光刻用石英玻璃晶圆检测的核心意义
在半导体制造工艺中,光刻技术是决定芯片性能和良率的关键环节,而石英玻璃晶圆作为光刻掩膜版的核心材料,其质量直接影响光刻图形的精度与重复性。由于石英玻璃需承受高能激光(如EUV极紫外光或DUV深紫外光)的长期辐照和复杂化学环境,对其物理、化学及光学特性的检测要求极为严苛。通过系统性检测,可确保晶圆在透光率、热稳定性、表面平整度等方面满足纳米级制程需求,避免因材料缺陷导致的光刻图形失真、线宽偏差等问题,从而保障芯片制造的良品率。
核心检测项目与技术要求
1. 表面质量检测
石英玻璃晶圆的表面粗糙度需控制在亚纳米级别(通常≤0.5nm Ra),检测采用白光干涉仪或原子力显微镜(AFM)。同时需通过暗场显微镜和自动缺陷检测系统(ADI)识别表面划痕、凹坑、颗粒污染等微观缺陷,缺陷密度需小于0.1个/cm²。对于EUV用晶圆,还需检测表面镀膜(如Mo/Si多层膜)的均匀性及附着力。
2. 几何参数测量
包括厚度一致性(公差±1μm以内)、总厚度偏差(TTV<0.3μm)和平整度(局部翘曲≤0.5μm)检测。采用激光干涉仪或电容式测厚仪实现非接触式测量,并通过光学轮廓仪分析晶圆的三维形貌,确保其与光刻机载物台的贴合精度。
3. 材料特性分析
通过X射线荧光光谱(XRF)检测金属杂质含量(如Fe、Cu需<1ppb),红外光谱(FTIR)分析羟基(-OH)浓度(影响热稳定性),以及热膨胀系数(CTE)测试(要求CTE<0.55×10⁻⁶/℃)。对于高能激光应用场景,还需评估抗辐照损伤阈值,防止材料因长期照射发生结构劣化。
4. 光学性能验证
关键参数包括紫外至深紫外波段的透光率(193nm处透光率需>99.5%)、折射率均匀性(Δn<5×10⁻⁶)以及波前畸变(RMS值≤λ/20)。通过分光光度计、Zygo干涉仪等设备进行多维度测试,并结合严格的环境温湿度控制(如±0.1℃恒温)排除外部干扰。
5. 环境稳定性测试
模拟光刻机运行条件,进行高温(300℃)、低温(-50℃)循环冲击测试,评估晶圆抗热震性能。同时需在真空或惰性气体环境中检测材料释气特性(outgassing),防止挥发物污染光刻机光学系统。耐久性测试要求晶圆在10^5次激光脉冲照射后仍保持性能稳定。
6. 洁净度与封装检测
通过颗粒计数器(符合ISO 14644-1 Class 1标准)和化学残留分析(离子色谱法检测Na⁺、Cl⁻等<0.1ng/cm²),确保晶圆无污染风险。封装环节需验证保护膜的完整性及抗静电性能,避免运输存储过程中产生二次污染。
检测技术的发展趋势
随着半导体工艺向3nm及以下节点推进,检测技术正朝着更高灵敏度(如皮米级表面分析)、多参数联检(如在线式光谱+形貌同步监测)和智能化方向发展。基于机器学习的缺陷分类算法和数字孪生技术,可实现检测数据与工艺参数的实时联动,进一步提升光刻用石英玻璃晶圆的品质控制效率。
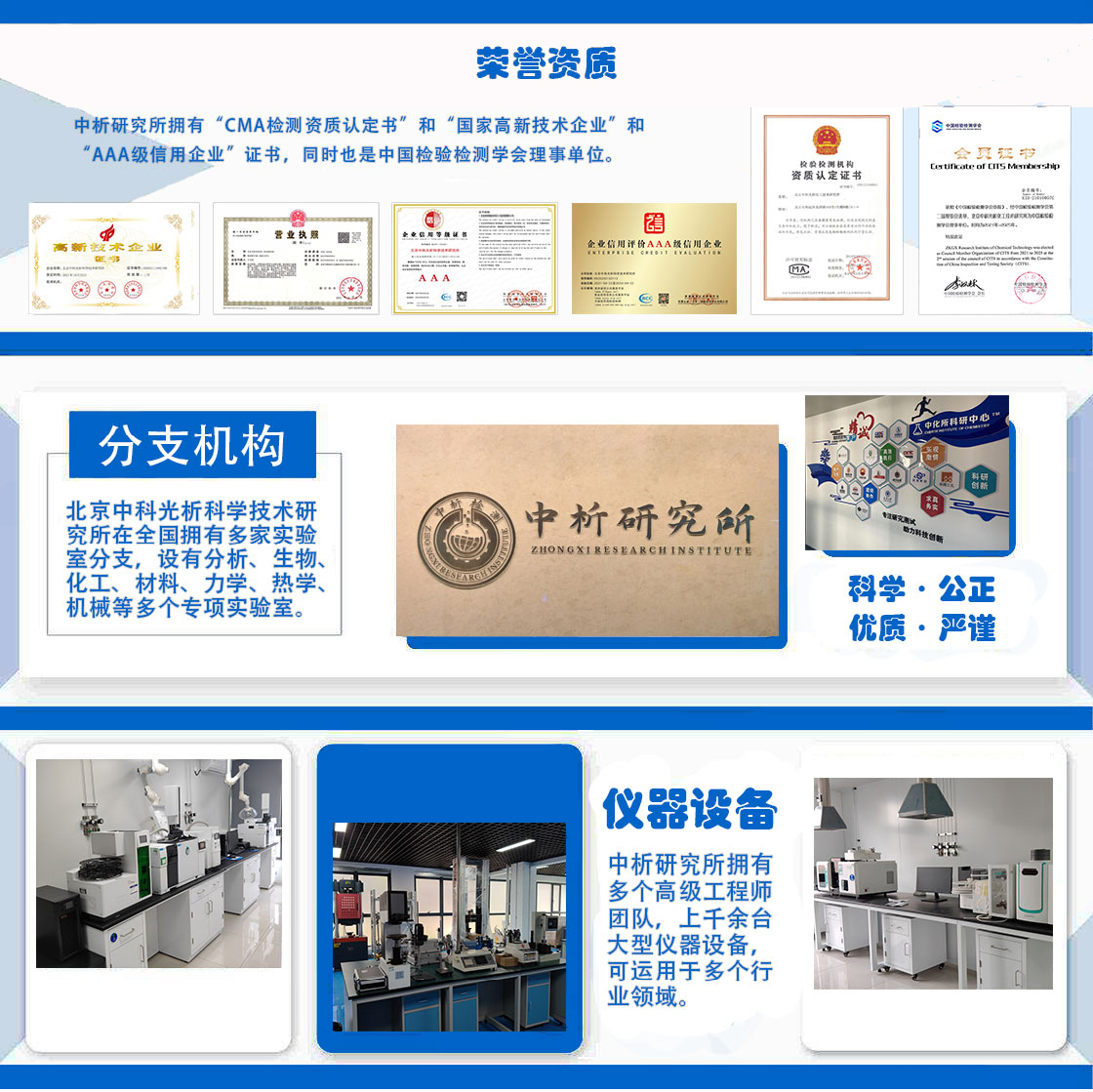
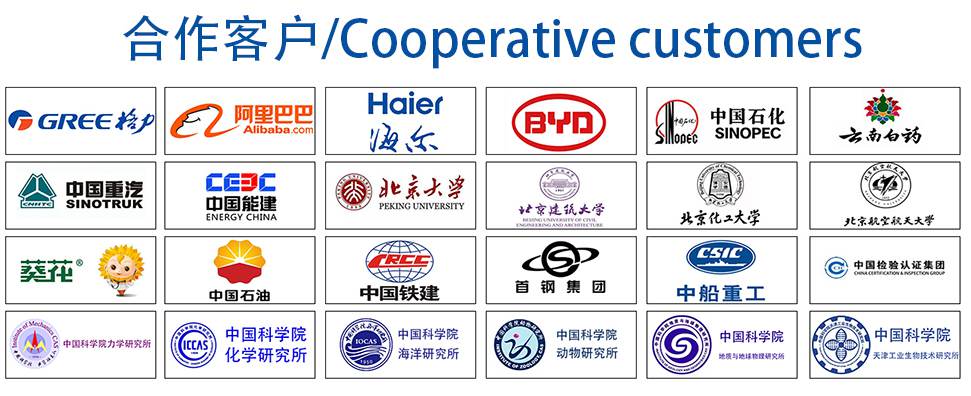