水泥窑用耐火材料检测的重要性
水泥窑作为水泥生产中的核心设备,其内部长期处于高温、化学侵蚀、热应力冲击等极端工况下。耐火材料作为窑炉内衬的“保护层”,直接关系到窑炉的运行效率、能耗水平及使用寿命。据统计,耐火材料的性能劣化是导致水泥窑非计划停窑的主要原因之一。因此,对耐火材料进行科学、系统的检测,不仅是保障生产连续性的基础,也是优化工艺、降低成本的关键。检测内容需覆盖材料的物理性能、化学成分、热性能及结构完整性,同时结合工况模拟实验,全面评估其在实际应用中的可靠性。
核心检测项目及方法
1. 物理性能检测
耐火材料的物理性能直接影响其抗热震性和机械强度。主要检测项目包括: - 体积密度与显气孔率:通过阿基米德法测定,评估材料的致密性; - 常温抗压强度:采用万能试验机测试材料在静态压力下的承载能力; - 耐磨性:模拟窑内物料冲刷环境,评估材料表面抗磨损性能。 这些指标决定了耐火材料在动态负载下的长期稳定性。
2. 化学成分分析
针对不同材质的耐火材料(如高铝砖、镁铬砖、碳化硅制品等),需通过X射线荧光光谱(XRF)或电感耦合等离子体(ICP)分析主成分及杂质含量。例如: - Al₂O₃含量决定高铝砖的耐火度; - MgO与Cr₂O₃比例影响镁铬砖的抗碱侵蚀能力; - SiO₂含量超标可能导致材料高温下产生液相,降低结构强度。
3. 热性能测试
耐火材料的热性能是其在窑内服役的核心指标: - 耐火度:通过高温锥法测定材料软化温度; - 热震稳定性:将试样加热至工作温度后急速冷却,循环测试直至出现裂纹; - 导热系数:采用激光闪射法评估材料的隔热性能,直接影响窑体外壁温度控制。 这些数据为优化窑炉热工制度提供依据。
4. 结构完整性评估
利用无损检测技术(如超声波探伤、红外热成像)和微观分析手段(SEM、XRD)检测材料内部缺陷、裂纹扩展及相变情况。例如: - 超声波检测可发现施工砌筑时的空洞缺陷; - SEM分析能观测高温下晶界氧化或渣蚀现象; - XRD可识别材料使用后新生成的矿物相(如硅酸二钙),判断侵蚀机制。
5. 使用寿命预测模型
结合实验室加速老化试验与现场拆检数据,建立耐火材料剩余寿命预测模型。通过测量材料残余强度、厚度损耗率及耐侵蚀指数,动态调整更换周期。例如: - 镁铝尖晶石砖的侵蚀速率与窑内碱硫比呈正相关; - 碳化硅浇注料在还原性气氛下的氧化失重需纳入寿命计算。
检测标准与行业规范
国内外主要参照ASTM C系列、ISO 10081及GB/T 2997-2015等标准。水泥企业可结合窑型(如预分解窑、立窑)、燃料类型(煤、替代燃料)及工艺参数定制检测方案。例如: - 采用替代燃料的窑炉需强化对Cl⁻、SO₃侵蚀的检测; - 窑口浇注料需额外增加抗CO气体侵蚀试验。
结语
系统化的耐火材料检测不仅能够延长窑炉运行周期(部分案例显示可提高30%以上),更能为故障预警提供数据支持。随着在线监测技术(如内衬厚度雷达扫描)的普及,检测正从实验室向智能化、实时化方向演进,为水泥行业节能降耗提供技术保障。
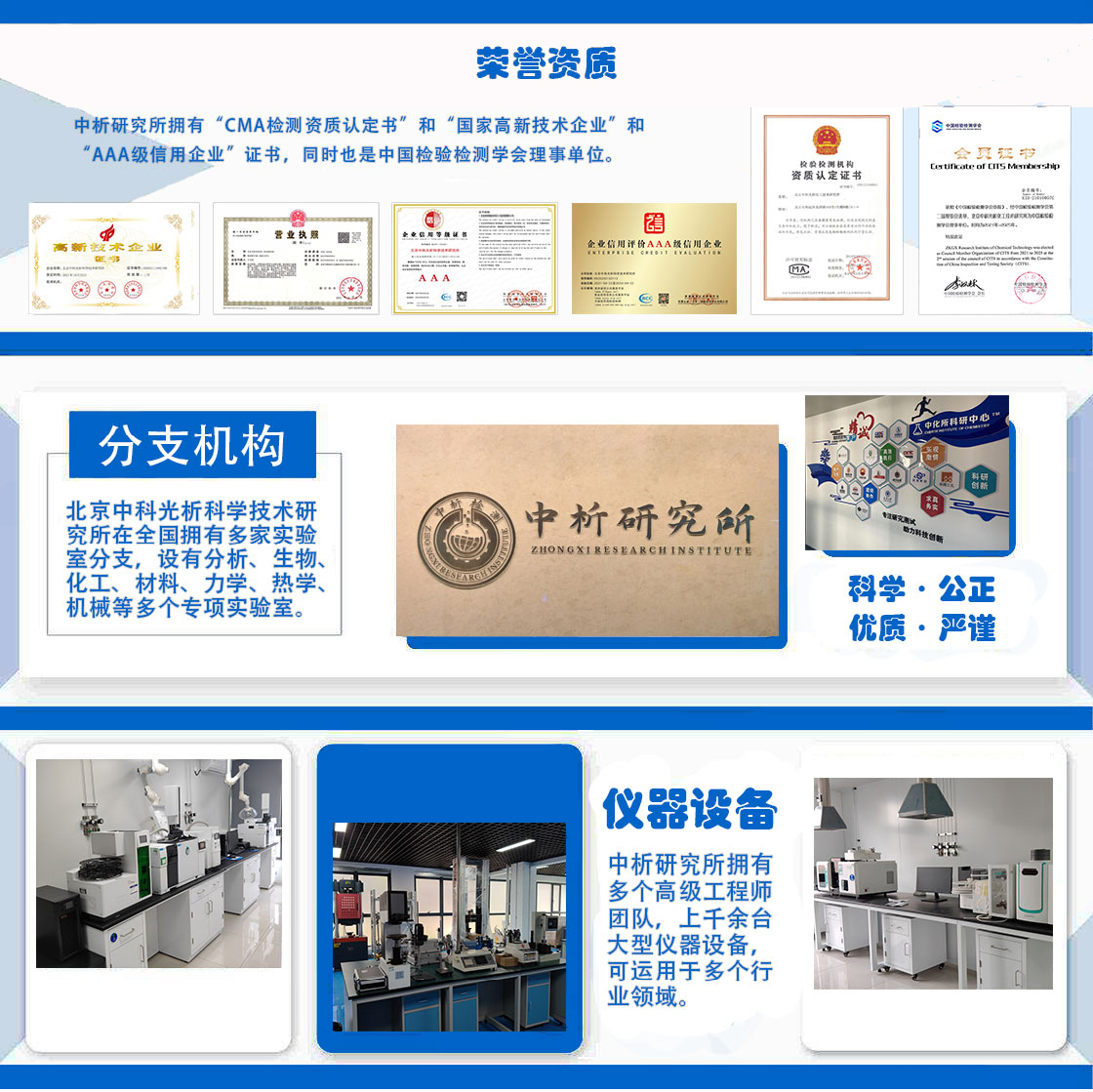
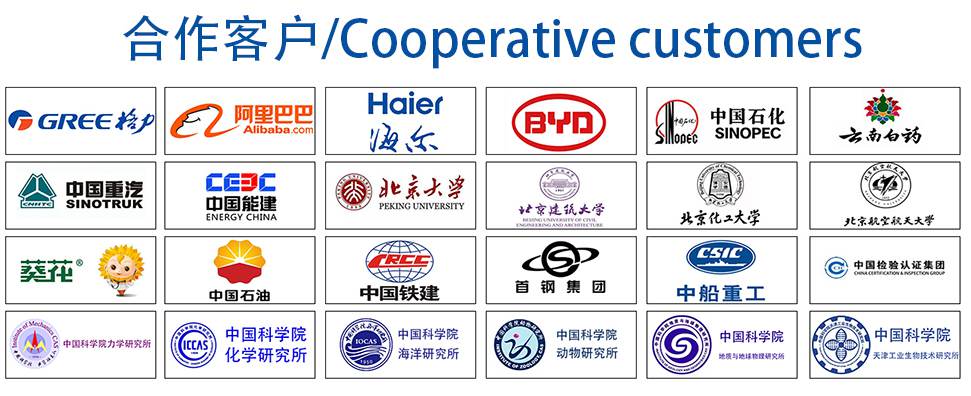