烧失量-灼烧差减法检测
发布时间:2025-07-17 20:07:34- 点击数: - 关键词:
实验室拥有众多大型仪器及各类分析检测设备,研究所长期与各大企业、高校和科研院所保持合作伙伴关系,始终以科学研究为首任,以客户为中心,不断提高自身综合检测能力和水平,致力于成为全国科学材料研发领域服务平台。
立即咨询烧失量-灼烧差减法检测:核心检测项目详解
一、检测目的
- 测定样品中挥发物(水分、有机物、碳酸盐等)的总含量。
- 评估材料的纯度、热稳定性及工艺适用性。
- 为工业生产(如水泥煅烧、陶瓷烧结)提供质量控制依据。
二、适用范围
- 材料类型:水泥生料、陶瓷原料、土壤、矿物、化工粉末等。
- 挥发成分:结晶水、碳酸盐(CO₂释放)、有机物(燃烧)、硫化物(SO₂挥发)等。
- 典型行业:建材、冶金、环境保护(污泥分析)、地质勘探。
三、检测原理
- �1m1:灼烧前样品+坩埚质量(g)
- �2m2:灼烧后样品+坩埚质量(g)
四、核心检测项目与流程
1. 设备与材料
- 仪器:
- 高温马弗炉(精确控温±10℃,最高温度≥1000℃)
- 分析天平(精度0.1mg)
- 干燥器(含硅胶或变色干燥剂)
- 铂金/瓷坩埚(耐高温、无挥发性)
- 辅助工具:坩埚钳、研磨设备、干燥箱。
2. 样品预处理
- 研磨:过100~200目筛,确保均一性。
- 预干燥:部分样品需105℃烘至恒重(若含水率高)。
- 称量:取样量依预期烧失量调整(通常1~5g,精准至0.0001g)。
3. 灼烧程序
- 温度设定:依材料类型选择(如水泥:950±25℃;土壤:550℃测有机质)。
- 升温步骤:
- 空坩埚预灼烧至恒重,冷却称量(扣除坩埚空白值)。
- 装入样品后,置于高温炉中,缓慢升温至目标温度(避免热震)。
- 灼烧时间:通常1~4小时,直至恒重(连续两次称量差≤0.5mg)。
4. 冷却与称量
- 使用坩埚钳将坩埚转移至干燥器,冷却至室温(防止吸潮)。
- 迅速称量,减少环境湿度影响。
五、质量控制与误差分析
- 重复性测试:平行样品≥3份,相对标准偏差(RSD)≤1%。
- 空白试验:扣除坩埚自身烧失量(尤其是瓷坩埚需预灼烧)。
- 标准物质比对:使用已知LOI的标准样品校准流程。
- 干扰因素控制:
- 硫/氯化合物:高温下可能生成SO₃、HCl,需在通风环境或惰性气氛中灼烧。
- 吸湿性样品:冷却后快速称量,或使用防潮天平室。
六、注意事项
- 安全操作:佩戴高温手套、护目镜,避免灼伤。
- 温度校准:定期用热电偶校验马弗炉温区均匀性。
- 样品代表性:确保充分混匀,避免局部成分偏差。
- 数据记录:详细记录灼烧温度、时间、环境温湿度。
七、典型应用案例
- 水泥生产:控制生料中石灰石(CaCO₃)分解程度,烧失量过高预示煅烧不充分。
- 陶瓷原料:黏土中有机物含量影响烧结收缩率,需LOI≤5%。
- 土壤污染检测:550℃烧失量可间接反映有机污染物含量。
八、总结
上一篇:水蒸气透过率检测下一篇:耐水性、耐化学性检测
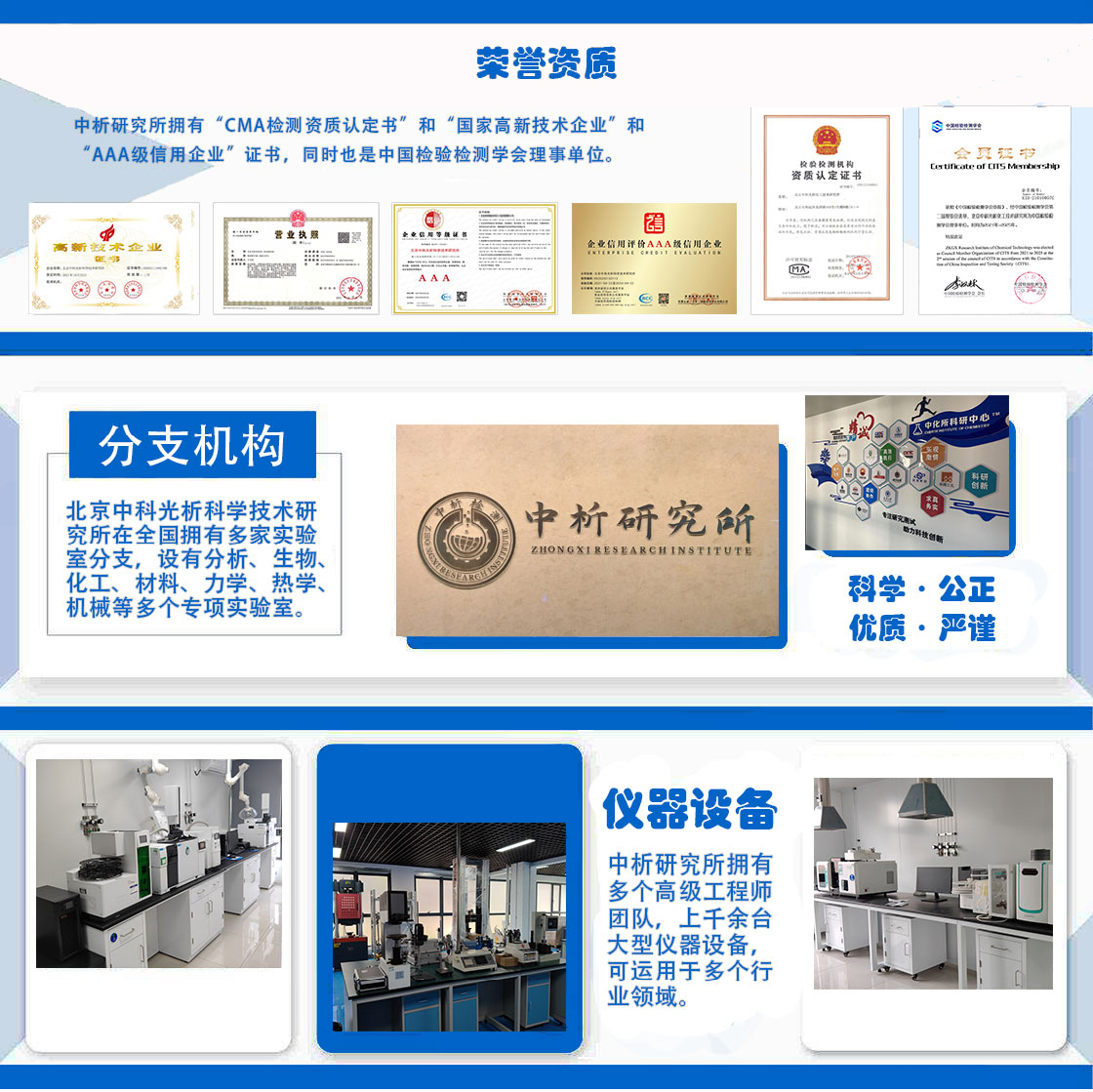
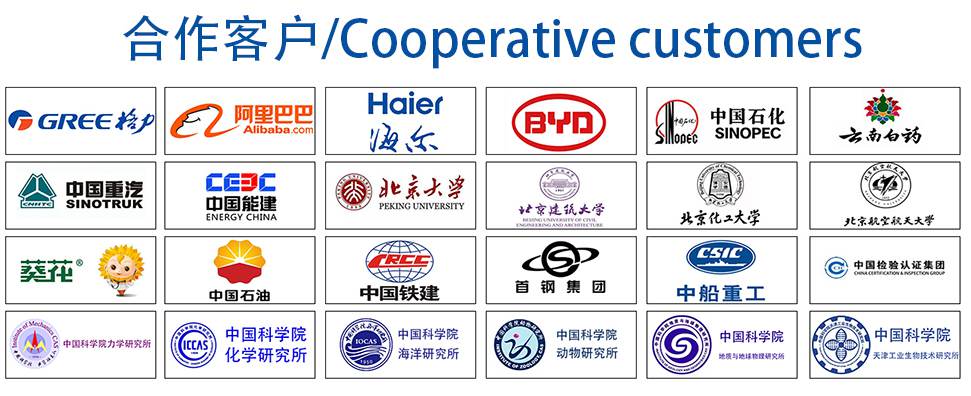
材料实验室
热门检测
317
269
240
247
246
244
257
252
269
267
251
257
254
254
244
243
260
240
254
251
推荐检测
联系电话
400-635-0567