机械采油系统检测:保障油田高效运行的关键环节
机械采油系统作为油田生产的中枢环节,承担着将地层原油提升至地面的核心任务。随着油田开发进入中后期,设备老化、工况复杂化等问题日益凸显,系统检测已成为预防故障、延长设备寿命、提升采收率的重要手段。通过系统性检测可及时发现抽油机、抽油泵、井下工具等关键部件的潜在隐患,减少非计划停机造成的经济损失,同时保障作业人员安全。现代检测技术已从传统人工巡检向智能化、数据化方向升级,形成了包含机械性能、电气参数、动态监测的全方位检测体系。
核心检测项目及技术要点
1. 抽油机系统检测
重点检测几何参数(悬点运动轨迹、冲程冲次)、动态平衡度、结构稳定性。采用激光测距仪测量驴头悬点位移,使用振动传感器监测曲柄箱、减速箱的振动频谱,通过扭矩仪测试系统载荷分布。对于游梁式抽油机需特别关注游梁支撑轴承磨损状态,皮带传动机型应检查皮带张紧度及磨损情况。
2. 抽油泵工况诊断
通过示功图分析泵效,利用井下压力计测量泵吸入口压力,结合电参数据计算有效冲程。重点检测柱塞与泵筒配合间隙(通常控制在0.05-0.15mm)、凡尔开闭响应时间,采用声波检漏技术定位气锁位置。对于稠油开采场景需增加泵腔结蜡监测,应用温度传感器实时监控泵体温度场变化。
3. 井下工具检测
使用多臂井径仪检测油管变形,磁记忆检测技术诊断杆管疲劳损伤,电子多点测斜仪监测井斜变化。重点检查抽油杆接箍螺纹完整性、扶正器磨损量(超过壁厚30%需更换)、加重杆配重平衡度。对于腐蚀严重区块,需定期进行管壁厚度超声波检测和硫化氢浓度监测。
4. 驱动装置检测
电机检测包含绝缘电阻(≥500MΩ)、三相电流平衡度(偏差<10%)、轴承温度(≤85℃)等指标。减速箱需检测齿轮啮合间隙、润滑油金属颗粒含量,使用热成像仪排查异常发热点。对于变频控制系统,应校验输出频率精度(误差≤0.5Hz)和电压谐波畸变率(THD<5%)。
5. 润滑系统检测
定期取样分析润滑油粘度(40℃时ISO VG320±10%)、酸值(≤1.5mgKOH/g)、水分含量(≤0.1%)。采用铁谱分析技术监测磨粒尺寸分布,使用在线油品传感器实时检测污染度。对于集中润滑系统,需校验注油压力(0.2-0.5MPa)和注油周期准确性。
6. 安全装置检测
紧急刹车系统响应时间应≤0.5秒,安全销剪切力需符合设计值±5%。检测载荷传感器精度(误差≤1%FS),校验过载保护阈值设置(通常为额定载荷的110%)。防喷盒密封压力测试应达到工作压力的1.5倍,持续30分钟无渗漏。
7. 系统能耗检测
通过功率分析仪测量系统输入功率,结合产液量计算吨液耗电量(齐全值≤5kWh/m³)。检测平衡度(电流平衡率≥85%),分析无效功占比。对于高耗能设备,需开展永磁电机改造、智能间抽控制等节能检测验证。
8. 环境适应性检测
在高温工况(>60℃)下测试密封件耐久性,低温环境(<-20℃)验证润滑油流动性。沙尘地区需进行防尘密封检测,沿海区域开展盐雾腐蚀测试。针对地震带油田,应评估设备抗震性能(满足VIII度设防要求)。
检测技术发展趋势
随着物联网技术的普及,机械采油系统检测正朝着智能化方向发展。无线传感器网络可实时采集20+项运行参数,大数据分析平台能提前14天预测故障发生概率,数字孪生技术实现了虚拟调试与工况模拟。2023年行业数据显示,实施系统化检测可使检泵周期延长40%,系统效率提升15%以上。
科学的检测管理体系应包含日常巡检(每班次)、预防性检测(月度)、全面诊断(年度)三级机制。建议油田企业建立设备健康档案,采用RCM(以可靠性为中心的维修)策略,结合检测数据优化维保方案,最大限度发挥机械采油系统效能,为我国油气稳产增产提供坚实保障。
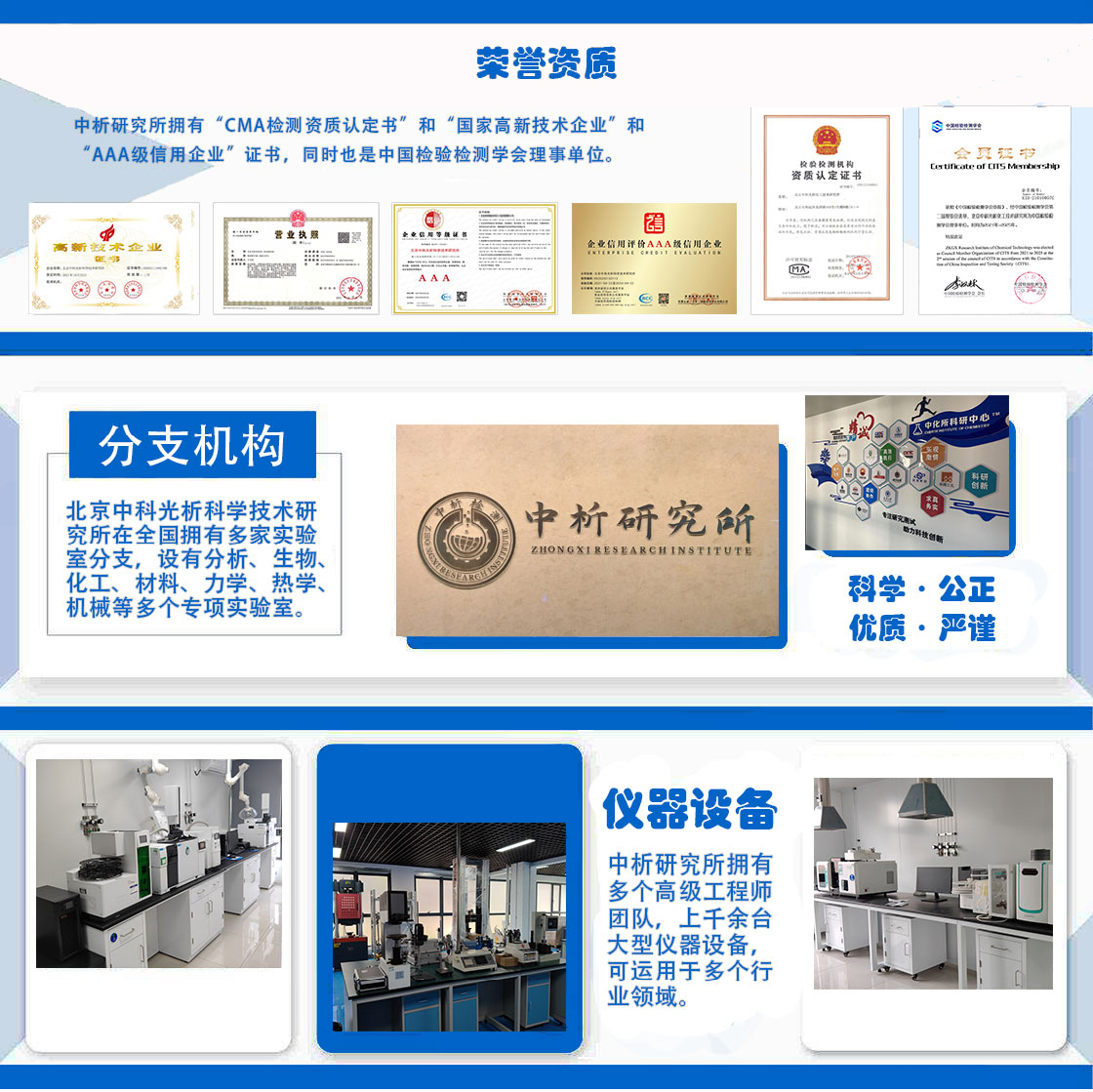
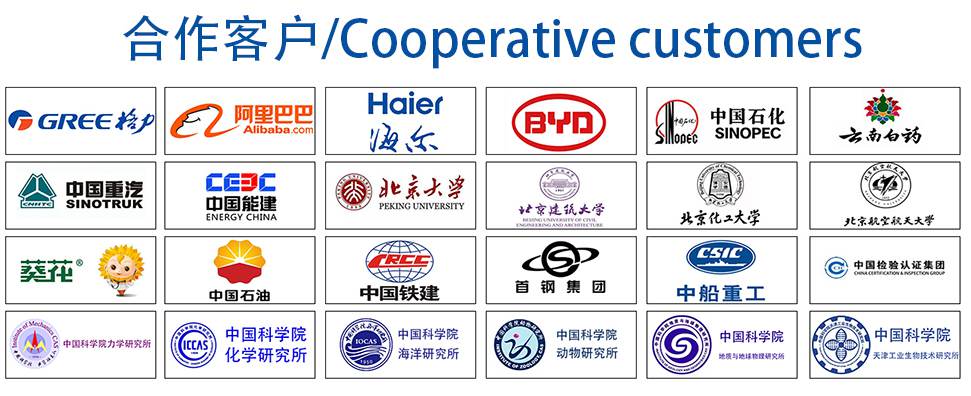