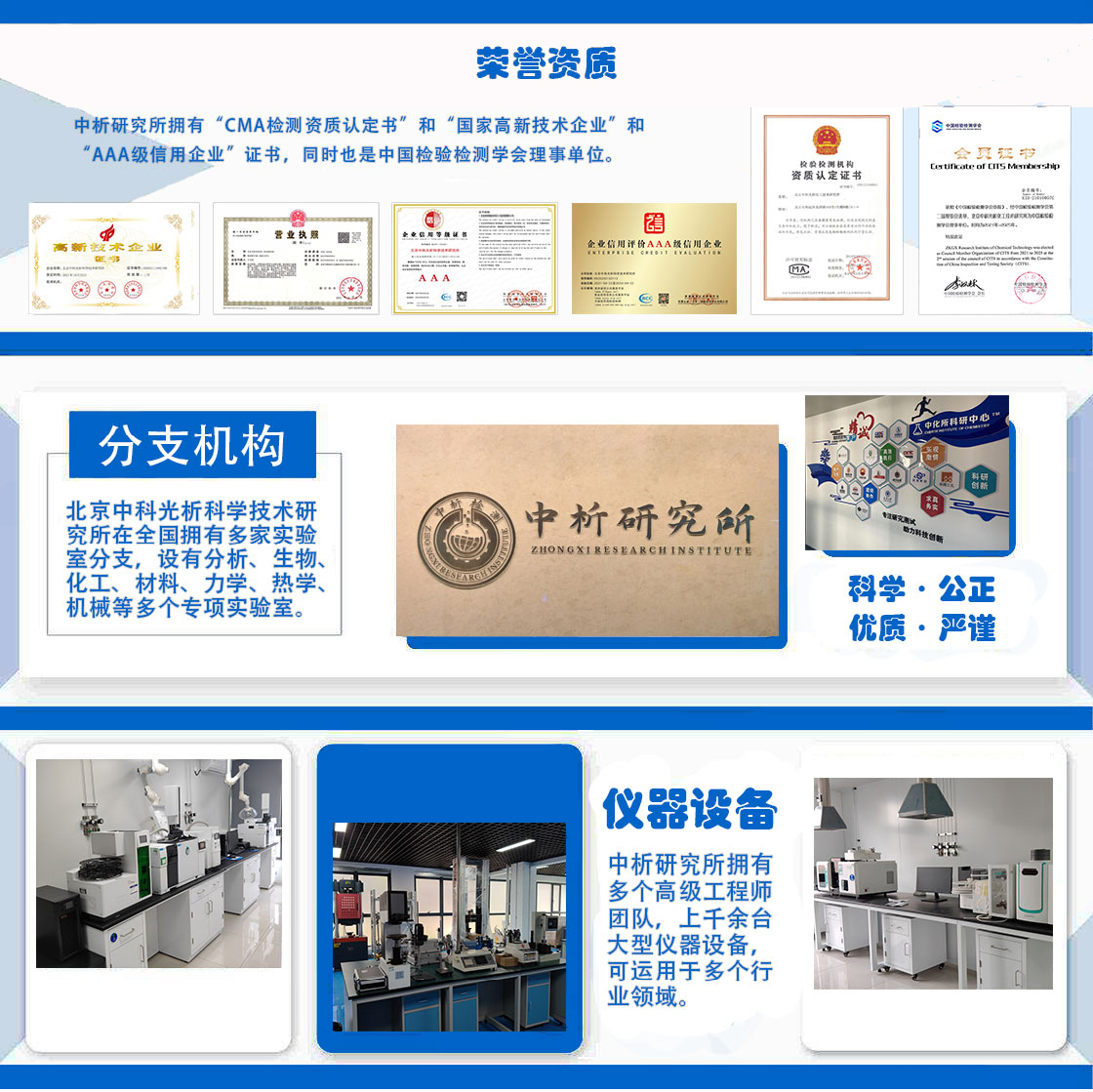
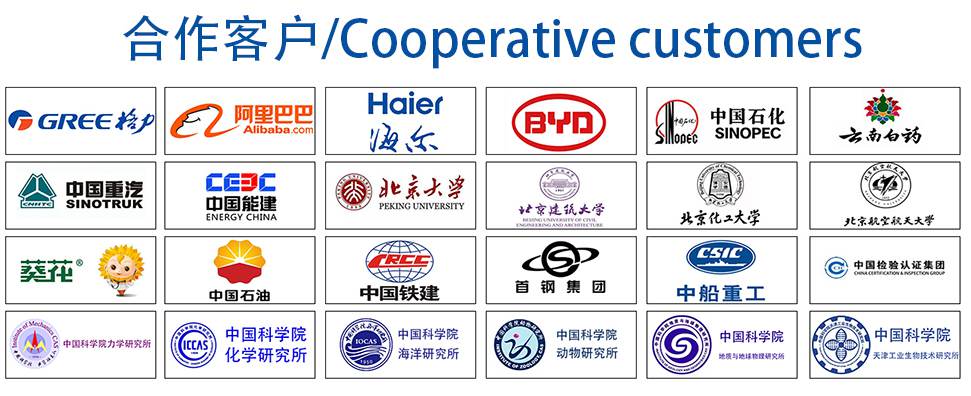