管道涂层检测的意义与重要性
管道涂层作为保护输送介质安全性和延长管道寿命的关键屏障,在石油、天然气、化工等工业领域具有不可替代的作用。优质的涂层能够有效阻隔腐蚀介质、减少机械损伤风险并提升管道运行效率。然而,涂层在施工、运输或长期使用过程中可能出现厚度不均、孔隙、剥离等缺陷,这些隐患可能导致管道腐蚀、泄漏甚至安全事故。因此,通过系统化的管道涂层检测项目,对涂层的物理性能、化学稳定性及完整性进行全面评估,是保障管道安全运营的核心环节。
核心检测项目及方法
1. 涂层厚度检测
涂层厚度直接影响防腐效果,检测需覆盖全管道表面。磁性测厚仪(适用于金属基材)和超声波测厚仪(非金属基材)是常用工具。根据ISO 2808或ASTM D7091标准,需随机选取测量点,确保厚度符合设计要求(通常误差不超过±10%)。
2. 附着力测试
通过划格法(ASTM D3359)或拉力试验机(ASTM D4541)评估涂层与基材的结合强度。附着力不足会导致涂层剥离,引发局部腐蚀。检测时需模拟实际工况温度,重点关注焊缝、弯头等应力集中区域。
3. 孔隙率检测
使用电火花检测仪(高压针孔检测)或湿海绵法(低压环境)定位涂层中的微小孔隙。根据NACE SP0188标准,检测电压需根据涂层厚度调整(如每毫米厚度施加1.5-3kV),确保缺陷点可被精准识别。
4. 耐候性与化学兼容性测试
实验室模拟环境中通过盐雾试验(ASTM B117)、紫外线老化试验(ASTM G154)验证涂层抗腐蚀与抗老化能力。对于化工管道,需额外测试涂层在特定酸碱介质中的溶胀、脱落情况。
5. 电化学性能检测
通过电化学阻抗谱(EIS)或开路电位测量,评估涂层的绝缘性能和阴极保护兼容性。该检测可提前预判涂层失效趋势,尤其适用于海底管道等难以维修的场景。
6. 外观与完整性检查
结合目视检查与工业内窥镜,排查涂层表面裂纹、鼓包、流挂等缺陷。红外热成像技术可快速定位隐蔽的剥离区域,提高检测效率。
检测标准与行业规范
国际通用的检测标准包括ISO 21809(油气管道涂层)、NACE SP0169(阴极保护)及ASME B31.4/8(压力管道规范)。国内需同步参照GB/T 23257《埋地钢质管道聚乙烯防腐层》等标准,确保检测结果具备法律与技术双重合规性。
技术创新与未来趋势
随着智能检测技术的发展,无人机搭载高清摄像头与AI算法可完成高空或长距离管道的自动化巡检。同时,纳米涂层材料的应用推动检测项目向微观结构分析延伸,如扫描电镜(SEM)观察涂层晶体排列。未来,结合大数据与物联网的预测性维护系统将成为行业新方向。
结语
管道涂层检测不仅是质量验收的必经环节,更是预防性维护策略的重要组成部分。通过多维度、多技术的检测手段,结合严格的标准化流程,能够显著降低管道运营风险,为工业基础设施的安全与可持续发展提供坚实保障。
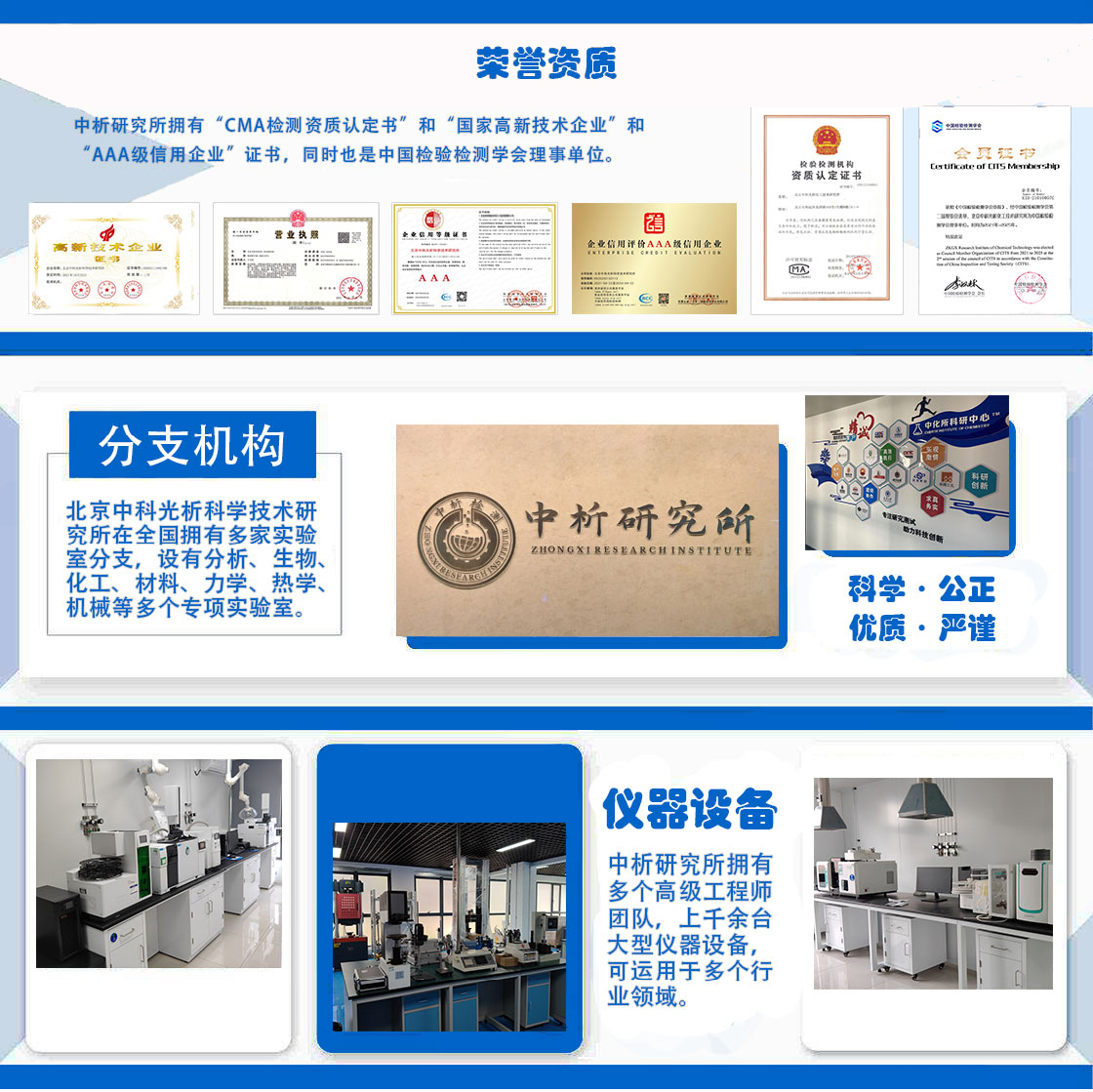
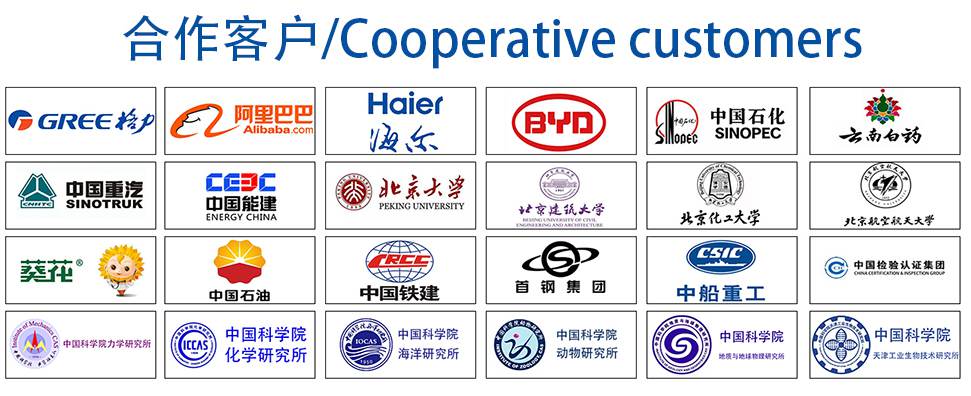